Inspectors make mistakes? Before you gasp and shed any tears, know that there are steps taken to minimize these mistakes.
It’s nice to believe that every product inspection is carried-out perfectly and according to the client’s exact requirements. But the truth is that even properly trained inspectors can make mistakes. We have covered errors that factories make, and ways they can improve, in previous articles.
Now let’s explore the mistakes that can occur during product inspection and the protocols & standards that professional inspectors follow in order to give clients the best possible service and most accurate & transparent reports.
1. Misinterpreting specifications or requirements for product inspection
Specifications and checklists provided by the client are included in the Auditor Service Instructions (ASI) that third-party inspection companies typically provide to their personnel. When an inspector has been examining a certain product for a long time, they may overlook small details or forget an addition to the checklist.
Not reading specs properly can create a wide range of problems, ranging from minor issues to major deficiencies in the reporting and process itself. An inspector might not see that you’ve provided a sizing chart with standards and tolerances for a shoe inspection. This would likely be a relatively minor problem because the inspector would simply report the actual dimensions taken.
But maybe the inspector misinterpreted the sizing chart regarding the method for measuring dimensions. If this is the case, the report you receive would show inaccurate dimensions – a much bigger problem.
There are a couple possible solutions for solving the problem of misreading specs, such as:
- Make sure your inspector clearly understands your specs and requirements for product inspection. Confusion or inaccurate reporting often occurs when there is a misunderstanding or ambiguity involving expectations.
- By rotating inspectors, you can be sure that the person inspecting your goods doesn’t overlook details. This also helps prevent any possible integrity issues resulting from having the inspector become too close with factory staff or management (see more at 5 Easy Steps to Prevent Corruption Amongst QC staff).
2. Not using the appropriate equipment
There is certain equipment that a factory typically needs to provide for product inspections. But auditors also have a responsibility to bring some of their own equipment for inspection and on-site testing. An auditor might:
- Forget to bring the appropriate equipment
- Bring the wrong equipment; or
- Bring equipment that is not calibrated properly and can’t dependably be used
Failure to bring the right equipment that is calibrated correctly can lead to inaccurate reporting. This can be disastrous for you - for example, if you’re importing acrylic sinks that fit a particular fixture and your inspector hasn’t brought calipers for precise measuring.
Any professional third-party inspection company should have pre-service procedures in place to make sure the inspector brings the correct and reliable tools needed for a service. One such procedure includes providing & reviewing Auditor Service Instructions with all involved personnel.
But you can help by specifying, in advance, any equipment that you expect to be required. If you want the specific color of packaging artwork to be verified, for example, be sure to provide the related Pantone code. Then the inspector will know to bring along a Pantone swatch to compare the color.
3. Letting the factory representative influence reporting
Factory personnel may try to convince the inspector that an issue reported as a defect is not actually a defect - or won’t affect item function, and therefore does not need to be reported. Listening to advice from factory reps can be problematic when the issue is not anticipated on the item checklist. Factory personnel have their interest in mind when advising, not necessarily yours.
"Listening to advice from factory reps can be problematic when the issue is not on the item checklist."For example, flash found on a pair of injection-molded sunglasses might require the factory to rework by hand. These sunglasses may be a high-end, premium item so that you cannot accept excessive flash. But if you didn’t specify your low tolerance in advance, your factory might prefer to ship the goods without you knowing about the potential problem.
The inspector should always report any defect or issue that is or might be unacceptable to you, the buyer. You can help by reinforcing this with your third-party inspection company before the service. Advise them that you want any issues or defects that are even remotely questionable to be at least reported. After receiving the initial report, you can offer necessary feedback on the future disposition of any issues you deem insignificant (see Product Inspection Reports – 4 Steps to Getting the Most out of Yours).
"The inspector should always report any defect or issue that is or might be unacceptable to you, the buyer."4. Wrong AQL sample size used
Most inspectors are given specific AQL levels which determine the sample size to be inspected. If the inspector reads or calculates this wrong, it can give the client a very different result, such as:
- Smaller inspection scope than agreed upon, which can lead to overlooking defects; or
- Larger inspection scope than agreed upon, which can lead to you being billed more than you were quoted for the service
Let’s say you’re manufacturing hotel furniture and your inspector should calculate a sample size of 80 pieces for inspection. If the inspector uses an AQL sample size that’s too small, they could be inspecting only 50 pieces. This would make the inspection scope smaller than what you intended and not statistically valid - defects like cracks in the wood or warping could be overlooked.
On the flip side, if your inspector uses an AQL sample size that’s too large, you could possibly be billed more for inspection because of the extra time required.
Most professional inspection reports will show the number of pieces checked and the AQL level chosen. You can use this to cross reference with the service quote provided in advance. Make sure there’s no discrepancy - and if there is, ask your inspection company about it.
5. Missing or incorrect photos in inspection report
Professional inspection reports generally include photos of the items examined, packaging, on-site test results, defects or issues found and any other important details. When there are many items, the inspector might mistakenly:
- Add photos to the wrong section of the report; or
- Forget to include photos which are helpful or necessary to understanding certain findings
Issues with photos can lead to confusion for you while reviewing the report. For example, maybe an inspector has reported damage to a printed label on a piece of ceramic cookware that you’re manufacturing. Without photos showing the extent of the damage, you may not have the information necessary to determine whether to approve shipment of the order.
Reports should be reviewed closely by technical staff before the inspector has left the factory, in case issues with photos or any other areas need clarification or revision. But if you’re confused by photos or any other parts of the inspection report you receive, be sure to ask your service provider to clarify these. Furthermore, if there are photos you’d like to see that have not been included, ask for them to be provided in the future.
Conclusion
Inspectors are people after all, and people sometimes make mistakes. That’s why it’s important that procedures exist to insulate you from problems resulting from an inspector’s mistakes. In most cases, professional third-party inspection companies should provide additional training for their inspectors at least once every six months to help prevent carelessness and improve the overall process.
By being aware of these potential errors, you can remain vigilant and report any mistakes you see. Check out the 4 roles of a QC team to learn more about the duties of the various team members who work to make sure you’re getting accurate reports for every inspection. Be sure to listen to the manufacturing podcast episode that covers this article as well!
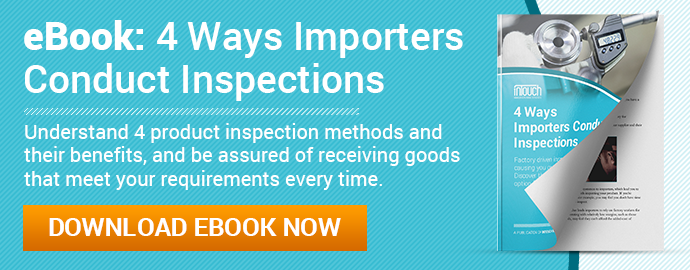