A shortage in quantity is one of the most frequent problems affecting retail supply chains. When shortfalls occur, the products cannot be distributed to the different resellers in the expected volumes. End consumers may be frustrated, and product costs can increase. How can you control the total quantity shipped to you more effectively? How can your quality partner in Asia assist you?
What are the methods to check finished goods quantity?
An inspection reviews several important aspects of a product: workmanship, specifications, quantity, functionality, and safety. Unfortunately, limited budgets don’t always allow examination of all those areas in detail because it requires significant time and increases inspection costs. Therefore, time is limited and inspectors use the most efficient methods of control possible, within the available resources.
How do we check the finished goods quantity today?
A
quality inspector commonly
counts all units present in 3 cartons and then determines the number of cartons in the batch without removing them from the storage area. Simple multiplication determines the total number of units in the consignment. This method provides a good compromise between accuracy and workload in most situations. But there are better ways to proceed, depending on the circumstances.
Counting each piece, one-by-one
This process may require that every single carton is opened and examined by the quality inspector in collaboration with factory workers.
After counting, personnel must repack and seal the cartons, then re-organize them in the warehouse. There are faster counting methods that exist such as the use of the conveyor belts to count the goods before packing into master cartons. However, this implies verification of quantities during the production and before packing. Any other method requires approximations rather than exact numbers. However, this technique needs considerable space which most warehouses can’t offer. It also requires a substantial amount of time and human resources – i.e., factory workers plus QC personnel to supervise the job is done properly.
Units and carton weight
A second, alternative method to check the finished goods quantity consists of checking the number of units in one carton and then determining the total weight of the carton with those contents.
Inspectors can then verify if the weight of all the other boxes is the same. This process takes considerable time as well, but far less than checking the contents of every single box. The challenge with this method is that warehouses are usually tightly packed and the space between each lot is narrow. The quality inspector has to find enough room to move the cartons out of their storage location to weigh them all one by one. To do this effectively, he needs the collaboration of several factory workers, for a few hours. The underlying premise of this method is that all cartons and products weigh the same without exception, and it is therefore somewhat of an approximation.
Let’s take an example to deepen the understanding of the methodYou decide to import 50,000 bags and get them manufactured by one of your supplier in China. In total, there are 2500 export cartons, which contain 20 bags each.During the inspection, the Quality Inspector will open one carton then count the number of pieces and verify that there are 20 pieces in the carton. He will then put the 20 bags back in the export carton and verify the gross weight. In this case, the G.W. is 8kgs. He will take this value as a reference to verify the gross weight of the other 2499 export cartons.
Define the inner volume of each carton
A third approach is to measure the dimensions and thickness of a carton to define the inner volume. If you know the unit packing volume, you can then estimate how many units should be inside one box, and multiply that by the number of packages to get a total.
With this method, you need to take into account some loss of space. For example, a carton is not always filled 100% by the units but also contains air. Cartons might have dents so fewer pieces can fit inside. Depending on the product, the number of pieces may also vary in each carton.This method is most suitable for products packed in boxes as they guarantee a consistent volume when the packing process is the same. For products like plush toys or cushions packed in polybags, it is harder to guarantee that the factory will be able to pack the items in the same way in each carton.
Let’s take an example to deepen the understanding of the methodYou are importing 500 wooden jewellery boxes from your Chinese manufacturer. The Quality Controller will measure the volume of your packed products to determine their volume. In this case, each box is packed in a gift box measuring 31x21x13cm. Therefore the product volume is 0.0085m3.The Quality Controller will then measure the inside of one export carton to determine its inner volume. After removing all goods, the measurement is 43x25x35cm. Therefore, the inner volume of each export carton is 0.0376m3.By dividing the product volume with the export carton inner volumes, the QC concludes that only 4 pieces can be packed per export carton (0.0376/0.0085 = 4.42).After that, the QC will count the number of cartons ready. In this case, he counted 100 cartons and can then conclude the total number of pieces finished and packed: 100x4 = 400 pieces. This means that there is a quantity shortage, not all goods are ready for shipment, as 100 jewellery boxes are missing.
Changing to a more
reliable and complex method to check finished goods quantity increases the chance of
receiving 100% of your order. However, the workload and your costs also increase, and you must ensure the check is performed at the right time for the best result.
Pre-shipment inspection is usually considered the best quality control solution to check quantities, safety, and conformity to your requirements, but who knows what happens after the inspection is finished? Due to lack of time on the day of inspection, third-party QC companies do not usually supervise the re-packing of the inspected goods. You must, therefore, rely on the goodwill of the supplier and their workers to repack them all after replacing or reworking the defective goods.
So, how can you guarantee the total quantity in each carton and that all of those cartons will be loaded into the container?
As discussed above, the quantity check procedure can be adjusted to verify the total quantity of the shipment with more or less approximation. However, the time at which this check is done is as valuable as the check itself. Ideally, it should be at the very last “minute” to allow the best control and supervision of the consignment.
We recommend you send your third-party inspection company to
supervise the loading of the container to remove any doubt.
Learn more about
Container Loading Supervision.
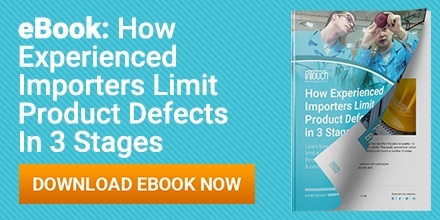