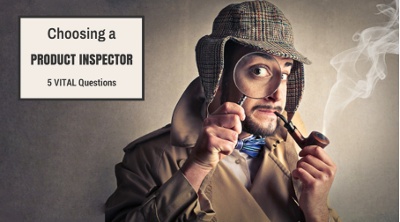
Your supplier in Dongguan, China is a mere two weeks away from shipping your order of 6,000 pairs of designer ladies’ shoes. And you haven’t had a chance to look at the goods to make sure you’re getting what you paid for!
Then you get an idea – hire a product inspector to visit the factory and check the goods on your behalf. You breathe a sigh of relief. Now the only question that remains is how do you go about choosing a product inspector?
If you’re scratching your head trying to think of a reputable product inspection company by name, you’re not alone. Lots of importers have trouble finding a QC provider that is reliable, knowledgeable, trustworthy and cost-effective. And if you are able to name one or a hand full of third-party inspectors, do you know how to weigh each to decide which is best for you?
Here I want to give you an in-depth look at the five MOST important questions you should be asking when choosing a product inspector.
1. What’s your man-day rate or cost for inspection?
Since you probably consider cost to be a major determinant in choosing a product inspector or third-party inspection company, why not start there? But bear in mind, cost is certainly not the only factor to consider. Plenty of inspection companies out there will offer cheaper rates for less thorough or honest inspections – remember that. You get what you pay for.
Inspection based on “man-days”
Most major third-party inspection companies bill based on what are called “man-days”. A man-day is the length of time a product inspector spends in a typical business day. A single man-day usually includes time needed for the inspector to:
- Travel to the service location, typically the factory that manufactures your goods
- Pull a random sample of goods from production (for inspections that use AQL sampling)
- Inspect your order of goods, or a sample of goods
- Tag any units that contain quality defects (some inspectors may also take photos or video of affected units)
- Fill out a written inspection report that shows their findings; and
- Travel home from the inspection site
Whether your product inspector bills by man-days or some other method, you’ll probably still be charged based on the time needed for these aspects of inspection (related: 5 Ways the Smartest Importers Cut Inspection Costs).
Travel expenses and inclusive man-day rates
It’s important to note that travel expenses will also be a major cost factor for choosing a product inspector.
Aside from a man-day rate, many third-party inspection companies will also charge a separate fee for travel expenses. These are costs related to any airline, train or bus tickets, hotel accommodation or other necessities for getting to and from the inspection location.
In some cases, an inspection company may be willing to offer you a reduced man-day rate that is inclusive of travel fees. This discounted rate is often reserved for importers that need a minimum volume of inspection man-days per month. It pays to learn more about what pricing options you have available when choosing a product inspector.
"An inspection company may be willing to offer you a reduced man-day rate that is inclusive of travel fees."2. How many product inspectors do you have and where?
This question is important to ask, especially when choosing a product inspector in China. China is the fourth largest country in the world with a land area of 9,596,960 sq.km.
Why the geography lesson?
Because travel costs for inspectors can add up fast in such a huge country.
The number of staff a third-party inspection company has and how spread out they are is important. An inspector may have to travel from their company office in Guangdong Province in the south to a factory in Tianjin in the north. That’s A LOT of travel time and associated expenses that you’ll be paying.
Local inspection staff and lower expenses
Of course, professional inspection companies do take measures to keep travel costs low when they can. The main way they lower costs is by hiring inspection staff that live closer to the service location.
In the example used above you need an inspection in Tianjin. Rather than sending an inspector from Guangdong Province, your QC provider probably maintains a number of inspectors in or near Tianjin that can travel to that location. This way, travel expenses can be greatly reduced, while still offering you the same level of QC oversight.
Ask about the number of staff and where they’re located when choosing a product inspector. You shouldn't pay someone in South Korea to fly all the way to Indonesia for a 1-man-day inspection.
3. Are your product inspectors full-time, part-time or contracted?
Just as important as asking where and how many inspectors a QC company has is finding out which are full-time, which are part-time and which are contractors. Ideally, your products would be consistently inspected by the a few different inspectors each time, all with experience inspecting your product type. But this isn’t always the case.
Part-time product inspectors
If your QC company doesn’t have inspectors in common factory areas like Dongguan or Ho Chi Mihn City, then they may be a small company using part-time inspectors. The issue with part-time inspectors is that their inspection method is less standardized. This can make for inconsistent results, and they may not always be available to inspect your products.
However, it’s important to note that an effective independent inspection company will rotate inspectors regularly. This ensures there are no integrity problems that could result if the same inspector visits the same factory day after day (more on this in a moment).
Contracted product inspectors
Contractors are arguably less reliable product inspectors than the other two types discussed here. This is due to their being hired periodically and irregularly. These product inspectors usually have a background in professional quality control but don’t consistently work for the same company.
