Best in Manufacturing – August 27, 2017
Each Sunday, we publish a list of top articles and other content related to manufacturing in areas like quality control, product development, supply chain management, sourcing, auditing and law.
1. Avoid getting hacked: improve IoT security with these defense tactics
The Internet of Things, or IoT for short, is remarkable. It’s enabling major technological leaps across society, whether in the form of smart homes, wearable electronics or intelligent factories. And this list barely even scratches the surface of IoT’s potential.
Unfortunately, despite its promising applications, IoT can be exploited to divulge valuable information or negative impact the real world. For example, one man was able to exploit vulnerable IoT devices in a prison by opening and closing cell doors. Thankfully, it was just a demonstration. Needless to say, a prison could be seriously compromised if someone decided to act on its IoT weaknesses.
In the context of manufacturing, malicious hackers might hold a factory enabled with IoT systems ransom to force production to start again (Related: Factories vs. cyberthreats – see #2). Or the hackers could collect valuable, proprietary data via IoT and sell it to competitors or elsewhere on the black market.
But the news isn’t all bad. There are ways to protect yourself against those that would seek to manipulate IoT systems for their own gain. The author of this featured article provides a few ways to make sure IoT systems can stay secure:
- Conduct an inventory of all your IoT devices
- Implement segmentation of IoT and other devices, like PCs and servers
- Configure firewalls and proxy devices
- Change default configurations
- Regularly install software patches to your devices
- Integrate your IoT devices into a system to log usage
If you’re curious about how you can use these steps to make sure your IoT devices don’t get exploited and used against you, check out the full article in the link below:
IoT Security: A Two-Pronged Defense Strategy for Manufacturers - Kiel Murray, Chris Reffkin and Chris Wilkinson, Industry Week
2. What “poka yoke” is and how it can help improve factories
Onomatopoeia is the formation of a word by imitating the sound that it’s referencing. Words like BOOM, ZOOM and WOOF, are examples of onomatopoeia representing explosions, high speeds and a dog, respectively. Yet in the case of poka yoke, I didn’t know if it was onomatopoeia for some weird animal that I never heard of as a kid or something else entirely.
As it so happens, poka yoke is actually Japanese for “mistake proofing”. This term is used as part of efforts to improve factory operations and other aspects of manufacturing, like making CAD designs.
The author of this featured article mentions six poka yoke techniques that you can consider implementing with your supplier’s or your own factory. I'll describe three below and you can see the others on the author's website:
- A change in a fixture design: make a product fixture impossible to place incorrectly
- Sensors that prevent processing under certain conditions: for example, use a proximity sensor to enable or disable processing when a part is within a certain distance
- A vision system: especially with the advent of artificial intelligence that can help analyze objects, a vision system can indicate the need to halt production until a change is made
Factories aren’t always perfect. Defects happen. And while it might be impossible to have completely defect-free production at the present, the insight offered by the author of this featured article can at least help you have a better manufacturing experience.
Check out the full article that covers poka yoke by following the link below:
6 Poka Yoke (Mistake Proofing) Techniques That Most Factories Overlook - Renaud Anjoran, China Manufacturing Consultants
3. Addressing the manufacturing skills gap with these future jobs
Technological advances like the Internet of Things and artificial intelligence are creating a new generation of factories. These new production facilities are capable of greater productivity, lower defect rates and more customization. In the transition to these new factories, however, some workers will lose their jobs.
