Best in Manufacturing – October 16, 2016
Each Sunday, we publish a list of top articles and other content related to manufacturing in areas like quality control, product development, supply chain management, sourcing, auditing and law.
1. Electric silk paving the way for wearable electronics
For millennia, silk has been a beautiful, luxurious and widely-sought fabric. Despite the lengthy process to create it, silk’s allure is so great that it greatly contributed to the ancient Silk Road between the East and West. Nowadays, silk is mass-produced and easier to acquire.
But one development, thanks to researchers at Tsinghua University in Beijing, stands to make the legendary fabric even more versatile and useful.
The researchers recently conducted an experiment where they fed carbon nanotubes and graphene to silkworms. They accomplished this by spraying mulberry leaves (the preferred food of silkworms) with aqueous solutions. The weights of the solutions were composed of 0.2 percent of the aforementioned materials.
The results are nothing short of amazing. The silkworms produced silk that’s able to conduct electricity and “can withstand at least 50% higher stress before breaking”.
As the market for wearable electronics grows to $1.2 billion by 2025 (go to #3), it’s likely that this new type of silk will eventually make an appearance in laboratories, design studios and shops. It could be used in smart textiles and advanced body sensors, among other things. And for importers and manufacturers, this all means an opportunity to stay on the cutting edge of technology and develop new, advanced business segments.
If you’d like to learn more about this super-silk developed by Tsinghua University, check out the full article in the link below:
Silkworms Spin Super-Silk after Eating Carbon Nanotubes and Graphene – Scientific American, Prachi Patel
2. Digitized manufacturing: is the ROI there?
Risk is a critical consideration of any investment. And when compelling evidence doesn’t exist for the usefulness of investing in a certain project or idea, making the leap to supporting it becomes even harder.
That’s why for some, pouring money into the digitization of manufacturing is hard to do. It hasn’t been adopted on a wide enough scale yet to convince some skeptics of its return on investment (ROI). But many in the industrial sector realize it has enormous potential to transform every aspect of manufacturing, from research and development to production and more.
The author uses Boeing as an example to prove the benefits of digitization. He mentions that Boeing used all virtual design for the 777 and 787, which reduced time to market by over 50 percent. And this isn’t even the tip of the iceberg.
According to research by the World Economic Forum,
…the combined value — to society and industry — of digital transformation across industries is upwards of $100 trillion over the next 10 years.
Does that sound like something worth investing in? I’d definitely say so. And those that are first movers for implementing digitization will see a greater amount of this value reflected in their own business as they begin to occupy established, highly competitive positions.
If you’d like to read more about making the financial leap toward disruptive manufacturing technologies, check out the full article in the link below:
Can the CFO Predict ROI of Digitalization in Manufacturing? – Mark Humphlett, IndustryWeek
3. Less expensive metal 3D printing
3D printing has long been considered just a prototyping tool. While it’s true that the technology can quickly bring concepts to life, it's been harder for the manufacturing industry to adopt 3D
printing en masse for production needs. But due to the partnership of companies Optomec and Fryer Machine Systems, metal 3D manufacturing took a step in the direction of more widespread adoption.
The combination of Optomec’s laser engineered net shaping (LENS) process and Fryer’s computer numerical controlled (CNC) machines could result in systems that are created at a lower cost. But talking about these technologies isn’t nearly as exciting as seeing them in action.
You can take a look at the LENS 3D printing system in the video below:
Advances like these are great news for manufacturers because they could eventually result in more effective prototyping, more precise production processes and innovative new products that can only be made with 3D printers. Maybe in the future, thanks to this partnership, you’ll find some 3D printed metal products in your orders or on your shelves.
If you’d like to learn more about Optomec and how the LENS process works, check out the full article in the link below:
Optomec Introduces Hybrid Metal 3D Printing at Half the Cost – Editorial staff, Engineering.com
4. Realizing the potential of the industrial Internet of Things
Smart production lines, collecting data about operations in real-time and discovering new business insights are just a few of the benefits of the industrial Internet of Things (IIoT). But these advantages won’t become a reality without a proper strategy in place.
As the author points out, operational technology (OT) and business technology (IT) need to combine to truly reap the benefits of the IIoT. Historically, however, these two areas of a business have acted separately from one another. Making them successfully interact to promote data synergy requires businesses to align their priorities.
In addition to this advice, the author provides some best practices to help OT and IT work together. They are:
- Understand your uptime needs
Consider: Are you aware of the availability required by your operations? Do you know the actual costs of unplanned downtime?
- Protect your “inflight” data
Consider: Will you still receive all your valuable IIoT data in the event of a transmission interruption? Are you sure that your data will be consistently delivered?
- Keep it simple
- Keep your options open
The IIoT is a promising development in the manufacturing sector. But for some that try to introduce it to their operations, it could be a useless investment if it’s not implemented effectively. By heeding the advice of the author, however, you can gear your business, suppliers or facilities up for IIoT success.
If you’d like to read about the other best practices mentioned above and how to successfully realize the potential of IIoT, check out the full article in the link below:
Merging OT and IT Systems to Achieve the Promise of IIoT – John Fryer, Manufacturing.net
5. Additive manufacturing strengthening nuclear security
3D printing offers the benefit of easily creating tools and other items that might otherwise require significant investments of time and money. And while the technology is normally thought of as one that’s used for prototyping, it has uses elsewhere – like in the nuclear industry.
At the Pantex Plant in Texas, men and women handle nuclear materials, create bomb casings and assemble high explosive detonators. Especially in this line of work, there’s little room for accidents; precision is essential. And due to the accuracy in production that’s required, constant munitions testing is needed to ensure everything is up to par.
Before 3D printing, employees had to spend great lengths of time to create a costly holding fixture used for testing explosives. Thankfully, however, 3D printing changed that.
The Additive Manufacturing team found a solution by creating a new, one-piece holding fixture through additive manufacturing. The updated fixture is reusable and eliminates the need for pads and glue, thus saving the department more than $300,000 and thousands of work hours every year.
As additive manufacturing continues to evolve, it might further integrate into the operations at Pantex and into other areas of the defense industry. And if the defense industry continues to use this technology, it’ll hopefully develop innovations with commercial applications that can be shared with the rest of society.
If you’d like to learn more about Pantex and 3D printing, check out the full article in the link below:
Improving Nuclear Security with Additive Manufacturing – Tek Ferguson, Machine Design
We’re constantly scanning the web for top manufacturing stories and news. But if you’d like to submit an article for consideration for our weekly Best in Manufacturing, send us a message and let us know.
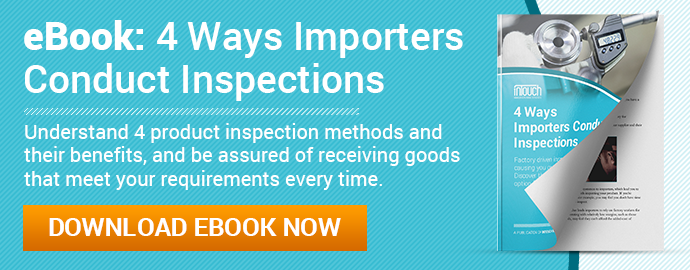