How do most furniture importers ensure their products don’t have wood warping issues? How do cookware importers verify the quality and thickness of the enamel coating on their pans? And how do garment importers confirm that product dimensions meet their sizing tolerances? The answer is most often product inspection.
Pre-shipment inspection of the product is one of the best ways to ensure that an importer’s expectations are met.
Sometimes importers rely on factory QC staff to conduct inspection before shipping the goods. These staff work independently of production workers and don’t report to a production manager. They typically inspect the product at various stages in manufacturing. And they have the power to directly affect production schedules by stopping production lines if a serious issue is found.
Relying on the factory’s own staff to conduct inspection can be a solution for some importers. But for many others, factory staff alone don’t provide the clarity and insight they need. Let’s look at some of the popular reasons why some importers continue to let the factory handle QC, and why most others insist on having someone else inspect.
Why some importers count on the factory to inspect
Relying on factory QC staff may be a reasonable option for an importer that consistently receives high-quality products with few or no serious issues. For importers and suppliers who share this kind of relationship, it’s no surprise that it’s often built on a solid foundation made up of several factors including, but not limited to:
- A detailed QC checklist to clearly note how the goods should be evaluated and what tolerance the importer has for particular defects and other issues
- Approved samples, or golden samples, available for comparison against mass-produced units at the factory; and
- Clear communication between the importer and supplier ensuring that expectations are understood and no questions are left unanswered
But the problem with this relationship is that it doesn’t happen instantly. Suppliers and importers need time to develop a mutual understanding of product quality needs and issues (related: Why You Can't Assume Chinese Suppliers Always Understand Requirements). An importer typically needs repeated success and consistency with a particular supplier before they can confidently rely on the factory’s own QC staff for inspection.
Higher tolerance for quality issues in lower cost products
Often an importer of low-cost products will feel they don’t need outside inspection help because they don’t have strict quality requirements. For example, an importer of promotional sunglasses might assume that end-consumers won’t expect high quality. So they might simply clarify specifications for the product to the supplier and allow QC staff at the factory to check before shipping.
Fear of shipping or production delays
Importers that have promised their customers to deliver goods within a certain deadline may feel compelled to forgo outside inspection. Arranging outside inspection could delay the order, especially when the factory is working on a tight schedule already. So some importers may decide to let the factory handle QC in an effort to avoid delays.
But quite often, importers can use outside inspection, if arranged in advance of a deadline, to keep production on-time. By seeing a report of their order, they can forecast issues and address them with the factory to prevent delays.
Budgetary constraints
Budgetary constraints account for another reason why some importers rely on the factory alone to inspect their product. Many importers working with a low-margin product may feel they can’t afford the extra expense of paying for inspection.
The potential problem is that these importers can end up paying more to repair or rework goods when they receive them defective. And there are several simple ways that importers can cut inspections costs to meet their budget.
Supplier resistance to outside inspection
Another reason why importers may rely on the factory to carry out inspection is pressure from their supplier. Occasionally, an importer might want to bring in outside inspectors but is convinced otherwise by the supplier. And in cases where an importer has already sent their own inspectors, the supplier might complain about the inspection staff. They may suggest the inspectors were “rude” or “unprofessional” during their time in the factory.
The supplier may also complain about not having time for inspection. But regardless of your choice to use outside inspection, resistance from the supplier is a red flag. It often indicates the supplier may be trying to hide something, like substandard working conditions or poor quality.
Risks of relying solely on factory QC staff to inspect
Despite the reasons for importers opting to let the factory manufacturing their goods also check their quality, there are several risks of doing so. As we’ll see here, most importers don’t rely on factory QC staff for inspection due to several reasons.
Reliability and self-assessment bias
Last month people around the world gathered round to watch the Olympic Games in Rio de Janeiro on television. Little did they know they were about to see a major quality problem unfold.
