Organized and disorganized factories have one thing in common: problems can occur at any time and affect production. A disorganized factory will typically be more prone to issues. But that’s not to say an organized factory is immune to accidents, setbacks and poor product quality. All factories are vulnerable, especially those working with more complicated products (related: 4 Challenges of QC for Complicated Products).
Since problems can occur at virtually any point in manufacturing, that might leave you guessing from where certain defects or delays originate. Product inspection at any given stage in the manufacturing cycle only gives a snapshot of the product and order status at that time.
But production monitoring, having an inspector at the factory regularly, gives a fuller picture of what’s happening not only at one place, but throughout the factory. In fact, many importers that have continued to have a variety of quality problems at a single factory often insist on production monitoring to help solve them.
Here are three reasons to conduct production monitoring:
1. Production monitoring offers a wide view of manufacturing
One of the main benefits of production monitoring is that it gives you a wide look at all the manufacturing processes at work in the factory. It’s typically a combination of all three types of product inspection:
- Early product inspection at the start of production, giving insight into the status and quality of parts and materials used (related: Don’t Neglect Incoming Quality Control for Parts and Materials);
- During production, or “DUPRO”, inspection looking at a product as it’s moving through manufacturing stages; and
- Final inspection, checking a product when most units are already finished
Inspection at a particular production stage can be helpful for most importers. But rather than having a limited view of a product at one area, production monitoring reveals the whole spectrum of manufacturing. This can be beneficial in a number of ways, including revealing how factory workers operate and the implications for your product.
Operating procedures for factory workers
Besides seeing your products as they move throughout the factory, production monitoring lets you see how the factory operates. Your inspector can report on how factory workers handle the product and its materials. They can also tell what procedures workers seem to be using or what kinds of best practices the factory may be lacking.
For example, well-established and efficient factories often have work instructions at workstations. These detailed, yet easy-to-follow, instructions save workers time and help prevent quality defects caused by worker errors during production and assembly (related: Why Your Factory Needs Work Instructions).
Factory management may refuse to grant the inspector access to certain parts of the facility. And there may be hidden details about the way the factory operates. But production monitoring can illuminate areas where the factory, and your product, might benefit from improvement.
2. Production monitoring helps prevent shipping delays
Production and shipping delays are among importers’ most common frustrations when working with suppliers. And one of the major causes for delays is a general lack of transparency. Production monitoring—and to a less extent, product inspection—offers transparency to help importers forecast and prevent delays that might otherwise lead to customer dissatisfaction.
Factories prioritizing customers
Sometimes even placing an order with a factory months in advance doesn’t guarantee there won’t be delays. One reason is because factories usually work with multiple customers at a time. And factory managers tend to give a higher priority to some customers than others, mainly based on these factors:
- Order quantity;
- Order frequency; and
- Relationship with the customer
A factory incurs some expenses each time it needs to change the product it’s manufacturing. Purchasing staff at the factory often need sub-suppliers to arrange parts and materials for the next product. Factory equipment may need to be recalibrated, or even purchased, to handle the next order. And factory workers may need additional training when switching to another product with different specifications and requirements.
A preference for more profitable customers
Naturally, factory owners and managers prefer to work with more profitable customers. A customer ordering goods in a higher quantity or ordering shipments more often typically offers high margins for the factory. Factory managers also tend to prefer working with customers they’ve worked with before, as business with them is generally more predictable. All these factors also help to reduce variance, which improves the efficiency of factories.
The result is that factories may take on smaller customers but grant a higher priority to those that are more profitable. Without you being at the factory, your supplier can make up excuses for delays that allow them to move a different order ahead of yours. But production monitoring helps you confirm any real delays and their origin.
Consider an order of 3,500 ballpoint pens, for example. Your supplier emails you a week before you expect the goods to ship and says the factory needs at least two weeks. When you send your inspector to the factory for production monitoring you find the factory hasn’t even started. Instead, the workers are producing pens for a much larger customer. Knowing this, you can address the problem directly with the supplier and get production back on track.
