To complete a puzzle, you need all the pieces. Similarly, there are several key pieces of information your product inspection company will need to effectively check the quality and status of your order before it ships.
Product inspection, whether by your own full-time staff or by a trusted third-party, is a fairly standard precaution in the manufacturing industry today. Most experienced importers know that it’s very difficult to be sure about the quality of the goods you’ll receive without inspecting them before they leave the factory.
But what many importers don’t know is what information to provide their inspector that will help them do the best job possible. And giving your product inspector the wrong information can cause problems, such as:
- Delaying the inspection
- Under/overestimating the cost of inspection
- Attempting inspection at the wrong location
- Applying the wrong criteria during inspection
- Inspecting the wrong number pieces
These are just a few of the serious issues you can avoid by being familiar with this list of common information to provide your product inspection company:
1. PO and order details
A PO, or a purchase order, is a document typically containing information like order quantities per stock keeping unit (SKU), item numbers, ex-factory date, pricing and more. A product inspection company will need the quantity information shown on the PO for quoting the cost of inspection. It’s also acceptable to provide a packing list or some other breakdown of product quantities, instead of the PO, which some importers will do to hide pricing.
The number of SKUs and quantities for each are important for determining the number of pieces to pull during sampling. Typically, a sample should be taken of each SKU in an order. A larger quantity usually means a larger sample will need to be inspected for meaningful reporting. And it’s important to note what distinguishes each SKU because you may be able to save money by merging similar ones for inspection (related: 5 Ways the Smartest Importers Cut Inspection Costs).
Urgent orders
It’s also important to let your inspector know how soon you’ll need the order to ship. Informing product inspection staff of the shipping date helps by:
- Allowing adequate lead time for booking the inspection and
- Alerting inspectors to the possibility or rushed production or packaging
Product inspection companies often try to plan ahead, scheduling services two or more business days in advance to ensure they have staff available in that area to perform the service. You can ensure your inspection doesn’t delay shipping by notifying the inspector of the urgency of the order. And inspectors will be more vigilant in looking for common defects related to rushed production if you let them know ahead of time.
Packaging method and materials
Importers of some types of products often have very specific requirements for packaging. Packaging is especially important for higher-end, luxury goods, such as timepieces, jewelry and cosmetics.
You should provide your product inspection company with any specifications or requirements related to packaging to ensure they’re familiar with what to check. This is even more important when a factory is rushing to meet a shipping deadline. Since packaging is the last step before shipping, you’re more likely to see rushing affect quality at this stage (related: 5 Packaging Tests Vital for Product Inspection).
2. Any known quality defects or product issues
Even novice importers are typically familiar with certain quality defects and other issues known to affect their product. And some importers will try to “test” their inspector by seeing if they find such issues without being told about them beforehand. But this is ill-advised, even if you have time and money to spend trying out multiple QC providers.
Instead, it’s generally a good idea to inform the people that will inspect your product of these known issues early. It also helps if you can indicate your relative tolerance for each defect type. For example, if you’re manufacturing denim jeans in Vietnam, you might think that untrimmed threads are a minor issue you’re expecting to see. But you might be aware of issues related to zipper function and color shading between pieces. Informing your inspector helps you because:
- The inspector will know some specific issues to look out for
- The inspector will know how to classify different issues, which is important in determining if the product “passes” or “fails” inspection; and
- The inspector will know which on-site tests are more important to conduct than others
Simply put, you’ll receive a more accurate report of a more efficient inspection. Without this information, your inspector might conduct function testing for zippers on an inadequate sample of jeans. Your inspector might also classify some issues as “major” that should be “minor” and vice versa.
Every importer has unique preferences for how to evaluate their product. So your input on known defects and other issues essential to having your product inspected by your standard. Consider working with your inspector to develop a detailed QC checklist for your product as well.
3. Contact information
Aside from the detailed address of the factory—which your inspector will need—it’s always helpful to provide urgent contact details for both you and your supplier. This is because your inspection company may need to reach you or your supplier more urgently than email will allow. And if there are issues that need to be discussed before, during or after inspection, communication by phone is often the best option.
It’s helpful if you can provide your inspection with the office and mobile number of you and your supplier and note when it’s appropriate to use which. There are also various communication apps for mobile phone or PC that you can download for free, such as:
- Skype
- Viber (mostly popular in Europe)
- WeChat (used mainly in Mainland China and Hong Kong)
- WhatsApp (more popular in the United States and Europe)
- Line (popular throughout Japan, Taiwan, Thailand and Indonesia)
Depending on where you and your supplier are based, it may be worthwhile to use one of these apps to communicate more urgent matters. You never know when your inspector or supplier will need to contact you quickly to clarify a requirement, explain a problem or address another matter.
4. Feedback on reporting and inspection method
Many importers make the mistake of receiving an inspection report, looking at the overall result and then setting it aside. If the result isn’t “pass” they’ll often delve deeper to find out why. But few importers will take the time to read through, or at least briefly scan, the full report.
By looking closely at the full report, you might find issues you hadn’t previously considered. Maybe the product doesn’t meet a requirement that you didn’t specify before inspection, for example. Since the inspector wouldn’t have known about the requirement, the issue wouldn’t have affected the overall result. So you’d only spot the problem by looking closely at the actual findings of the report. Then you could adjust the criteria so that the inspector looks for it in the future.
Similarly, if you find the inspector is too strict in reporting certain issues, you can ask them to be more lenient in reporting these in the future. Changing the process for inspection to better suit you needs helps you get a more accurate report. It can even lower your inspection costs by eliminating needless checks or tests.
Your product inspection company should hold your product to the same standard that you would if you were inspecting the goods yourself. And you’re far more likely to be satisfied with the report if you’ve given your inspector and supplier clear product expectations and inspection criteria (related: 4 Steps to Success with Third-Party Inspection). Giving feedback on the reporting and inspection method is equally important.
Conclusion
Products that don’t meet your quality standard or requirements can leave your customers dissatisfied and your brand’s reputation damaged. But product inspections can help you be more confident that your products meet your expectations. If you decide to use third-party inspection, you’ll want your inspection company to have all the information they need to conduct an efficient and effective check of your goods.
Ultimately, there’s a critical piece to the quality puzzle, and that’s you. With your input on defects, order details and other important information, you’re in a much better position to have product inspection working for you.
And don't forget to check out the manufacturing podcast episode that covers this topic!
What else do you find is helpful to provide a product inspection company? Share your thoughts in the comments below!
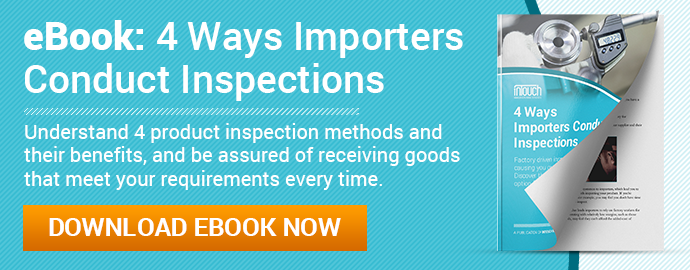