ctIf you’re planning on having your next order of made-in-China goods inspected by a 3rd party QC company – and we strongly recommend that you do – you’ll want to make sure you’re getting the most out of the inspection. The key to guaranteeing that your inspections are as effective as possible is to make sure that all parties involved – you, your supplier, and your QC team – understand your quality requirements.
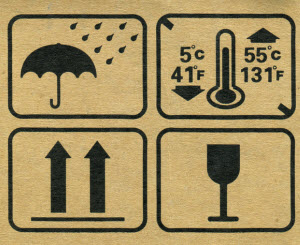
In order to leverage your quality control inspections to their fullest potential, preparation is crucial. There are a few steps you can take prior to the inspection that will ensure you receive the most actionable information in the QC report you receive afterwards. Remember, the idea is to ensure complete understanding of the quality level you require in your final products.
Here is a breakdown of the 5 steps InTouch recommends that every importer take leading up to their next inspection:
Provide Drawings, Specifications, Artwork to Your Supplier and QC Team
Chances are you provided this information to your factory well before your order entered mass production. However, if any modifications to the original product specifications have been made either before or during production, update your supplier with the most recent versions. Take it a step further and send your QC team the previous AND most recent versions of the product specifications, noting the key differences that you are expecting to be reflected in the final products.
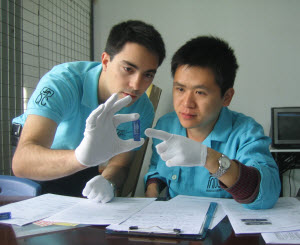
This will serve to confirm with you supplier what the end products should actually look and function like. For your QC team, this information will give them valuable insight during the inspection as to what issues they are finding are actual defects, and which issues indicate that the factory is using outdated product specifications.
Provide Approved Samples to Your Supplier and QC Team
Approved or “golden” samples are crucial to any quality control program. InTouch recommends keeping a set of 3: 1 for you to keep and compare to production units, 1 for your factory to use as a reference during production, and 1 for your QC team to reference during the inspections.

Like with product specifications, golden samples will allow your factory and QC team to see exactly what your product is supposed to look like, and what it is supposed to do. But golden samples are arguably an even better tool to accomplish this, because they can be held, felt, and manipulated just as an end consumer would. Where specifications come up short, a quick comparison to your golden sample will yield a definite answer as to whether or not your products are up to standard.
[sidebar name="case studies"]
Review Samples From Your Supplier
Again, its very likely that you reviewed samples from your supplier before placing an order. Even if the samples weren’t of your exact products, you were probably able to gain significant insight into your supplier’s ability to meet your quality standards.
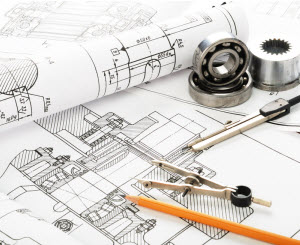
This is the kind of insight you should share with your QC Team. Provide them with images, or better yet the actual sample, and note what kinds of issues you found with the factory’s sample. If you’ve had conversations with the factory about what issues need to be addressed in order to meet your quality standards, inform your QC team. During the inspection, they can then follow up specifically on these issues.
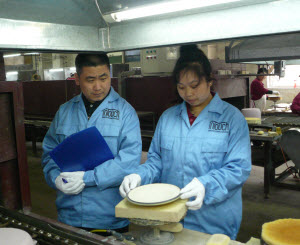
Provide list of Known Quality Issues to your Supplier and QC Team
If you’ve ordered the products you’re having inspected before and have identified quality issues in previous shipments, we definitely recommend sharing this information with your supplier and QC team. This can be done simply by organizing a list of the defects, with each ideally accompanied by an image. If you’d like to take this a step further, you can classify each defect as Major (will cause a return), Minor (unlikely to cause a return, but still an issue), or Critical (potentially dangerous to the end user).
As above, providing this list of known quality issues to your QC team and supplier will solidify their understanding of the level of quality you are expecting in your shipment. This can also help to streamline the inspection. For example, if you only consider scratches of 5mm or larger to be a defect, your QC team will not waste time marking and recording instances of smaller scratches. Your QC team can also add to this list and give you a historical record of the kinds of quality issues you’ve experienced in your orders, perhaps across different suppliers of the same product.
Develop a Quality Control Checklist
Together with golden samples, QC Checklists are an incredible asset for any quality-focused organization. QC Checklists serve as a central document that clearly lists your quality standards, a repeatable procedure to follow during each inspection, and a guide for how each defect found should be classified. Checklists are most effective when they are bilingual, ensuring that all parties involved can fully understand the quality standards. Truly comprehensive checklists will also incorporate other elements discussed earlier in this article, such as a list of known quality issues. For more information about quality control checklists, read our How To Guide for Creating a QC Checklist that covers this topic in detail.
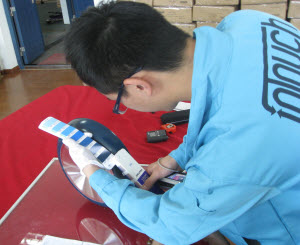
It’s important to note you should definitely include your supplier in the process of developing a QC checklist. If your supplier is unable or unwilling to agree to the standards you require, then documenting them in the checklist that will be used to evaluate their products will not yield the most effective results. In the same vein, try to make your checklist realistically reflect the actual criteria you will use to make accept/reject decisions for each shipment: if an inspection is conducted according to your checklist and the result is PASS, rejecting the shipment can cause serious consternation for your supplier.