With the continued global spread of COVID-19 affecting importers and manufacturers alike, the erratic closure and reopening of factories will increase supply chain pressure. In such times it can be easy to overlook quality and compliance processes in order to meet deadlines.
This article aims to highlight some of the key risks and potential solutions to ensure the reliable flow of goods once lockdowns are lifted while maintaining a level of quality and compliance.
Common scenarios that put quality and compliance at risk
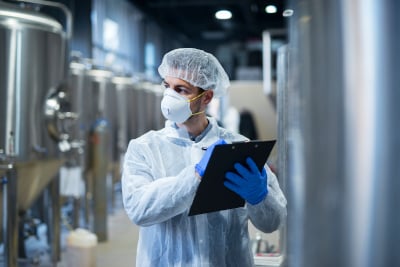
Government lockdowns have, for the most part, been reactionary measures imposed once a local spread of COVID-19 has been established. Such actions, by their very nature, are swift and do not provide supply chain stakeholders much time to plan. Goods that have been produced and not yet shipped are sometimes left in factory warehouses, while goods in production may be left mid-process once the workforce downs its tools.
The prolonged storage of goods, particularly in humid South East Asia, risks the introduction of mold, stains and rust. Traditionally, importers implement stricter controls to prevent mold as temperatures increase during Spring. However, these controls are placed on products that would usually ship immediately after production. Extending the storage time of goods in warehouses and factories without timely quality inspections greatly increases this risk.
Once factories resume production and goods can once again flow, the inevitable rush to get the products into containers and onto ships will begin. The prospect of delaying shipment further by conducting inspections of the goods may be too much for some manufacturers, who could be tempted to skip the process to meet deadlines. We urge taking the utmost care before making a decision to avoid regular quality assurance measures unless you are certain those goods have been stored in a controlled environment and are free from moisture or other environmental impacts that can cause quality issues. A quick pre-shipment inspection on a limited sample size produced before Chinese New Year can significantly reduce this risk by checking the area where the goods have been stored, the condition of the packaging, the moisture content of the products, and inspecting a sample of the goods to ensure they are free from mold.
An alternative to time-consuming quality inspections
The abrupt shutdown of factories often results in goods left at varying stages of completion. Other countries may face similar issues in getting their workforce back once operations resume, for example, in India where many workers have returned to their hometowns during the lockdown period to avoid the high cost of living in the cities where the factories are located. Furthermore, once production resumes, it may take time for the workforce to pick up where it left off – and there will be pressure to get the goods out as quickly as possible.
Factories will no doubt push to get the goods out as soon as possible and, as is natural when one has to quickly pick up a semi-completed task and is under time pressure to complete it, mistakes may creep in. Such errors during manufacturing processes invariably result in a defective product and harm to the brand’s reputation.
One solution we recommend that would reduce the time impact on the quality inspection process would be the implementation of In-line monitoring, or a During Production (DUPRO) inspection. This prompts the factory to adhere to its own internal quality control processes, and allows the importer an objective third-party inspection of the goods. Providing there are no major quality issues found during this process, an importer may more comfortably take the decision to ship the goods without a final pre-shipment inspection (PSI), avoiding further delay.
As was experienced in China, local governments had implemented strict controls on the resumption of normal operations of companies once the spread of COVID-19 had been controlled. While it remains to be seen how other countries will handle this process, factory operators in less developed countries may be inclined to get operations moving without waiting for the required approval.
With or without such approval, factories will naturally want to paint an optimistic picture for their clients and, therefore, may provide inaccurate information as to the operational capacity of the factory. This presents a challenge in understanding the real situation in the factory.
Furthermore, factories may increase overtime in order to meet deadlines or run overnight shifts/double shifts which can lead to social compliance issues.
In-line monitoring and During Production Inspection will afford the opportunity for a third-party quality control company to first check that the factory has the required authorization to resume. However, it may not be easy for the inspector to obtain a comprehensive understanding of the factory’s operational capacity since they are not usually privy to seeing the full operation when visiting for inspection.
Factories are also unlikely to accept a factory audit from a regular customer as it could be seen as a sign of mistrust and can place an administrative burden on the factory in preparation.
Having an inspection company conduct a factory visit is something that can give the importer an objective view on the factory to ensure they have the required government authorization (if applicable) to resume operations, check on the production capacity of the factory (orders in production and staff working), as well as the shift work timetables of the factory to indicate any potential excess working hours / social compliance risks.
Conclusion
While the full extent of the impact of COVID-19 on global supply chains remains to be seen as the virus continues to spread, customers’ expectation of availability of products in the market may be more flexible. However, consumers are unlikely to compromise on their expectations of the quality of the goods they purchase.
Similarly, the requirements of retailers and product safety regulators will not change in terms of product and factory compliance.
AQF, as a leading third-party provider of quality control and factory compliance solutions operating in all major manufacturing centers, is well-placed to provide objective views on local manufacturing conditions and assist you to manage product quality and factory compliance risks during these uncertain times.
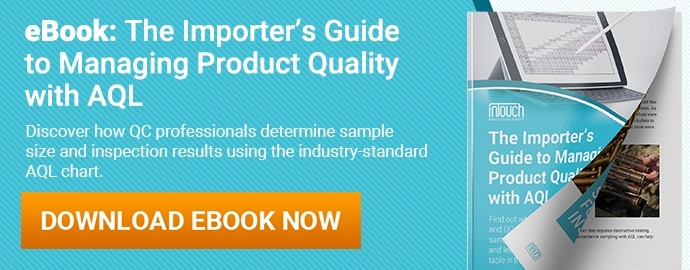