If you’ve subjected your products to rigorous product testing for proper function, toxic substances, and general safety, then they are 100% ready for sale in the U.S. market right? Wrong.
The stark truth is that any of your products bound for stores in any one of the 19 U.S. states shown below (and the list is growing) must also be tested for toxic materials such as heavy metals. Other states as well as the U.S. Congress have also considered the legislation, it’s a fairly safe bet that TPCH legislation will be adopted nation-wide as heavy metals become an increasing concern.
The states that have already enacted legislation based on the TPCH model are California, Connecticut, Florida, Georgia, Illinois, Iowa, Maryland, Maine, Minnesota, Missouri, New Hampshire, New Jersey, New York, Pennsylvania, Rhode Island, Vermont, Virginia, Washington and Wisconsin.
What is TPCH?
The Toxics in Packaging Clearinghouse (TPCH) was formed in 1992 in response to the huge amount of heavy metals in packaging and packaging components that are sold or distributed throughout the United States. Originally drafted by the Source Reduction Council of CONEG in 1989, TPCH has refined and put forth model legislation meant to promote testing and regulation of heavy metals in packaging.
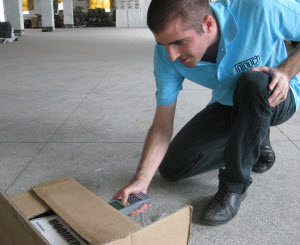
While exposure to individual sources of heavy metals do pose a health risk, TPCH legislation is meant to address the issue in a more far-reaching environmental context: “Since packaging comprises approximately one-third of the waste stream, it is hoped that this legislation will curb the amount of heavy metals entering the municipal solid waste stream and, ultimately, landfills and incinerators. A reduced contribution of these metals to the waste stream will gradually lower their harmful presence in the environment.”
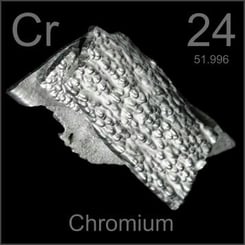
Four specific heavy metals are targeted for elimination or reduction: mercury, lead, cadmium, and hexavalent chromium. Scientific studies have shown that these metals pose significant environmental and health hazards, especially when introduced to the atmosphere as incinerator ash and stack emissions or into soil and groundwater via landfill leaching.
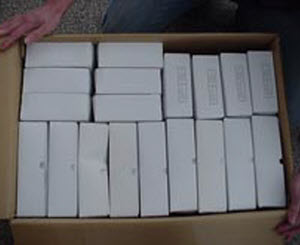
TPCH Legislation
According to TPCH model legislation companies are not permitted to sell or distribute any package or packaging component to which any of the four metals has been intentionally introduced. There is an important distinction to be made between the presence of these metals as intentionally introduced substances and those that are incidentally present.
For example, lead processed from used automotive batteries and used to manufacture an ink pigment that is then used to print labels would qualify as an intentionally added toxic substance. Companies are allowed 2 years from the time the law is enacted to clear inventories and reformulate packaging to ensure intentionally introduced substances are adequately reduced.
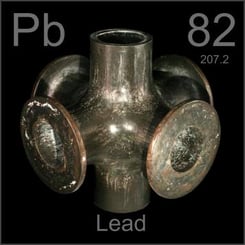
Incidental presence is defined as the presence of one of the four regulated metals as an unintended or undesired component of the final package. Trace amounts of residual metal resulting from the use of a processing aid or similar material during production of a product (i.e., used as a cleaning or oxidizing agent) from which a package or packaging component is manufactured would not make the final package or packaging component non-compliant if the total residual metal level were below 100 ppm, as this is not considered intentional addition of the regulated heavy metal.
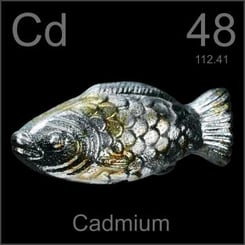
The distinction is made because these processing aids are reasonably expected to be consumed, transformed into a non-regulated chemical during the process, washed or dissolved away, or otherwise nearly all removed during processing. The incidental presence of these metals must be gradually reduced to 100 parts per million four years after TCPH laws have been enacted.
Incorporate toxics in packaging requirements into your packaging specifications
In addition to dimension, color, and durability requirements for you packaging also include maximum toxic material contents restrictions.
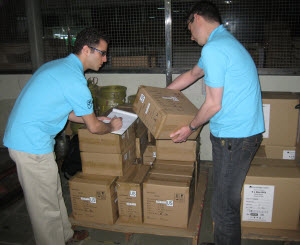
Maintain a direct dialogue with your suppliers
Don’t assume that suppliers have read and adhere to the packaging specifications, or know about restrictions on the use of heavy metals in packaging. Talk to them about these requirements, encourage them to ask questions, and follow up with answers as best you can. If you have questions yourself, contact an accredited 3rd party laboratory for clarification on TPCH requirements.
Require proof of compliance
Require suppliers to provide a Certificate of Compliance with supporting documentation. Ask suppliers to provide the analytical data on which they base their compliance claim. Require suppliers to submit new Certificates of Compliance with supporting documentation whenever their suppliers or raw materials change.
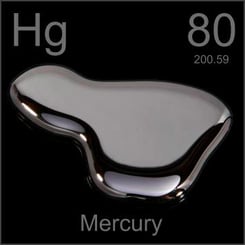
If your suppliers refuse or are otherwise unable to provide this documentation, inform them that you will be employing a 3rd party QC firm to take samples of your packaging and transfer them to an accredited lab for testing.
Minimize supplier turnover
For many reasons, it is beneficial to take steps to reduce supplier turnover and maintain a stable supply chain. Constantly finding new suppliers will require that you repeat the first steps described above often, and possibly at extra expense to you.
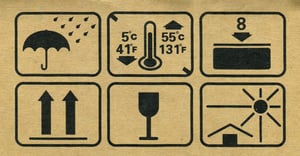
If you do find yourself working with a new supplier, test their packaging materials or components prior to issuing a purchasing contract using x-ray fluorescence analysis or conventional laboratory testing. Select laboratory sample preparation and test methods that result in full dissolution of the sample and analyze for total concentration of each metal. Test methods that only measure leachable metals are not appropriate.
Follow up regularly
Institute an on-going program for monitoring or periodically “spot-checking” incoming raw materials or packaging components to make sure that heavy metals are not subsequently introduced you’re your packaging materials and supplies.
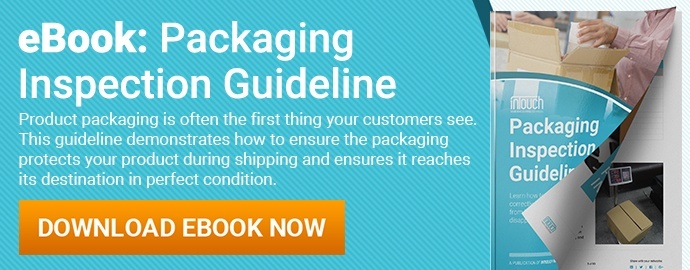