Many importers lack a dedicated team in Asia for quality control and regulatory compliance. They already have their hands full managing multiple suppliers, placing POs, keeping production on schedule and approving shipments.
Importing goods from Asia exposes your supply chain to many risks, like potential quality defects, compliance issues and production delays. And these risks can be deadly to your importing business if they cost you customers, recalled products or penalties for noncompliance.
Quality control inspections and lab testing are essential to ensure goods meet your customers’ quality requirements and mandatory legal requirements. But how can you ensure product compliance without your own dedicated quality engineers on the ground?
Verifying compliance with inspections and lab testing
As a promotional goods startup, SquareNuts knew there were mandatory standards they must comply with to legally import into the EU.
But they didn’t have their own physical presence at their suppliers’ facilities in China or the required technical expertise to ensure product compliance. And they didn’t want to rely on their suppliers’ test reports alone, which they feared could be unreliable.
In this case study, you’ll learn why SquareNuts began working with AQF in 2013, including:
- Key qualifications they sought in a third-party QC provider
- How pre-shipment inspections have helped them anticipate quality issues
- How lab testing has helped them meet EU toy safety compliance requirements
- How AQF’s technical expertise helps them make lab testing decisions
These factors and more help SquareNuts cost-effectively manage product quality and limit their risk when importing from Asia.
Can a third party help you minimize risk in your supply chain?
Sometimes not having your own staff in Asia forces you to work with many different third parties to move manufacturing projects forward. And in turn, this subjects your supply chain to greater uncertainty and risk, as you have to oversee multiple partnerships.
A quality control provider with diverse service offerings can serve as an extension of your business near your suppliers. Working with one provider for all your QC needs lets you:
- Book inspections, audits and lab tests all within the same online platform
- Communicate with the same points of contact for every service
- Ensure consistent ethical policies within the same organization
- Centralize product requirements and quality control documentation in one location
Your third-party QC company doesn’t have to just be a service provider. The right one can be a true partner that simplifies your supply chain.
Tired of struggling to achieve quality goods without your own QC team? Aren’t sure how to ensure product compliance with mandatory legal requirements? If so, you won’t want to miss the lessons in this case study.
Strengthen your QC presence in Asia today. Click the button below to download your free case study now!
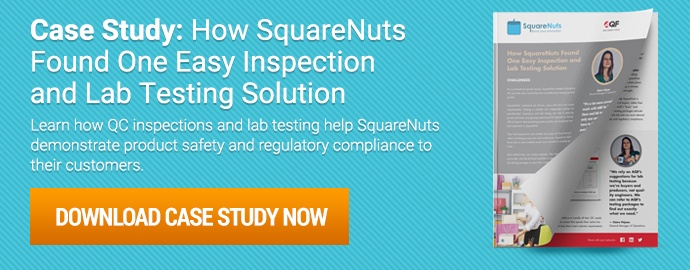