Understanding the manufacturing process of tissues is key in laying out a quality control program for such items.
Several types of equipment are used to press the non woven wet mixture, and to create non woven sheets. Non-woven fabrics are assembled by chemically, mechanically and thermally weaving fibers together. There's two assembly processes for non-woven fabrics, a wet and dry laid process. A wet laid is used generally in the production of tissue.
Mixing Process of the Raw Materials
The wet mixture flows into a head box device, which will then spray the mixture onto a fourdrinier. The fourdrinier is 50 feet in length or more and is flat like a table. The wet mixture travels down the fourdriner and separates. The water type liquid drains below the mesh and the fibers stay above the mesh. Once the fibers and water have separated, felts (series of woolen blankets) compress the tissue further to squeeze any remaining water from the fibers.
Drying Process of the Facial Tissue
The facial tissue is then passed through a Yankee Dryer, which is a 10 – 12 foot steam roller. The facial tissue is passed through the Yankee dryer until the tissue is dried. If a design is desired it is imprinted into the tissue during the process of water removal.
Lotion Application Process
After the water removal and drying stage, the facial tissue is referred to as a webbing. The webbing is ready for further processing and stored on calender sticks, which are large vertical rollers. The lotion for the tissue is prepared in a separate heated tank with a blender type system for mixing and is sprayed a thin layer over the webbing being fed by a paper making belt. The tissue is then passed through several rollers to remove access lotion that may be left in the tissue. During this lotion application analytical testing and evaluations are performed by a quality control specialist. The amount of lotion coated on tissue is extremely important and undergoes several tests.
Forming and Packaging Process
The webbing then passes through rotating blades that cut the facial tissue into desired length. The facial tissue is then cut into intervals and then packaged into cardboard boxes or plastic wrapping. Before being shipped off to selected consumers, fabric softness must be tested by a quality control specialist and trained volunteers to test the softness and flexibility. Density and absorbency facial tissue inspection tests and Colormetric analysis are also performed.
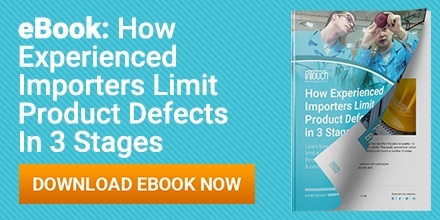