Navigating the intricacies of supplier quality management during relocation requires meticulous planning and strategic execution. Moving a business can introduce many challenges, from potential disruptions in the supply chain to maintaining quality standards. So, it’s necessary to approach the process with due care and diligence!
Assessing the need for relocation
Assessing the need for relocation involves a thorough examination of the factors driving the decision to move. By carefully evaluating the reasons behind the move, a company can determine if it's the right course of action. This assessment should include considerations like the need for a larger workspace, access to a more skilled workforce, or proximity to target markets. Additionally, potential disruptions to supplier relationships should be weighed, as shifting locations can impact the supply chain. Brands can also explore alternative solutions, such as optimizing the current workspace or improving logistics.
Be extremely thorough and meticulous in your planning for relocation!
Preparing a moving plan
When preparing a moving plan, start by assembling a dedicated team with members who possess the expertise needed for a smooth move. Clearly outline your goals and objectives for the move, making sure they align with your company's broader mission. Then, develop a detailed timeline, ensuring that every task has a set timeframe, and create a budget that considers all expenses, including unforeseen ones. Effective communication with your team and stakeholders is key, as it keeps everyone informed and engaged throughout the process. Lastly, regular reviews of your plan allow for adjustments as needed, ensuring that your relocation remains on track and within budget.
Communication with suppliers
Effective communication with suppliers is a cornerstone of supplier quality management during relocation. Open and transparent dialogue is essential, so notify your suppliers about the relocation plan well in advance, keeping them in the loop regarding timelines and expectations. Address their concerns and questions promptly to maintain strong relationships, too. Still, it's also wise to insist on pre-shipment quality inspections to ensure that the products meet your standards before the shipment. Involving them in this crucial phase reduces the chances of receiving subpar goods post-relocation or even during it. Besides, maintaining a strong rapport with suppliers and emphasizing pre-shipment quality inspections helps mitigate risks and promotes trust and reliability.
Clear communication strengthens your cooperation with partners and keeps things moving!
Supplier evaluation and selection
Evaluation and selection are fundamental for supplier quality management during relocation. So, assess the performance of your current partners, examining their ability to adapt to the new location. Consider new suppliers at the relocation destination, evaluating if they align with your quality standards and expectations. Due diligence on prospective partners is crucial, from checking their track record to verifying their capabilities. If the move has you busy, you can consider outsourcing quality control to a trusted third-party. This measure can help maintain the quality of your operations while you focus on the moving process.
Risk mitigation strategies
The first step in risk mitigation is to identify potential risks associated with supplier quality during the move. This includes assessing the possibility of disruptions in the supply chain, delays, or quality issues. To prepare, develop contingency plans, like maintaining safety stock or dual sourcing, to ensure a consistent supply of critical components. These strategies act as safeguards, helping your business weather unforeseen challenges during your move. A proactive approach also involves regular monitoring and assessment of your supply chain's resilience. By doing so, you can swiftly adapt and make necessary adjustments, minimizing the impact of any problems if they occur.
Supplier audits and assessments
Conducting regular audits ensures that your suppliers adhere to the agreed-upon quality parameters. So, this step provides transparency and identifies areas for improvement. Implementing ongoing performance assessments is equally important. It allows you to track performance over time, spot any deviations, and make the right decisions. Establish key performance indicators (KPIs) for suppliers to provide a measurable way to gauge their performance. These KPIs can encompass factors like delivery timeliness, product quality, and communication responsiveness.
You should always be on the lookout for new potential business partners!
Employee training and skill development
Investing in employee training and skill development is the linchpin of a successful relocation. When employees are well-prepared, they can adapt to the challenges and changes that come with the move. Providing training on supplier quality management best practices ensures that your team understands the importance of maintaining high standards. Skill development programs also enable employees to navigate the intricacies of a relocation seamlessly. Furthermore, Here & Now Movers Maryland can attest that well-trained employees make every aspect of a relocation easier. They can coordinate with suppliers more effectively, handle unexpected issues, and ensure the supply chain remains resilient.
Continuous improvement
Embracing a culture of continuous improvement is not merely about managing the move at hand but about consistently seeking ways to refine your business quality management strategy. These periodic check-ins allow you to learn from past operations, adapt to evolving market conditions, and incorporate lessons learned into your processes. Continuous improvement ensures that your production quality management practices remain agile and resilient. It fosters a mindset of innovation, encouraging your team to explore new technologies, refine procedures, and optimize your operations.
Post-relocation evaluation
After completing your relocation, conduct a thorough post-relocation evaluation. This step allows you to assess the success of the move, particularly regarding the quality of your operations. It's an opportunity to reflect on what went well and what could have been improved. Identifying areas for enhancement paves the way for continuous growth in your quality management practices. So, celebrate your successes, acknowledge the challenges overcome, and use these insights to refine your approach for future relocations.
A true foundation for long-term business success
Effective supplier quality management during relocation is decisive for sustaining business continuity and meeting customer expectations. Implementing the best practices discussed here guarantees that businesses will minimize risks, maintain strong supplier relationships, and ensure a smooth move to a new location. So, these strategies mitigate potential disruptions and lay the foundation for long-term success during relocation.
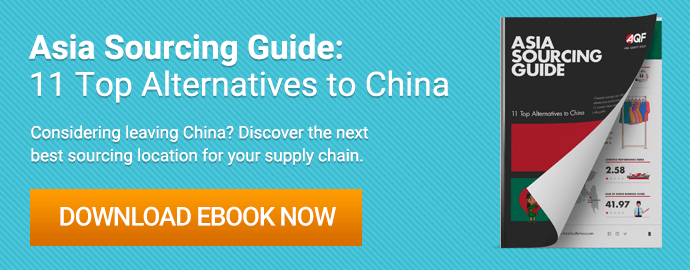