Plastic product inspection is one of the most commonly conducted inspection because so many industries require high quality plastic components in manufacturing their products (related: Top 5 Injection Molding Defects to Avoid).
Product inspection is one of the best ways plastic component manufacturers can ensure their product meets their customers' requirements. Let's look at some of the common procedures included in a professional inspection of plastic products:
Visual inspection
- Color comparison – compare product color with pre-approved samples or with specified values in the Pantone color chart.
- Manufacturing damage inspection – visually check for production defects, such as bumps, depressions, chipping and cracks.
- Crocking check – verify coating and finish quality by rubbing product surface with a wet white cloth and then checking for any sign of pigment transfer.
- Opacity evaluation – evaluate the degree of opacity of the product using an opacity meter.
- Transparency evaluation – determine the transparency rating of a plastic product using an applicable tester.
Materials inspection
- Raw material verification – verify that the quality and quantity of raw materials used in your product conforms to specifications.
- Lead content testing – check the materials for any traces of lead. This is typically part of composition testing, which should be performed by a qualified laboratory.
- Food safe inspection – verify that product materials adhere to regulations and industry practices for food-safe plastic products. Like the lead content testing, a certified lab should typically conduct tests for food safety.
Packaging Inspection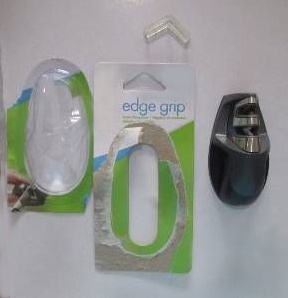
- Packaging materials and procedure verification – check that the materials and procedures for packing your product follow contractual specifications and that your product is able to withstand shipping. Use the carton drop test if applicable.
- Retail packaging inspection – check that the retail packaging satisfies your marketing requirements. This often includes inspecting the logo and labels, dimensions and thickness of packaging materials, ease of assembly, safety labels, clarity and color of prints, overall appearance and user manuals.
Dimensional inspection
- Individual parts inspection – verify that individual parts adhere to measurement specifications.
- Assembled product inspection – verify the measurements of an assembled product follow contract specifications.
- Weight check – check the weight of the assembled product and individual parts for compliance with specifications.
- Volume check – verify the effective volume capacity of the product.
- Thickness check– measure the thickness of critical product parts for deviation in design.
- Uniformity inspection – check for any product uniformity issues, including appearance, volume, weight and geometric measurement. Product deviations must not exceed industry limits.
Specific plastic inspection protocols
Fiber-reinforced plastics (fiberglass)
Fiberglass has diverse applications. It's commonly used in automotive components, pipes, hot tubs and other products.
- Gelcoat finish – thoroughly inspect the surface of fiberglass products for any sign of defects. Verify that materials and procedures used comply with gelcoat-finished product requirements.
- Cure evaluation – determine if the product's surface has been cured to the required degree by using tests like the Barcol hardness test and the acetone sensitivity test.
- Corrosion resistance – fiberglass products are highly non-corrosive given that they adhere to certain industry requirements for materials, design and production. Corrosion resistance tests are applied according to your specifications.
Plastic containers inspection protocols
The following procedures are applicable to plastic products that are meant to contain liquid substances, such as water tanks and HDPE bottles.
- Resin identification code (RIC) verification – verify that resin used in the plastic is the same as the declared RIC in bottle and rigid container.
- Liquid penetrant test – conduct this test to evaluate the permeability of the plastic product.
- Constant-top-load test – evaluate the ability of a high-density polyethylene (HDPE) bottle to withstand top-load pressure that occurs when bottles are stacked on top of each other.
- Elevated internal pressure test – tests the product's ability to withstand internal pressure build-up caused by environmental rise in temperature and humidity.
Every plastic product requires a different set of inspection processes. We recommend using qualified inspection experts to help you develop processes that address your specific product needs.
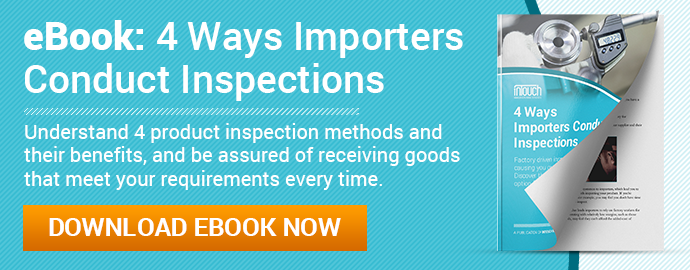