The furniture business has never been better and with much of the world looking to purchase furniture for growing families, businesses, and enterprises, quality is more important than ever.
The quality of your products is critical to producing an item your customers will love. It’s also essential for another reason: the quality of workmanship contained in your furniture determines whether customers will come back for more.
Excellent quality pieces result in loyalty and trust between your customers and your company. Shoddy work, mismeasured parts, and pieces that don’t fit together when your customer is ready to assemble will end up leaving them frustrated and unhappy.
When a customer receives a piece that is less than excellent, they’ll not only turn to you asking why they received such a product, but they’ll also turn to social media and let everyone else know about it, too.
Thankfully, these mistakes can be avoided and you can ensure you manufacture quality products that people love. Here are five ways to avoid these issues and create pieces that boast excellent workmanship and fine quality.
1. TALK WITH YOUR TEAM
When you’re manufacturing a piece of furniture, be it a table, a chair, or a couch, you don’t complete the process alone. You have an entire team that works with you and, for this article, we’re not simply talking about your in-house design team. We’re also talking about the manufacturers you use to produce your furniture pieces. The people who work in the manufacturing warehouse cutting, piecing together, priming, painting, drilling, and preparing your one-of-a-kind furniture pieces are also on your team.
No one single person on your manufacturing team is responsible for all quality control issues. So, if you want to ensure that your pieces are being produced to the highest standards, it’s important that you communicate with your entire manufacturing team.
If you’re searching for the source of a problem with quality, it’s important to use the same strategy. Gain the perspectives of your manufacturing team to get to the bottom of an issue. Go well beyond the yes and no questions – and be willing to listen and learn.
Ask your team to describe the manufacturing process to you. Ask where they feel ill-equipped to manufacture a product. Seek information regarding their process and find out:
- Where misinformation is getting spread.
- Where mistakes are getting made.
- How misunderstandings are making their way into the manufacturing process.
2. DETERMINE QUALITY BASED ON YOUR CUSTOMER’S PREFERENCE AND PERSPECTIVE
If you find yourself concerned that your furniture products aren’t the best on the market, or you find yourself wondering how you can make them “better,” it’s important to figure out what “better” means – to your customer.
You may think upgrading the lining or upholstered fabric will make a better product – but your customers will shy away because it doesn’t meet their need for a budget-friendly, utilitarian piece. You might decide that crafting a six-drawer desk from luxury woods will make your furniture better – but your customers may prefer reclaimed wood and something more minimalistic.
Understanding what your customers need and want is critical to crafting quality pieces that hit home once they reach the marketplace. This is a critical part of customer value management. Without gaining a clear understanding of customer wants and needs, you could end up crafting the very best piece of furniture available only to watch your sales and profits suffer.
3. COMMUNICATE THE COST OF QUALITY
As a business owner, you are well aware that it’s far less expensive to fix a quality control issue before it leaves the manufacturing floor than it is to make good on a warranty repair or replacement promise.
This fact should be communicated to those on your team, including your manufacturing team. Train your manufacturers to own the job of inspection and catching defects before each piece leaves the warehouse. Then, promote the process of finding defects, flagging them, and solving them before the item ever reaches the customer.
Your manufacturing team wants to produce excellent quality pieces. So, when you’re training them to catch quality control issues, it’s vital that they understand that catching those mistakes is a good thing. The focus should never be “who did this wrong?” but “great job for catching that mistake!”
If you start looking for the person who “did it wrong,” everyone will hang their heads, no one will speak up, and you’ll continue having quality issues. On the other hand, if you celebrate mistakes being located, then you can focus on the root cause and create a solution to fix it.
There may be cases where quality issues come from negligence or even intentional deviation from the process that those responsible may rather cover up. It may be beneficial to establish a whistleblowing system so anyone on the manufacturing team can alert you to issues without fear of reprisal.
4. COMPLETELY SOLVE QUALITY ISSUES
One of the biggest mistakes manufacturers can make is finding and fixing the symptom of the problem rather than discovering the root cause.
When you’re hunting down the root cause of the quality issue, it will take more than setting up an extra inspection station or a place to rework a piece with a quality problem.
Instead, keep going all the way to the root cause of the issue. Once this is discovered, your manufacturing team won’t need to set up reworking or reinspection stations because the problem will no longer exist. Creating a true solution will result in the quality control issue vanishing for good.
5. DETAIL YOUR PROCESS DISCIPLINE
No one likes a hovering helicopter of a boss who squashes all attempts at innovation and creativity. In fact, a recent study found that 45% of manufacturing industry leaders report that rigid internal processes hamper their team’s ability to innovate. That said, when manufacturing furniture pieces, it’s vital that every person on the manufacturing team knows, understands, and follows your process discipline.
Furniture-making is an exact science and creativity happens on the drawing board before it reaches the manufacturing warehouse.
When pieces are getting cut, items are getting labeled, and assembly is a step away, the time for creativity is long past. Even a small deviation in the process could result in entire product lines getting scrapped because of quality problems affecting everything from safety to the overall look and design of the item.
While no one likes to be micromanaged, proper structure and process discipline must be maintained in the manufacturing warehouse to produce furniture pieces with consistently high quality. With a strong process discipline in place, it’s far easier to catch quality control problems and issues that arise down the line.
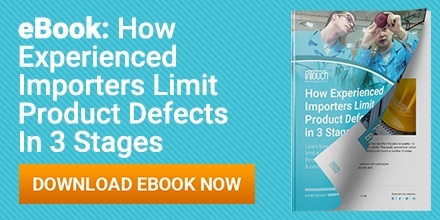