QC inspectors are the very heart of any QC company. They are the client’s eyes and ears on the production line. They are the ones who scrutinize every product being assembled and make sure everything is up to the buyer's standards. A quality inspector need not only receive a buyer’s requirements and verify whether or not a product meets standards. A quality inspector also needs to be able to point out issues a buyer might not have anticipated. In turn, inspectors are able to inform the manufacturer and, often, advise them on how they can improve the quality of their products.
Below we follow the steps of the hiring process for a quality inspector and what we look for to make sure we’re hiring qualified and competent QC staff.
Recruiting quality inspectors
Like most companies, we start off with job postings on job-hunting websites and attend job fairs. However, we have very specific guidelines on how and where the resume should be sent. Followed by stringent requirements on what information should be on the resume itself.
We also require the candidate to answer questions based on the instructions. Anyone who does not follow the instructions exactly as stated is out of the running because, as a quality inspector, attention to detail is vital. We want people that can successfully follow specific instructions and communicate them afterwards.
Resume review and selection
Applicant resumes are sent to HR for further review into the applicants qualifications. The answers to the initial questionnaire are reviewed and the candidates work experience is verified. Requirements can differ somewhat depending on the type of product inspector. For example, if an inspector is needed in Ho Chi Min City to inspect raw fabric, the ideal candidate would be located in or nearby that area and would know how to grade fabric, use a fabric inspection machine, etc. Only resumes meeting all the requirements will be passed on to the appropriate quality manager.
Phone call notification
The quality manager vets candidates a second time and contacts those that seem to fit the job by phone. The resume will then be passed down to HR again, in order to schedule a face-to-face interview if the quality manager believes the person is right for the position.
Interview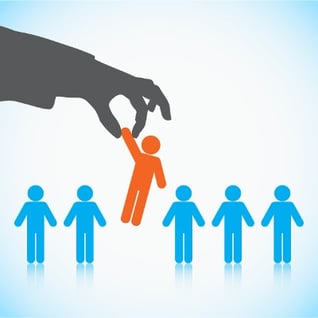
HR follows up with the candidate to schedule a face-to-face interview. All the appropriate information, with the schedule of the interview and directions to the office, is sent to the candidate. Candidates located in a remote area far from the nearest InTouch office can schedule a video Skype interview instead. The candidate is asked a series of questions to verify their capability and knowledge of the quality field and inspection process. After the interview, the quality manager talks with the candidate in person.
Offer
A job will be offered, to the right candidate, after their interview with the quality manager. Even after the offer is accepted, the inspector will then enter a 3 month probationary period before an official long-term contract of employment is signed. However, all the appropriate insurance is provided for the inspectors from their 1st day on board.
Conclusion
The selection process for a proper quality inspector is important because inspectors have the most important job in the firm. In order to ensure accurate reporting of the status and quality of an order to buyers, we have to make sure only the most qualified individuals are selected. Check out our Careers page to learn more!
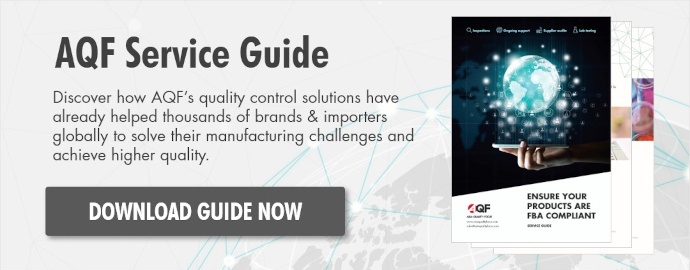