During the medal ceremony following the 10m air rifle competition, officials raised two Chinese flags that did not conform to the official national flag. There are five stars on the national flag—one large star on the left and four smaller ones rotating around it. But the smaller stars in the Chinese flags raised during the ceremony ran parallel to each other. They didn’t match the pattern of the official flag.
Not only were officials at the Olympics unable to catch the issue, but the flags were made in China, and staff at the factory there overlooked the problem as well.
This case study raises one of the most common risks importers face when trusting their product quality to the factory workers themselves—reliability. How reliable is an inspection if it’s conducted by staff employed by the factory that manufactured the product? Although QC staff are separate from those working on the production line, it’s hard to deny the potential for bias here.
Will the factory actually address any issues found during inspection?
Even if QC staff at the factory are relaying accurate information to the factory manager about an order, there’s a good chance the manager won’t act on that information. Doing so will likely require:
- Time, since the supplier may have to notify the importer, who may need to advise how to move forward; and
- Money, since the factory may have to stop production to correct any issues, sometimes with product rework. This usually costs additional resources in the form of parts & materials and human labor.
A factory owner’s desire to ship out POs quickly and continue generating revenue often overshadows QC staff’s duty to inspect your product. In short, factory management doesn’t always have their customers’ interests at heart.
Little or no reporting to the importer
Another key risk of relying solely on factory QC is that you might receive goods with unexpected issues. That’s because, although inspection is generally performed, factory QC staff almost never provide the importer with a detailed report. So you’re left uninformed about what “QC” was actually done and what issues, if any, were found.
A detailed inspection report should include clear photos, any dimensions measured, on-site test results and other important information. Without an inspection report, importers don’t have the opportunity to “see” the goods before shipping. So if there’s a serious issue with the product you likely won’t know until you receive the order.
Reliable product testing results
There’s also the risk that certain testing required for your product wasn’t conducted. For example, fire resistance is a common requirement for the foam filler used in many types of furniture. But it’s difficult to confirm you’re meeting this requirement without having a passing test report that you can verify matches your product. It’s not unusual for factory workers to include a fake certification label with a product.
Linking product damage to transportation or packaging
One point that few importers consider is that, without an inspection report, it’s often difficult to find the cause of any product damage found when you receive the goods.
How can you know if chipped coating on your acrylic picture frames occurred during shipping? And how do you know if broken ceramic dishes in your dinnerware set was caused by rough handling by the factory? These are questions that can only be answered by knowing the condition of the goods before shipping.
Seeing a report of product inspection gives you a lot of assurance of the quality and status of your order before it ships (related: What QC Inspection Results Do and Don't Mean for Your Shipment). And that’s one of the main reasons most importers choose not to rely on a factory’s own QC for inspection.
Conclusion
No two importers are exactly alike, even those that manufacture the same product. Different considerations, such as budget, target market, local regulations and others can greatly influence how each importer manages product QC.
But one statement we can make about importers is that most do not rely solely on staff at their supplier’s factory to conduct product inspection. They know that constraints like budget and timeline shouldn’t interfere with performing a proper check of an order before it leaves the factory.
The extra knowledge that third-party QC provides translates into more control over your goods. And when you have more control, you’re more likely to receive goods that meet your and your customers’ expectations.
And don't forget to check out the manufacturing podcast episode that covers this topic!
Do you have any experiences with product inspection from factory staff? Share them in the comments below!
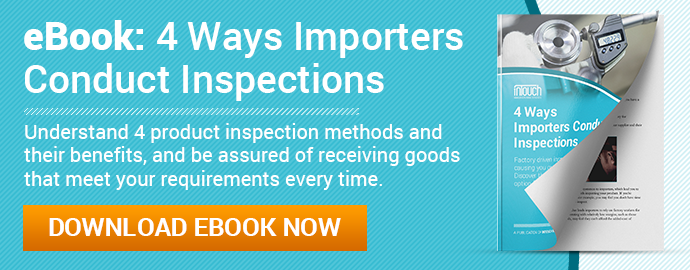