Using a Gantt chart to track production
Some importers find they’re able to prevent delays by using a Gantt chart together with production monitoring to track production. Gantt charts are visual schedules often used in project management to keep track of deadlines. Importers can use the same kind of document to track production milestones and confirm whether a factory will meet their shipping deadline.
For example, let’s say you’re manufacturing promotional baseball caps at a factory in Ho Chi Minh City, Vietnam. All the hats need to be produced by September 5, embroidered by September 12 and packaged by September 22. You can document these deadlines in a Gantt chart of your own. Then your inspector can check the Gantt chart of production deadlines against what’s actually happening at the factory and report the progress.
By regularly updating the Gantt chart with each factory visit, you can confirm right away when the factory isn’t meeting deadlines. Then you can address it with your supplier directly and discuss ways to prevent or limit shipping delays (related: 3 Ways Experienced Importers Avoid Production Delays).
3. Production monitoring identifies issues as they occur
When you discover product defects after production has finished—or worse, after the goods have shipped—they can be difficult to correct. Besides potentially needing to unpack and repack finished goods, product repairs or rework can be time-consuming and costly. That’s why defects and other problems are much easier to remedy when they’re caught early.
Production monitoring entails having an inspector on-site and checking the product daily, or almost daily. Since they’ll typically check the product at every active production stage, the inspector can note any product issues and notify you that day. Following their report, you could then advise the supplier of any issues found and prevent them from affecting the entire order.
Let’s look again at the earlier example of baseball caps. Maybe there’s a problem with the embroidery on one of the SKUs. But you don't inspect the hats until after workers have finished and packaged them. Because the embroidery process is automated, the problem is likely going to affect all the units of that SKU. But with production monitoring, the inspector would’ve noticed the problem with the embroidery almost immediately.
For some factories, this early detection of problems can be especially helpful. Management and workers may be accustomed to reworking defective products. But having an inspector identify defects before the goods reach their customer saves them from wasting time, and possibly, from losing that customer’s future business. And helping a factory improve its manufacturing processes often improves the relationship you have with your supplier (related: 3 Tips for Stronger Supplier Relationships).
Process auditing for determining root causes for issues
There’s a difference between identifying product defects and other issues and pinpointing their root causes. Product inspectors can often point to the production processes which are introducing particular defects. They may even be able to sometimes suggest potential causes. But they typically cannot analyze a process to determine how to fix problems.
An importer that desires a greater amount of improvement in a factory’s operations can opt instead for a process audit. Process auditing is normally conducted by manufacturing consultants who closely examine the production processes themselves. These consultants generally find the root cause of any problems and help factory staff implement solutions.
Production monitoring is still useful in detecting problems early so the factory can address them. But if factory management are unable to fix specific problems, a process audit can be the best way forward.
Conclusion
Different types of inspections are suitable for different types of factories, products and problems. Production monitoring can be an unnecessary or expensive QC option for importers working on a tight budget or with a factory that has a history of adequate product quality. You might find you only need to conduct a final inspection before shipping. Other importers may find that they need the more complete oversight that production monitoring provides.
Production monitoring gives you knowledge of the entire manufacturing cycle, points out any defects at all stages and helps prevent shipping delays. And when you understand and control your manufacturing from start to finish, that can only mean two things: better product quality and happier customers.
How has production monitoring helped or hurt your product quality? How about your relationship with your supplier? Share your experience in the comments below!
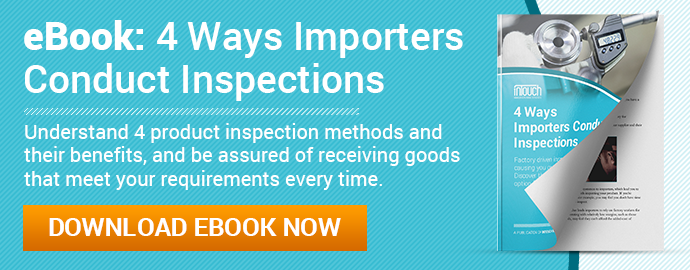