Sometimes a third-party inspection company will hire a contractor to handle inspections in a low-volume area where hiring a part-time or full-time inspector isn’t warranted. This saves the inspection company money by not having to pay a salary to staff that are seldom needed.
A contracted product inspector may be sufficient if your product is simple or lower-cost. Insisting on the use of a full-time inspector could end up increasing your inspection cost if one is not locally available. Find out whether the inspectors checking your products will be full-time, part-time or contracted.
4. How fast can you book an inspection and when can I expect the report?
These are good questions to ask when choosing a product inspector. They can give you valuable insight into how efficient and flexible a QC company is. Generally, the longer it takes for booking and reporting, the less organized and efficient they are.
Lead time for booking product inspections
Generally, it shouldn’t take an experienced and efficient inspection company more than two business days of advance notice in order to guarantee a regular inspection. But there are exceptions when the booking process may take more time, such as:
- Inspections scheduled during the time leading up to and immediately following a national holiday and
- Inspections located outside a QC company’s main area
National holidays can lead to a sudden jump in the number of inspection requests from importers trying to work around the holiday. As a result, it can be difficult for a product inspector to guarantee the same availability afforded by normal conditions. A prime example of this is Chinese New Year (related: How Chinese New Year Affects Manufacturing).
Inspection located outside a QC company’s main area can take longer to arrange. If this is the case, your QC provider may be hiring a part-time or contracted inspector.
Lead time for sending product inspection reports
Lead time for sending reports might not seem like a major concern for you when choosing a product inspector. But consider being on a very tight schedule and needing your order of goods to ship within just 24-48 hours of inspection. In this case, you’ll probably want to know the results of inspection as soon as possible so you can make an informed shipping decision.
Some product inspectors need one or two days to complete the written report and send it to you. Others are able to send you the report within just a few hours of the inspection’s completion.
Whatever your level of urgency, sooner is usually better when it comes to receiving the inspection report. But it’s best to work with your supplier to arrange inspection plenty of time ahead of the scheduled shipping date. This will allow for any needed rework to the product without delaying shipping.
"Arrange product inspection plenty of time ahead of the scheduled shipping date to avoid delays."5. How do you prevent integrity issues during product inspection?
Preventing integrity issues is SUCH a major aspect of effective manufacturing. And it’s a shame that most importers don’t know to ask about it when choosing a product inspector. Integrity should be an important consideration, no matter which country you’re importing from.
Alternating product inspectors
You might think that by sending the same inspector to check your orders from a factory, you’ll have the most consistent and experienced oversight. But actually, sending the same person to inspect at the same factory everyday can put you at risk.
This is because the more time an inspector spends with the same factory staff, the closer they become. It’s not long before the inspector develops a bias towards the factory and, possibly, becomes more lenient or forgiving in their reporting of quality problems.
As a way to prevent this, it’s important that the people inspecting your product are rotated regularly. This is one way a QC company can prevent integrity issues. You might be concerned about the level of experience of different inspectors checking your product. But most professionals will assign inspectors that have sufficient experience in your product or product area.
"Sending the same person to inspect at the same factory everyday can put you at risk."Formal inspection procedures for reporting integrity breaches
Aside from rotating inspectors, you’ll want to know what kind of formal inspection procedures your QC provider has in place for reporting integrity problems.
- Does the inspector fill out a form to document any meals, transportation or similar benefits provided by the factory and have the form signed by a factory representative?
- What happens if an inspector is handed an actual bribe during inspection?
- Will the QC provider inform you of any such cases of bribery?
These are the specific kinds of things you should be looking for in a QC provider that takes integrity seriously. These are particularly important when inspecting in China or South East Asia.
Consider it a red flag if a QC provider can’t give you details about any specific procedures they have for preventing corruption or other issues with integrity.
Conclusion
Importing from abroad can be stressful. But choosing a product inspector doesn’t have to be. Now you have the tools to find which third-party inspection firm is best for you.
There are many out there. But the number that you can trust with the quality of your product, the satisfaction of your customers and, indeed, the lifeblood of your business is much smaller.
And if you'd prefer to listen to the author, Chao Wang, and Client Manager John Niggl discuss these points, check out the manufacturing podcast that covers this article!
Leave us a comment, and let us know what other questions you ask when choosing a product inspector!
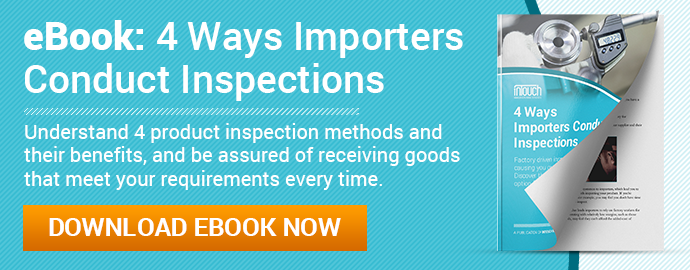