Have you ever received a product inspection report that left you wondering why some details were included and others weren’t? Maybe you had questions that weren’t answered in the report. Or maybe you thought the scope of inspection would be significantly larger than what you see in the report.
Whatever your experience was, chances are, you’re not alone.
A product inspection report can be a very useful tool that gives you a clear picture of the quality of your products.
But it’s not a silver bullet.
You should use the report to make more informed decisions regarding your product and shipment, as opposed to expecting the report to solve all of your problems on its own.
It is important to know about these four things an inspection report will not tell you:
1. Product inspection reports will not tell you whether or not to ship
A lot of importers mistakenly think that the result of the QC inspection will directly dictate whether or not to ship the goods.
Don’t over rely on the official report result
Your inspection report will typically give a result such as “PASS”, “FAIL” or “PENDING” (Related: What is a “Pending” Result?). But just because your inspection report might show a passing result does not mean your supplier has the authority to ship the goods. Likewise, if your inspection report shows a failing result, you still have the authority to hold the shipment.
For example, say you are importing stadium seats and the inspection result is “fail” due to a minor defect, some scratches on the underside of the chairs present on 20 percent of the sample size inspected. You may decide this defect is acceptable, even though your inspector issued the report with a result of “fail”. In this case, you can tell the supplier you approve the order for shipping.
The importer usually makes the final decision about shipping, not the inspector or the supplier. So it’s important that you use the product inspection report as information to help you decide, instead of relying only on its official result to determine whether or not to ship.
Be sure to provide feedback on reporting
It’s also important to understand to let your inspector know if you don’t agree with the result shown in the report. Whether you feel inspection criteria should be tighter or looser, offering feedback to your inspector and supplier will help you get more accurate reporting in the future.
2. Inspection reports will not tell you about every piece in your order
Some importers think that product inspection is typically carried out on their full order. Others think that sample sizes are chosen somewhat arbitrarily for inspection. But actually, both conclusions are wrong.
Inspection of 100 percent is impractical
In most cases, it’s impractical and costly to inspect every item in a shipment, which is why inspectors will often inspect a random sample of product pulled at the factory. Inspection of 100 percent of an order is more feasible when:
- Your order size is smaller relative to the time needed to inspect each piece
- You’re inspecting a high-ticket item (i.e. jewelry), or
- You’re placing a trial order with a supplier or working with a supplier for the first time
Sample sizes are chosen based on a specific standard
Secondly, the sample size for inspection is usually determined by AQL levels you or your inspector set based on the total quantity of pieces in your order. The larger the sample size, the more accurate the representation of quality in your shipment. You’ll get a less transparent view of your order by inspecting a smaller sample size.
You can inspect without using the internationally-accepted AQL standard, but it will make interpreting the results more difficult, since AQL relies on statistical sampling to determine pass or fail. Most professional inspection companies can give you a few options with different sample sizes for inspection based on AQL. So you don’t need to be an expert yourself in the all the ins-and-outs of AQL to understand inspection results.
3. Inspection reports will not tell you how to fix defects
This third point is not commonly known among first-time importers. And being aware of it upfront will help you avoid frustration and manage your expectations.
A professional inspection report will give you a thorough overview of the defects found in your products. Many reports will even include detailed pictures or video to give you a clearer understanding of the nature and severity of any defects found. However, one thing a product inspection report will not show you is how each defect got there in the first place OR how to fix it.
"A product inspection report will not show you how each defect got there OR how to fix it"
For example, if there are flow marks present on your water bottles there could be any number of causes related to injection molding, such as injection speed or pressure, temperature or a problem with the mold itself.
Diagnosing quality problems and finding solutions
An inspector with experience in your product type may be able to speculate as to the likely cause of or possible corrective actions for particular defects. But explanations like these are typically not covered in the inspection report itself. You might want to ask the inspector for their input. But ultimately, you’ll need to address quality concerns with your supplier directly, as it is the factory staff that are operating and maintaining the machinery.
Some importers opt for a more direct approach to reducing quality defects, such as hiring the services of a manufacturing consultant or carrying out what’s called a process audit to pinpoint root causes (Related: Process Auditing vs. QC Inspection). These are typically more expensive options and require more cooperation from the factory.
4. Product inspection reports will not tell you the state of the factory
Some importers hope to learn details of a factory, such as production capacity, number of workers and even financial information from a product inspection report. But gathering this kind of information simply isn’t part of the normal product inspection process.
A regular final or during-production inspection can give you an overview of a random sample of your product. It can tell you what percentage of your order is finished and packaged. And it can tell you if the goods are meeting your standards and requirements.
But a typical product inspection report will NOT tell you anything about conditions, level of sophistication, worker safety or other factory information not directly related to the product inspected.
Auditing the factory instead of the product
There are a number of different standards applied to factory audits that will give you this kind of information, including:
- ISO 9001 (used for evaluating a factory’s Quality Management Systems)
- SA8000 or brand/retailer standards (used for determining a factory’s level of social compliance)
- ISO 14001 (used for evaluating Environmental Management Systems)
At the very least, a preliminary audit of a factory’s Quality Management Systems is always advised before working with a supplier for the first time. This will tell you about your factory’s legitimacy, number of staff, production capacity, internal QC, whether they have an export license and much more.
Conclusion
Carrying out product inspection before shipping can tell you a lot about the status of your order and the quality of your products. But it’s important to understand what an inspection report will not tell you.
As a buyer, it is important for you to be in regular communication with your supplier to address any issues found in the reports. Make sure they understand that only you grant approval to ship.
Most importantly, if you have questions about what to expect from a product inspection report, don’t be afraid to ask your inspector directly. You may even want to ask them for a sample report for a similar product to get a better idea.
Knowing what to expect in reporting beforehand can save you a lot confusion later on.
Be sure to listen in on Stacy Bruce and John Niggl discussing this topic in the manufacturing podcast!
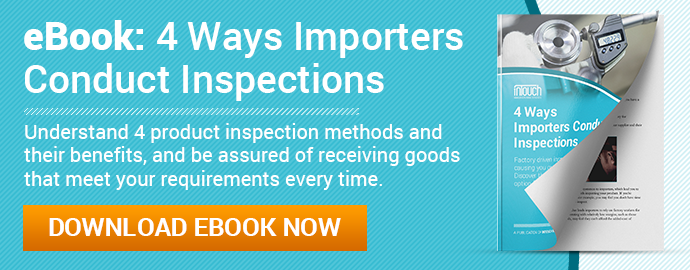