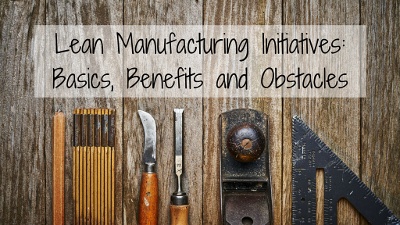
But let’s say you’re a carpenter that makes artisan furniture for high-end retailers. Would you rather have an organized workbench, where everything has its proper place and your tools are easy to find? Or would you rather have a messy one where you’re constantly losing materials and tools?
Most of us would choose the organized workbench because it’s easier to find the tools you are looking for in an organized environment. You become much more efficient in your day-to-day activities with each step you take to become more organized. You may not realize it, but this is the essence of “lean” thinking.
We've discussed the 5S method of improving efficiency. Now let’s talk about lean manufacturing as a broader term.
What is lean manufacturing?
Lean philosophy originated from the Toyota Production System (TPS). Lean manufacturing is a systematic method for the elimination of waste within a manufacturing system.
"At the end of the day, quality defects and their severity should be determined by the buyer."When most people hear the words “manufacturing waste”, the first thing that comes to mind tends to be wasted materials used in production of goods. But actually, there are many other types of manufacturing waste. And the average factory, especially in developing countries, has a LOT of waste.
Lean manufacturing initiatives focus on the reduction of the following seven wastes to improve overall quality and reduce costs:
- Transportation – moving products not actually required to perform the processing
- Inventory – all components and materials not currently being processed
- Motion – people or equipment moving more than what’s required for processing
- Waiting – waiting for next step in production
- Over-processing – redundant work effort resulting from poor tool quality or design
- Over-production – production ahead of or exceeding current demand
- Product defects – effort involved in inspecting for and fixing defects
What is the benefit of lean manufacturing initiatives?
The basic tenant of lean manufacturing is that a factory becomes leaner when waste is reduced. A lean factory is an efficient factory. And an efficient factory will have higher production capability and make products with a lower defect rate.
"An efficient factory will have a higher production capability and make products with a lower defect rate."An article published in 2018 listed the top 10 lean manufacturers in the world, placing Intel at number 4. “Five years ago, it took us 14 weeks to introduce a new chip to our factory; now it takes 10 days. We were the first Intel factory to achieve these times using Lean principles,” said one factory manager at an Intel plant in Ireland.
How does lean manufacturing work?
Let’s look at an example in transportation. The state-of-the-art running shoe you’re manufacturing in Dongguan, China requires 10 processes to complete. Between each process – polymer injection of the outer sole, assembly, vulcanization testing and others – your product requires transportation from one station to the next.
The chance of that product getting damaged by a handling error will be much higher than a product that is transported via conveyor belt (with almost no human handling in between). The conveyor belt also means the worker that would otherwise be needed to transport the product can instead be utilized at another production stage.
More products can be made during the same amount of time, since less time is required to manufacture each unit of finished product. This was made famous by Henry Ford with his use of the assembly line.
Why lean manufacturing initiatives often fall short
Many companies, both in the manufacturing and service sector, appear to be falling short in achieving long-term results with lean initiatives, despite the opportunities for improvement.
A 2007 article by Industry Week discussed the results of a survey of 3,082 company executives in 6 countries. The top reasons cited for failing to achieve long-term improvement were resistance to change and a lack of leadership, at 40 percent and 25 percent, respectively.
Resistance to change often occurs when workers and managers become accustomed to a certain way of doing things. Changes that seem to be counter-intuitive, in particular, are often difficult to force upon employees.
In cases like these, leaders might be faced with attempting a paradigm shift, a change in a seemingly immovable pattern of behavior in employees. It’s especially important that leaders work to instill a vision and inspire employees to adopt lean initiatives.
Conclusion
All of your suppliers are probably aware of lean manufacturing but most in developing countries implement few, if any, lean initiatives within their operations. This is one reason why third-party inspection is so important if you are manufacturing. Don’t ever take a new supplier’s word on their “amazing product quality” (see Third-Party Inspection vs. Factory Self-Inspection).
Lean manufacturing initiatives can be quite difficult to follow through on. Take the advice of Steve Denning, the author of a Forbes article on why lean programs fail: “The management task is not to impart a routine for doing work, but rather to inspire new work habits and mindsets for continually improving the work.”
Be sure to check out the manufacturing podcast episode that covers this article!
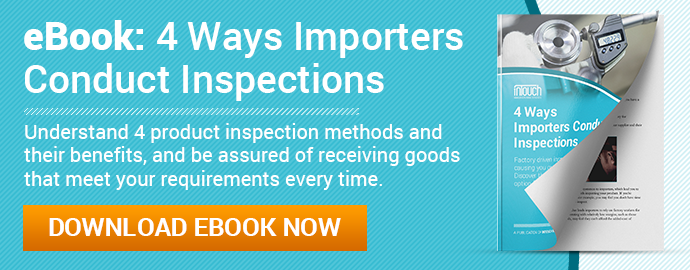