The substitution of original quality materials for cheaper, lower quality ones is an unfortunate but very recurring problem in products made in China and elsewhere. By performing regular checks throughout production, or by working with a trusted third-party QC company to act on your behalf, you can be sure the materials used in your product meet specifications.
Some of these tests and checks can be done on-site at the factory, while others require samples be sent out to an accredited laboratory (see Product Testing and Product Inspection – What’s the Difference?). Whether you hire a third-party QC company, arrange for your own staff to inspect or rely on the factory’s internal QC procedures, it is important to know what kinds of tests and checks you need.
Products that contain leather, for instance, are often susceptible to issues related to the quality of the leather used in production. So let’s look more closely at leather for the sake of breaking down product inspection and lab testing for quality of materials.
1. Product Inspection to Check Material Quality
Inspection of regular random samples, of both incoming raw material and in-production or finished product, is particularly important for leather (see Don’t Neglect Incoming Quality Control for Parts and Materials). Since natural leather is made from animal skins and cannot be ordered in huge mass-produced and consistent bolts like fabric, quality can very drastically within a batch. If the factory tries to cut costs by mixing a few batches of lower quality skins, you are unlikely to find these lower quality units if you only pull a sample of 2-4 pieces out of 100,000 pieces for a single round of expensive lab testing. On-site inspection, on the other hand, is relatively inexpensive and verifies a much larger volume of units.
That being said, the degree of confidence product inspectors can have saying “all these units are made of quality leather” is limited by their environment, equipment and training. While there is no way to truly check what type of animal a piece of leather came from during an inspection, there are some standard checks that can be performed including:
- Checking vein, texture, and smell of the material – all of which are pretty unique to real leather. Most experienced inspectors can easily identify synthetic leather this way.
- Burn test – real leather will not easily burn, and if it is fake, there is usually a distinct smell of burning plastic.
For more on product inspections, check out The Buyer’s Guide to the Product Inspection Process.
2. Certification and Lab Testing of Materials
As mentioned above, lab testing can be costly and time consuming. Also, lab testing typically only checks one or a few pieces of material out of a large order. Samples are usually pulled before production and, depending on the length of a project, once or twice farther down the production line (see What is a Product Testing Lab?).
Despite this, lab testing is the only real way to verify that quality of the raw materials used meets your design specifications. In this case, this is the only way you can really verify the leather comes from a cow. Depending on how your product is used, this is often the only way to certify that your product and its component materials comply with your local regulations for health and safety.
Unless you really are an expert in the material and product you are buying from abroad, you may want to speak with a combination of lab service providers, QC companies and compliance experts to know what tests you really need to conduct and when.
Conclusion
Like all parts of quality control, ensuring the quality of your product components and raw materials is an ongoing process. To make sure your product is only made using the exact standard materials you want, both cautious investigation of suppliers before starting a project, as well as regular check-ups, typically through product inspection, are required.
Regardless of how good your supplier may be at actually creating or assembling the final product you buy, the quality of that item is only as high as that of its parts and materials. In order to prevent low quality materials from ending up in your product, remember:
- Inspect both the factory and the product - Try to work with factories you trust, but be sure to do due diligence both before and after placing an order.
- Quality control requires a multi-pronged attack strategy – Labs and on-site inspections both have their pros and cons, but you may need both to ensure the quality of your product.
If you don’t keep a watchful eye over manufacturing of your products, you may be purchasing inferior goods without realizing until you receive the finished product.
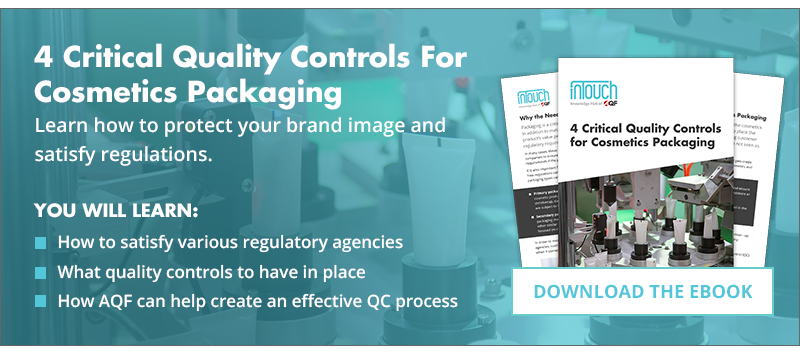