Today, manufacturers constantly seek ways to reduce costs while maintaining high-quality standards. Striking the right balance is essential since quality in manufacturing directly affects customer satisfaction, product reliability, and overall business reputation. Therefore, businesses must adopt innovative strategies that enhance efficiency and reduce expenses to remain profitable without sacrificing quality. This article explores how manufacturers can achieve this delicate balance by cutting costs smartly and sustainably.
Streamlining Production Processes for Maximum Efficiency
Reducing inefficiencies in the production process is one of the most effective ways to cut costs. Unnecessary steps, bottlenecks, and outdated practices can waste time and resources. Optimizing the production flow can, in truth, lead to significant cost savings.
Manufacturers should evaluate their workflows to identify areas for improvement. One solution is implementing Lean manufacturing principles, which focus on minimizing waste and maximizing efficiency. Automating repetitive tasks is another key step. Automation speeds up production and reduces the potential for human error, leading to fewer defects and higher overall quality. By making the processes easier, companies can produce more with less, ensuring cost reductions without compromising quality.
Optimizing production processes by eliminating inefficiencies and implementing automation can significantly reduce costs while maintaining high quality.
Investing in Technology to Improve Long-Term Savings
Many manufacturers hesitate to invest in new technology due to the upfront costs. However, this investment often results in long-term savings that far outweigh the initial expense. Advanced technologies such as artificial intelligence (AI), the Internet of Things (IoT), and modern machinery can significantly enhance production efficiency and quality control.
Technology-driven improvements, such as predictive maintenance, can help prevent equipment breakdowns and reduce downtime. That keeps the production line running smoothly and ensures products are consistently manufactured to high standards. Over time, technology reduces defect rates, leading to fewer product recalls and customer returns—both costly and damaging to a company’s reputation. Embracing modern technology is essential for companies that want to cut costs while maintaining quality.
Investing in advanced technology can lead to long-term savings by enhancing production efficiency, reducing downtime, and improving product quality
Reducing Waste Through Smart Material Management
Waste is a significant contributor to unnecessary manufacturing costs. Reducing it should be a priority for any company aiming to cut expenses without sacrificing quality in manufacturing. One effective approach is to implement just-in-time (JIT) inventory systems. That reduces excess stock and minimizes the risk of spoilage or obsolescence, ultimately lowering storage and material costs.
If storage space is a problem, consider portable storage solutions, which allow you to store inventory off-site when space is limited or seasonal demand fluctuates. Portable storage solution provider like PortaBox Storage, a secure and flexible portable storage unit provider, can deliver containers right to your location. You can load them at your convenience, and they will pick them up for safekeeping at their facility. That helps businesses reduce on-site clutter and better use their available workspace while ensuring easy access to materials whenever needed, keeping operations efficient and organized.
Manufacturers can also recycle waste or reuse scrap materials where feasible. Waste reduction ties directly to sustainability efforts, which can improve a company’s green reputation while cutting costs.
Reducing waste is essential for cutting costs and maintaining quality in manufacturing, with strategies like just-in-time inventory systems and recycling scrap materials proving effective
Supplier Collaboration to Lower Material Costs Without Sacrificing Quality
Another area where manufacturers can save money is by working closely with suppliers. Instead of focusing solely on getting the lowest price, manufacturers should build strong relationships with suppliers to balance cost and quality.
Negotiating bulk purchasing deals or long-term contracts leads to cost savings. In contrast, failing to manage supplier relationships properly can result in higher costs and inconsistent material quality, directly affecting the final product. When collaborating with suppliers, manufacturers can develop cost-effective solutions that do not compromise the materials' integrity. Regular communication and strategic partnerships ensure both parties benefit from reduced costs and consistent quality.
Training Employees for Increased Productivity and Quality Control
A well-trained workforce is essential to cutting costs and improving quality in manufacturing. Employee errors, inefficiencies, and lack of skills can lead to production delays, product defects, and increased costs. Investing in training can help solve these issues.