But the news for workers isn’t all bad. Managing the new technology will require a different worker skillset, which can lead to unique opportunities for qualified individuals. This featured article lists and describes some of those opportunities. The manufacturers that hire for these positions might soon find themselves ahead of the competition when it comes to advanced manufacturing. The positions are:
- Chief digital officer (CDO): this person advocates for new technologies and spots areas where they can be used in an organization
- Digital manufacturing engineer: this person designs and creates what the CDO suggests
- Virtual reality (VR)/augmented reality (AR) system specialist: this person looks at early stages of product development to see where the organization can implement AR/VR to support its needs
- Worker experience designer: this person is focused on improving the experience of workers in an organization so they are more productive, have better morale and make fewer mistakes
- Digital factory automation engineer: this person looks for opportunities to implement automation
To learn more about these positions, check out the featured article in the link below:
5 Future Jobs that Could Solve the Manufacturing Skills Gap - Isaac Maw, Engineering.com
4. Reducing pollution in the denim industry
Whenever I put on my jeans, I rarely think about how they’re made. In fact, before reading this featured article, I had no idea producing jeans was so polluting and wasteful.
On average, it can take up to 10,000 liters of water to make a single pair of jeans. In most factories, the majority of untreated waste water–full of dyes and other chemicals–goes back into rivers and the ocean.
Industrial waste is no joke. Dyes recently turned dogs blue in Mumbai, India. And as this featured article reports, places like Xintang and Gurao in China are heavily polluted with the byproducts of jean manufacturing. The consequences to locals are an abnormally high level of fertility and reproductive problems.
The company mentioned in this article, Everlane, set out on a quest to avoid causing these types of problems. It partnered with a factory in Vietnam that shares its values and commitment to environmentally friendly manufacturing.
Some of this sustainability in action is the factory using solar panels and recycling 98 percent of its water with reverse osmosis machines. The polluted water is turned into potable water, thereby reducing the factory’s effect on Mother Nature.
It’s not always easy to integrate sustainability into manufacturing. But in doing so, companies let stakeholders know that they care about their impact on the environment and are doing something to address it.
Do you think sustainability in manufacturing is worth pursuing? Let us know in the comments section below!
To read more about sustainable denim, check out the full article in the link below:
Everlane’s Quest to Make the World’s Most Sustainable Denim – Elizabeth Segran, FastCompany
5. USA or China for prototyping
In an ideal world, your product idea wouldn’t have to go through many revisions to arrive at its final form. Really, however, prototyping is a fact of life in manufacturing. Prototyping is a necessary step toward understanding the look, feel and functionality of your item. It also serves as a valuable test for knowing what challenges you might face during mass production.
And when it comes to prototyping, some locations are simply better than others.
I’m personally of the opinion that Shenzhen is a pretty great place to prototype because there are many manufacturers, engineers, designers and other with the relevant skills all in one place. But in the opinion of the author of this featured article, the United States is a better place for prototyping for two main reasons:
- Intellectual property issues exist in China
If a supplier in China steals your designs and sells the finished product throughout the world, it might be difficult to receive restitution as compared to in the USA.
- Language and time barrier differences with China
The author points out that there are definitely people capable of speaking English in China, but not nearly as many people there have a native proficiency as in the USA. Additionally, trying to coordinate with suppliers and prototyping firms in China might be difficult because of the time difference, which could delay communication, production and prototyping.
While I’m not sure if the author has been to Shenzhen to see the rate at which new items can be prototyped, these points are worthy of consideration. The author also mentions a few resources the USA provides that can give it a bit of an advantage.
Find out about these advantages and more details about the differences in prototyping between these two countries by reading the full article in the link below:
Should I Prototype in the US or China? – Bryan Eagle, IoT for All
We’re constantly scanning the web for top manufacturing stories and news. If you’d like to submit an article for consideration for our weekly Best in Manufacturing, send us a message and let us know.
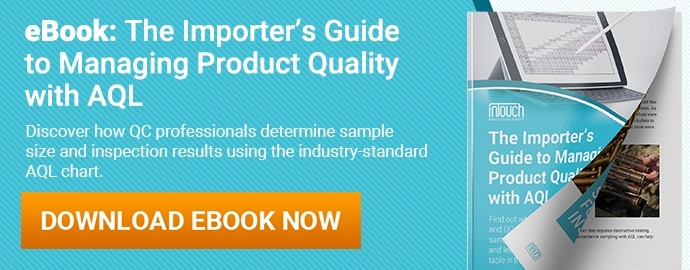