As a business owner, you want every aspect of your business to run like a well-oiled machine as often as possible. When it comes to quality control for your products, the process isn't a one-size-fits-all or "set it and forget it" method. As your business grows and changes, your quality control process will need to be revisited periodically.
Read on to discover some of the telltale signs that your quality control service is in need of adjustments.
How to Tell When Your Quality Control Service Needs Improvement
If your business begins to spot any of the following warning signs, it's incredibly important to rectify the situation immediately to protect your business's reputation, keep your customers satisfied and coming back for more, while minimizing lost profit.
1. You're Receiving More Customer Complaints
If you're noticing an uptick in complaints from your customers about issues they're experiencing with your products, that can be a huge red flag that something is wrong somewhere in the production process. Whether the issues are arising during the manufacturing process, pre-shipment, or in-transit, you'll need to identify what's causing the problem so you can correct it before you upset more of your customers.
2. Your Customer Service Team Is Overwhelmed with Support Tickets
Similar to receiving an influx of customer complaints, if your customer service representatives report that there is an increase in support requests, that can also indicate that there are defects occurring in your products' manufacturing. Pay close attention to what your customers are saying is going wrong to help you identify what needs to be adjusted or reworked in your products to solve the issue.
3. The Number of Returns or Refund Requests Is Rising
A steady or even drastic increase in returned products or refund requests from your customers is a clear warning sign that many of them are unsatisfied with your product. Whether it's defective items being missed in your quality control checks, inadequate packaging leading to damaged products during the shipping process, that is making your customers unhappy, it's important to find and fix the issue as soon as possible.
4. Too Many Products Are Failing Your Quality Control Inspections
Low-quality or downright defective products are bound to crop up every once in a while, but if your business is experiencing an increase in items failing your quality control checks, then something is clearly going wrong in the production process. To reduce the losses for your business, you'll want to identify and resolve the issue immediately.
5. Failing Product Inspections
While no business owner wants to fail a product inspection, it can act as a necessary wake-up call to pinpoint issues that your business is facing and provide an opportunity to improve your quality control service and eliminate many of the same problems from recurring in the future.
Set Your Brand Up for Success with Asia Quality Focus
Quality control service is an essential process for the continued growth and success of your business. To ensure the best quality control inspections for your products and a quality check process that doesn't let anything slip through the cracks, contact us today and get started with Asia Quality Focus quality control along your supply chain.
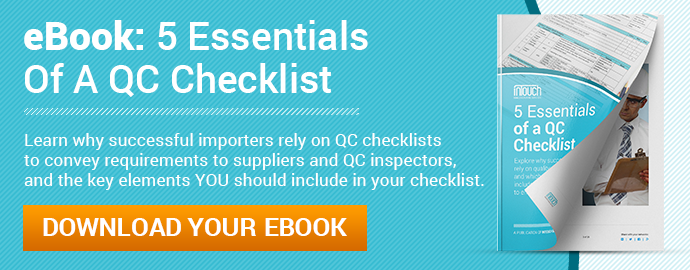