Cross-training employees to handle multiple tasks allows for greater flexibility on the production floor and reduces the need for additional hires. That saves costs and ensures that any gaps in staffing don’t disrupt production. With this in mind, trained employees are better equipped to spot potential issues before they become costly, improving quality control and efficiency. Continuous training programs ensure workers stay updated on the latest tools, technologies, and best practices, enabling manufacturers to maintain a high output standard at a lower cost.
Optimizing Energy Consumption to Lower Operational Costs
Energy expenses can be a significant portion of manufacturing costs. Reducing energy consumption is a straightforward way to save money while maintaining operational efficiency. Energy-efficient technologies like LED lighting and automated energy management systems help manufacturers lower their utility bills.
Scheduling production during off-peak hours can also help take advantage of lower energy rates. In short, cutting energy costs through efficiency measures directly impacts the bottom line. Regular equipment maintenance is another essential aspect of energy management, as poorly maintained machinery can consume more energy than necessary.
Outsourcing Non-Core Tasks to Specialized Partners
Outsourcing certain non-core functions, such as logistics, packaging, or IT services, is an effective way to reduce costs without impacting the quality of the final product. Manufacturers can focus on their core competencies by outsourcing to specialized partners while leaving non-essential tasks to external experts.
When managed correctly, outsourcing can improve efficiency and reduce costs. For instance, outsourcing logistics can simplify distribution, reducing the time and cost associated with shipping. Hence, manufacturers can focus on their strengths while ensuring that professionals handle secondary tasks. However, it’s important to regularly review contracts to ensure outsourcing remains cost-effective and aligns with the company's quality standards.
Continuous Improvement and Innovation for Sustained Quality and Cost Reduction
For manufacturers to remain competitive and keep costs low, they must embrace a culture of continuous improvement. Continuous improvement, often associated with the Kaizen approach, encourages employees at all levels to seek ways to enhance processes. This mindset leads to small, incremental changes that, over time, result in significant cost savings and improvements in quality.
Innovation is vital for cost reduction. By exploring new materials, processes, or designs, manufacturers can often discover more efficient ways to produce products by exploring new materials, processes, or designs. Another key point is to encourage employee feedback on improvements, as they often have valuable insights into day-to-day operations. In contrast, companies that fail to innovate risk becoming stagnant, which can lead to rising costs and a decline in product quality.
Cutting Costs Without Compromising Quality in Manufacturing
Cutting costs doesn’t have to come at the expense of quality in manufacturing. By focusing on simplifying processes, investing in technology, reducing waste, and optimizing energy use, manufacturers can lower expenses while maintaining high standards. Strong supplier relationships, employee training, and a commitment to continuous improvement ensure that cost reductions are sustainable and do not affect product quality. Adopting these strategies is essential for success and profitability.
Alongside the cost management road, don't set aside quality control. As a business owner, you should regularly assess the quality of your products to ensure they remain consistent during transitions. As a professional quality control solution provider, AQF is here to assist you. With over 17 years of experience in the quality control industry, we can support various product categories across multiple sectors. Our local experts can reach your manufacturing sites quickly and provide you with prompt feedback, enabling you to make rapid decisions in today's fast-paced market. Want to learn more? Contact AQF today!
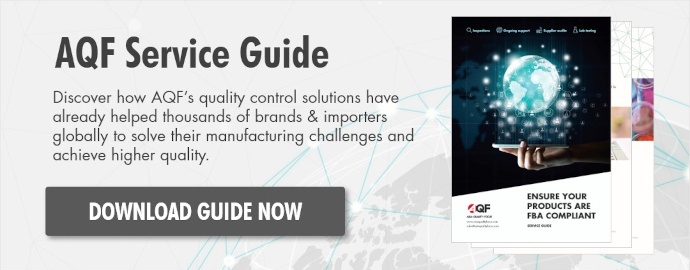