A factory’s overall layout and the setup of its processes have a strong impact on efficiency. It should be carefully planned. However, most Chinese suppliers suffer from serious mistakes that were made at the time their factories were set up.
Here is a list of 5 common examples we see over and over.
1. Illogical material flow throughout the plant
Ideally, the flow of materials should be product-oriented.
Let’s take a simplified example:
Overlock stitching → Double-needle stitching → Trimming → Packing
In this case, the workstations should be lined up in that order:
Overlock machine → Double-needle machine → Table for trimming → Table for packing
(And, ideally, trimming and packing should be next to each other on the same table.)
Instead, manufacturers usually organize their equipment by groups or centers – for example, a CNC machining center, a welding center, a polishing center, assembly lines, etc. And there is often a logic for that:
- Each group can be made to form one workshop, with one dedicated supervisor/leader, and build process expertise within that workshop.
- The process itself might have special requirements: heavy equipment is best left on the ground floor, silkscreen printing emits toxic fumes, and so on.
However, in many cases, we see no logic at all! The activity grows and new machines are purchased… and they are placed wherever there is free space!
What happens when parts have to queue for a lift, need to go to another building for further processing, and then get stored in a finished goods warehouse that is 200 meters away from the loading dock?
Transportation waste, and lower factory efficiency. They are paying people to walk around and carry material... In itself, this activity is not something any customer is happy to pay for.
2. Poor layout of manufacturing lines/cells
Another type of waste is motion waste. Operators have to walk too much. It means they don’t spend much of their time actually transforming the product.
Here is an example of spaghetti diagram from the ASQ website. Draw this type of diagram next time you visit a manufacturing facility and you might discover a situation that is much worse!
Note that, in addition to low labor productivity, excessive motion and material transportation are detrimental to quality. Operators are not fully focused on their task, take their eyes off the work, and make mistakes. Parts are piled up and scratched or dented. Nothing good comes out of a convoluted process.
3. Automation that doesn’t work as expected
Most manufacturing managers dream of automating their processes. This is more and more the case in China. However, we often see highly-automated equipment down that is being repaired (or waiting for a specialized repair person).
Why is this? Poor preventive & predictive maintenance skills. The technicians and engineers have to gradually learn how to work with automation. If they are still in their “once it’s broken we repair it” mode, more automated equipment will be down more often, for the simple reason that it counts more single points of potential failure.
Again, this has an impact on factory efficiency and also quality. Before a high-speed machine breaks down, it might make 2,000 bad parts. If that issue were caught immediately, the machine could be stopped and the issue investigated. Letting the machine run until failure is disastrous.
4. Poor organization of internal logistics
The way internal logistics are set up has a sizeable impact on overall productivity. Here are three issues you can watch out for.
- Are all materials delivered to a central warehouse, and then later dispatched to different workshops, rather than being delivered directly to point-of-use storage locations inside the workshops?
- Do operators need to walk to replenish a container of parts in a regular manner? Do they spend time searching and asking people? Do they hide and smoke a quick cigarette at the same time?
- Do warehouse operators often need to search for materials because of an inaccurate database?
5. Excessive office space for production
Do you want production supervisors and process engineers to sit down in individual offices and send emails, to look good in management’s eyes?
Of course not. Their primary work is on the shop floor. Many of the best factories don’t even give a nominative address to those employees. All the key information should be made visible and then acted on immediately, at the point where value is created.
Conclusion
As this last example demonstrates, even the office layout has a direct impact on efficiency. Nothing should be left to chance. Systems and processes can enable high performance (low costs, high quality, and short lead times)… or they can make it impossible.
In the end, all this belongs to the factory’s general manager. Unfortunately, in China and most South-East Asian countries, those people like to blame their employees for low performance rather than looking in the mirror.
What other examples of poor factory layout have you come across? Share in the comments section below!
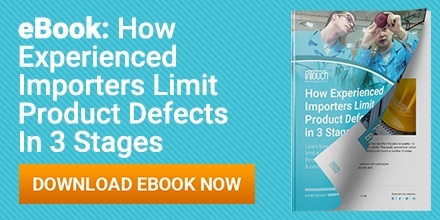