Behind its simple aspect, the AQL table is complex, especially when we need to define the AQL sampling size for product inspection. We all know the basics: identify the sampling size based on the total order quantity however do you know you can adjust AQL sampling plan for critical, major and minor defects?
The official AQL table
Before to start any explanation, it is important to get the right tool. When looking for the AQL sampling table online, it is very easy to find different versions. However, only one is the official and valid version: download or view the AQL tables ISO 2859, ANSI/ASQC Z1.4 used for product inspections.
Different AQL sampling size for critical, major and minor defects
The AQL standard has two tables: the sampling size code letters table and the single sampling plans for normal inspection table.
The table single sampling plans for normal inspection is the one of our interest today. It determines precisely the final AQL sampling size according to the tolerance level defined for each defect type (critical, major and minor).
Structure of the table single sampling plans for normal inspection:
- The 1st & 2nd columns, sample size code and sample size, identify the sampling size
- The 1st row, acceptable quality limits for single inspection, lists the levels of acceptable quality limits (tolerance levels) the buyer can choose from for each defect type.
At the cross-road there is the sampling size to apply according to the tolerance level chosen for each defect types.
A professional third party inspection company usually chooses three tolerance levels (one per defect type): critical 0, major 2.5, minor 4, thus there are three sampling sizes to determine.
Role of the arrows on the table single sampling plans for normal inspection
Those arrows are very important. In general they are the ones missing in the wrong AQL tables on internet, also the ones that create misunderstandings.
The arrows indicate if the sampling size varies according to the tolerance level allocated to each defect type (critical, major and minor).
Let's take two examples
The sampling size changes for one or more defect types
For an order of 160K pieces the general AQL sampling size is 800pcs however when following the three tolerance levels of profesional third party inspection companies: critical 0, major 2.5, minor 4, the sampling size per defects varies:
- Critical defects sampling size: 800pcs
- Major defects sampling size: 500pcs
- Minor defects sampling size: 315pcs
The sampling size is the same for all defect types
If, for the same total order quantity of 160Kpcs, the buyer chooses its own tolerance levels for each defect type such as critical 0, major 1 and minor 1.5, the sampling size is the same for all defect types:
- Critical defects sampling size: 800pcs
- Major defects sampling size: 800pcs
- Minor defects sampling size: 800pcs
And you: is it all clear for you? Feel free to share your doubts regarding how to determine the AQL sampling size for critical, major and minor defects!
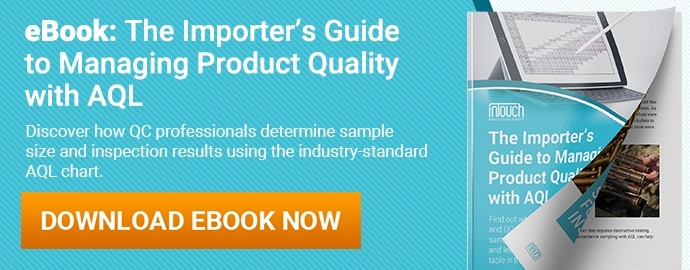