Brand reputation is crucial in the retail industry. But one simple mistake, one simple workplace accident can cause damage that may take years to repair.
Factory accidents are more common than you might think. The U.S. Bureau of Labor Statistics confirmed 2.6 million nonfatal workplace-related injuries and illnesses in 2021. This number indicates that not enough brands are taking manufacturing safety guidelines seriously and holding their suppliers accountable.
Injuries and accidents on the factory floor can equate to major losses for a brand. Whether that be a damaged reputation due to public perception, or loss of inventory due to fire or improper storage, manufacturing safety guidelines can provide an added layer of protection.
This article will discuss how brands can help to minimize these risks and prevent losses due to workplace accidents.
Recent Factory Accidents And Their Impact
Accidents and injuries in the manufacturing sector are more common than you might think. In fact, factory fire alerts increased by 129% between 2020 and 2021, as reported by CNN. Below are some recent examples of factory accidents that have highlighted the need for a stricter enforcement of safety guidelines industry-wide.
In December of 2022, it was reported that two serious industrial accidents took place at a German factory, resulting in one fatality and another critical injury. Both incidents received backlash and are thought to be the result of “workers who are poorly equipped for the tasks they are assigned” which includes working in dangerous areas and around hazardous materials.
Although manufacturing safety guidelines are often put in place by regulatory agencies, these recent accidents show that those guidelines are not always closely followed by the factories. Brands and retailers need to take extra precautions to ensure they are partnering with suppliers who are socially responsible in order to protect their reputation.
Why are manufacturing safety guidelines important?
Factory accidents can damage a brand in many different ways. The public does not care who was at fault and customers may boycott your products if they feel you were responsible. Between fines and penalties, legal implications, and brand reputation, there are a lot of reasons to pay attention to a supplier’s manufacturing safety guidelines.
Adhering to these regulations keeps employees safe and also reduces the risk of liability for your brand. Compliance with industry standards also allows companies to create an effective safety culture, ensuring all stakeholders are safer.
Perform These Four Safety Checks When Auditing Suppliers
A social compliance audit can help to assess your supplier’s working conditions more thoroughly. But most importers can still tell the difference between a safe and unsafe working environment by visiting the factory and performing these standard safety checks:
1. Wearing protective gear
Varying manufacturing niches require different protective gears. Check to see if employees are wearing appropriate safety gear, like:
- Steel-toe boots
- Earplugs
- Helmets or hard hats
- Face protection
- Other safety equipment when appropriate
2. Protecting heavy machinery
The Occupational Safety and Health Administration (OSHA) recommends the use of guarding devices like barrier guards to protect workers from dangerous machinery. It bases this argument on machine operators who racked up 18,000:
- Crush injuries
- Amputations
- Abrasions
- Fractures
- Lacerations
3. Factory design and layout
The factory layout and general design weren't 100% designed with safety in mind, but they can definitely impact a factory’s safety standards.
For instance, anti-slip flooring and appropriate lighting fixtures to ensure visibility can go a long way in preventing accidents. Wide isles and adequate space between machines also help reduce the risk of accidents.
4. Material storage
Materials need to be safely stored and organized to minimize safety hazards. All factories should keep hazardous chemicals and combustible materials away from ignition sources. They should also be using certified storage racks and shelving without overloading.
The factory itself must also be in good condition. A supplier’s storage area should be secure, dry, and of sufficient size to store the required materials.
Make sure your supplier is exercising caution when transporting hazardous materials from one area to another within the factory. This means that workers should be wearing protective gear and using the proper equipment, such as forklifts, handling trucks, or Automated Storage and Retrieval Systems (ASRS).
How A Social Audit Can Help
Workplace accidents can be damaging to your brand, but performing a social compliance audit demonstrates to your customers that you are socially responsible. With a social compliance audit, you can:
- Identify and partner with ethical suppliers.
- Show your customers that you are socially responsible.
- Protect and enhance your brand and reputation.
- Avoid dangerous work conditions.
- Assist vendors to improve their processes and develop better overall human resource practices.
- Prepare your supplier for corporate social accountability accreditation.
At Asia Quality Focus, we appreciate the importance of safety within your manufacturing process. That's why we provide a comprehensive social audit that examines all the essential aspects of your supplier’s operations.
Contact us or sign up or AQF Online to book a social audit today.
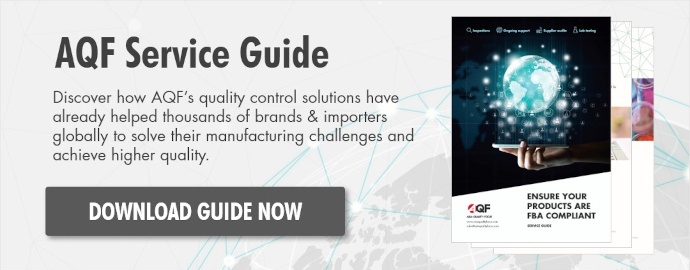