Examination of sleeping bags in different phases of the manufacturing process ensures quality compliance right down to the most elemental detail of the product.
Sleeping bag inspection and quality control tests are commonly characterized in the following categories:
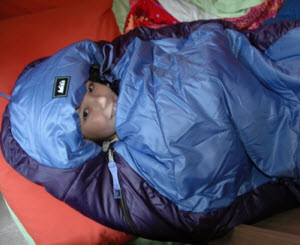
- Pre-production Inspection : Raw materials required for making sleeping bags are tested primarily to ensure they meet quality standards.
- During Production Inspection: During this stage of the manufacturing of sleeping bag’s, quality control specialists will check for any problems and defects in a partially completed and completed sleeping bags. These inspections allow to make any necessary adjustments to the product if required before shipment.
- Pre-shipment Inspection: This test takes place when the production phase ends and the sleeping bags are ready for shipment. These tests evaluate the quality of the product, its packaging values and adherence to safety procedures.
Key points for QC of sleeping bags:
To test the quality of a sleeping bag, ASTM tests and International standards are used for inspection and testing phases. Below are a few key sleeping bag inspection’s performed:
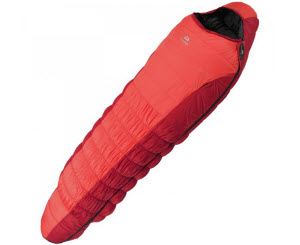
- ASTM F1720 – 6 : is used to analyse the insulating capabilities of a sleeping bag. A human model is heated and the insulation capability of the sleeping bag is thus determined via measuring the transfer of heat energy and temperature rise.
- ASTM F1955 – 99 : is used to measure the burn rate of various materials used in the manufacturing of sleeping bags. Labeling requirements are also needed to properly identify that the sleeping bags conform to this particular test method.
- ASTM D4524 – 86 :is used to test and standardize the plumage used for the interior filling inside the sleeping bag. The test method can be used for plumage found in a raw form or inserted into a finished product.