Quality control services are crucial to any manufacturing process, and it is even more important now as the world deals with the COVID-19 pandemic. Some companies may think canceling supplier audits or product inspections may be the proper thing to do in current conditions, but that is not the case.
Doing a factory audit is just as important now than it ever is, if not even more important, because consumers are increasingly focused on the quality of the products that they buy for themselves and their family. Here is why you should still prioritize your quality control initiatives during the pandemic.
In-House Quality Control Services vs. Third Parties
During a global pandemic, the importance of having a flexible, scalable team is more important than ever. This fact also highlights the necessity of working with third parties to manage quality control.
The benefits of working with a third party QC team are twofold:
- You can easily and affordably allocate resources based on business volume
- You won’t have an idle team standing by during periods of low volume
This is leading companies to adjust to a new way of performing quality control audits. As production surges and then slows, the benefits of having a fixed-cost, in-house team become less apparent and more businesses are now relying on flexible third-party relationships.
Why Canceling Audits is a Bad Idea
Canceling quality audits limits a firm's insight into its supply and manufacturing chain, so inferior materials and supplies may sneak into your manufacturing, resulting in making products that aren't up to the quality consumers expect -- which could hurt your company's credibility in your industry, potentially cutting into your sales and revenues.
That is especially true as factories reopen from COVID-19 closures, and try to quickly ramp up production to make up for lost production time. If you are creating more product than usual, performing regular audits is even more important than in other times. Canceling audits also lessens your ability to track your suppliers and make sure they are living up to any contracts you have with them, as well as abiding by your code of conduct expectations.
New Challenges for Ecommerce
The ecommerce space, with its rigorous quality control needs, has experienced unique challenges of its own.
With brick and mortar retail, customers are able to select the exact product they wish to purchase, so if an item is defective, they can simply choose another one off the same shelf.
However, ecommerce does not provide that luxury and the hassle of making returns and waiting for a refund is off putting enough. Therefore, ecommerce brands need to have exceptional quality control to preserve their reputations. Customers who receive defective products are likely to either choose a different brand next time, leave a negative review, or both.
With more and more retail companies relying on ecommerce channels to drive sales, the need for heightened quality control has reached a peak.
Contact Asia Quality Focus Today!
Asia Quality Focus can help you adapt to new challenges in quality control. Contact us today to schedule a demo to see how we can assist.
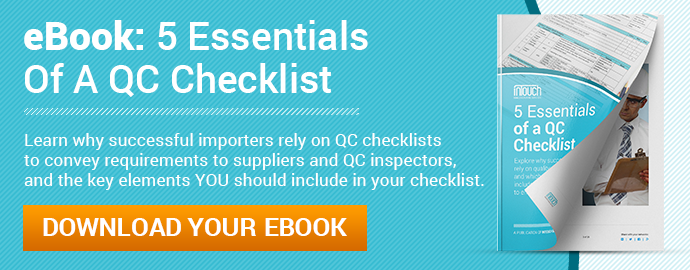