So where did Takata go wrong? Clearly, inadequate product testing and quality control processes were a major contributor to the crisis - specifically, airbag inflator testing. Let's examine this by taking a brief look at some of the credentials needed by testing professionals and the safety and function testing Takata should have been conducting.
Insist on Accreditation
Whether an auto parts manufacturer is performing the testing itself or enlisting the aid of a third-party inspection firm to do testing on its behalf, engineers performing this kind of testing should be done by professionals that possess the following or similar generally-accepted accreditations:
A2LA ( ISO/IEC 17025 c)
Certification by the American Association for Laboratory Testing ensures technical competency of staff, traceability of measurements and calibrations to national standards, suitability of testing equipment, quality assurance of testing data and other aspects of testing. Labs with this type of accreditation are lower risk and can save the manufacturer money that might be spent on repeat testing.
AMEC
The Automotive Manufacturers Equipment Compliance Agency sets criteria and standards for safety equipment related to auto manufacturing. AMEC maintains a list of existing laboratories that have achieved certification, a list of compliant automotive safety devices and a list of acceptable plastics for optic lenses and other parts in vehicles.
VCA
The Vehicle Certification Agency is a branch of the United Kingdom's Department for Transport and the country's foremost authority on certification for all on-road vehicles. Although the VCA is concerned mostly with providing certification related to performance standards, it also ISO Management Systems Certification, including ISO 9001, ISO/TS 16949 and others.
Airbag Inflator Testing for Safety
Now that we've reviewed the recommended certifications quality engineers should have in order to assess safety and quality of automotive components, let's get into testing. But first, for those of us unfamiliar with airbag inflators, how do they work? An airbag inflator, as you might have guessed, initiates deployment of the bag in the event of a car crash. Most modern vehicles are equipped with a dual inflator where one inflator deploys the bag during a low speed collision and the other deploys the bag during a high speed collision. Airbags contain a ballistics component known as an initiator, or bridgewire, which triggers the discharge of gas to inflate the airbag once it receives a signal from the crash sensor. The initiators need to be tested for resistance to be sure that an airbag will inflate properly and with the right intensity.
Aside from the more general airbag tests common among manufacturers, such as static & out-of-position deployments and fixturing, an auto manufacturer would definitely want to see some specific testing results for airbag components. Let's look at a few of them here and how they might have prevented the Takata issue.
Initiator Test
One essential part of airbag inflator testing is the initiator test. The initiator is connected to the inflator at two terminals and is coated with a primer. When sufficient current is passed through the wire a flashpoint is reached, and the initiator triggers inflation. To test the resistance of the initiator, current is supplied to the wire and a resulting voltage drop is measured. In the case of dual inflators, there will be two separate initiators that need to be tested. Typical resistance for initiators is 2Ω (Ohms).
Insulation Resistance (HIPOT) Test
A standard test for any electronic product is insulation resistance testing, or hi-pot testing. In this instance, we're concerned with the insulation resistance between the initiators and the housing. A test voltage, typically of 500V, is applied to one of the leads of the initiator and the housing, and the resulting current is measured. An acceptable insulation resistance usually ranges from at least 10MΩ (megaohm) to 100MΩ.
Shunt Bar (Shorting Clip) Test
There is a risk that a buildup of static electricity during handling or installation of the initiator could discharge and inflate the airbag. A shunt bar, or shortening clip is often installed across dual inflators to prevent this. Shunt bars should be tested for resistance with a current of 50mA (milliAmps) or less, so that a defective shunt bar will not lead to ignition of the initiator. Acceptable resistance for the shunt bar ranges between 10–100mΩ.
Conclusion
All of these tests are used to ensure the safety and functionality of airbag inflators and their relevent components. If Takata had been accurately and deliberately carrying out airbag inflator testing on a routine basis, perhaps they could have avoided their current predicament.
It comes as no surprise that some automakers affected by the airbag recalls are asking others to band together to fund independent components testing by reputable third-parties. And while the root cause of the airbag inflator problem is still unknown, it's clear that sufficient testing and quality control measures were not taken early on by Takata.
Click here to learn more about third-party inspection and testing services for automotive parts.
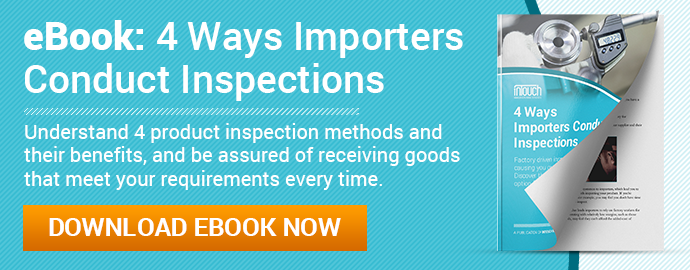