Fashion brands need to satisfy various regional and international standards for manufacturing their products. If you’re planning to sell or manufacture fashion apparel or accessories in the U.S. or EU, you need to be up to date on the latest standards or risk being stopped at customs.
This article will list some of the most important standards and explain how third-party quality control partners can help brands stay aligned with expectations.
Material Safety Standards
Garments and fashion accessories are designed to come into direct contact with the skin. Therefore, material safety standards are in place to ensure that products can be worn safely and do not contain chemicals or substances that may harm consumers.
Brands and retailers of fashion products should be aware of the following regulations:
REACH
The Registration, Evaluation, Authorization, and Restriction of Chemicals (REACH) is a regulation in the European Union (EU) that places responsibility on brands and retailers to identify and manage risks associated with the substances found in their products. Common examples of restricted materials may include:
- Inks and dyes
- Nickel
- Lead
- Cadmium
- Formaldehyde
- Phthalates
Since non-compliance can lead to legal consequences, product recalls, and reputational damage, overseas companies may feel a need to seek professional assistance from a third party to ensure compliance with their REACH obligations.
CPSIA
The Consumer Product Safety Improvement Act (CPSIA) in the U.S. intends to enforce stricter requirements for product testing and documentation. It addresses a wide range of products, including clothing and accessories intended for children, such as jackets, rompers, sleepers, hats, necklaces, bracelets, and more.
Under the CPSIA, brands and retailers must:
- Rely on third-party testing and certification of certain children's products to ensure they comply with safety standards before they are placed on the market.
- Use accredited testing laboratories to verify compliance.
- Show that their products do not contain harmful levels of substances such as lead and phthalates.
This applies to all companies based in the U.S. that make or sell children’s clothing and accessories. It also applies to non-US companies that wish to sell their products in the U.S.
Product Labeling Standards
Product labeling standards for manufacturing fashion accessories are essential for providing consumers with important information about the product's composition, care instructions, and safety considerations.
While specific labeling requirements may vary depending on the region and type of fashion accessory, some common labeling standards include:
CARE labeling
CARE labeling refers to the standardized label found on clothing and textile products that provides essential care instructions for consumers. These labels are typically sewn into the inside seam of garments.
The care symbols used on the labels are standardized and typically follow the guidelines provided by the International Organization for Standardization (ISO) in the ISO 3758:2012 standard. These symbols are designed to be internationally understood, making it easier for consumers to care for their clothing, regardless of where the garment was manufactured.
Under the CARE labeling rule, brands and manufacturers must:
- Provide complete instructions about regular care for the garment
- Ensure that these instructions will not cause harm to the product
- Include warnings about certain actions that would harm the product, such as "do not iron" or “dry clean only.”
Brands and retailers must attach CARE labels to finished products before they sell them. Overseas retailers must ensure that CARE labels are attached to products before they sell them in the U.S., but CARE labels don't have to be attached to products when they enter the U.S.
Jewellery Standards
Manufacturing fashion accessories, particularly jewelry, involves adhering to various standards and regulations to ensure product safety, quality, and compliance with ethical and environmental considerations.
Here are some common jewelry standards and considerations, although they may vary depending on the type of jewelry and the region of sale:
ASTM F2923-14
ASTM F2923-14 is a standard specification issued by ASTM International that pertains to consumer product safety for children's jewelry. The standard aims to reduce the risk of potential hazards associated with children's jewelry, particularly concerning the presence of harmful substances. It addresses various aspects related to the safety of jewelry intended for children, including:
- Lead Content
- Nickel Release
- Chemical Requirements
- Mechanical Hazards
Manufacturers, importers, and retailers of children's jewelry should adhere to the requirements specified in ASTM F2923-14 to ensure their products are safe for young consumers. Compliance with this standard demonstrates a commitment to consumer safety and may be necessary to meet legal requirements in some jurisdictions.
Achieve Compliance with AQF On Your Side
As a brand or retailer of fashion accessories, it is vital that you carefully review the regulations that apply to your product before selling it in the U.S. or EU. Working with a reliable third-party can help to ensure compliance with relevant standards so you can focus on what you do best: developing great products.
AQF provides a variety of quality control solutions, including raw material inspection and safety compliance testing. We can leverage the services and expertise of a network of laboratories that sit under WORMS SAFETY LABORATORIES to help protect your brand and consumers.
Contact us today to learn more or use AQF Online to book your next service.
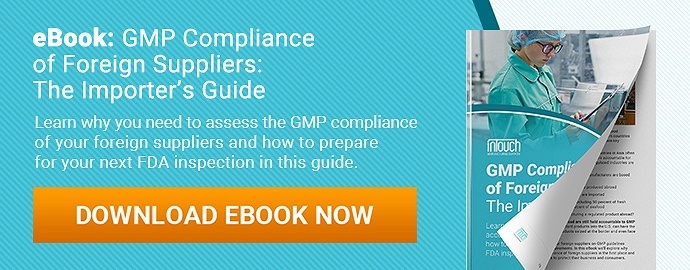