International attention focused on unethical manufacturing practices when in 1996, Kathie Lee Gifford was rocked by a scandal. It was revealed that children as young as 12 years old in Honduras, El Salvador, and China were sewing “Kathie Lee” brand garments destined for Walmart shelves. These laborers worked 14 hours a day in very poor conditions, earning just 22 cents an hour.
High-profile scandals like this one had a huge impact on public awareness and policy: in the United States, congressional hearings were held to get all of the facts surrounding the sweatshops that produced Gifford’s clothing, and President Bill Clinton designated a special anti-sweatshop taskforce. Since then, brands and retailers all over the world have followed suit: Target, Nike, Disney, Apple, and many others have put forth massive efforts to ensure that their merchandise is produced only by suppliers that adhere to certain ethical standards. While there are a variety of social compliance frameworks in use today, many of them overlap considerably, and likewise they often point towards the local law governing their supplier as their own standard.
Child and forced labor, discriminatory hiring practices, and dangerous working conditions are just a few obvious examples of serious social compliance violations. However, not all departures from the various ethical trading frameworks are as readily observable. Social compliance auditors are trained to conduct thorough documentation reviews and evaluations of production, warehousing, and dormitory areas. This training allows them to identify a wide range of social compliance issues. Below, we’ve listed the top 5 violations that most often contribute to a factories FAIL rating during social compliance audits.
5. Child and Forced Labor
These are what are commonly referred to as “ZERO TOLERANCE” issues according to nearly every social compliance framework on record. This means that when child or forced labor is found, the factory has immediately failed the audit, and may even be permanently or temporarily disqualified as a supplier of goods for their client.
Child labor is relatively self explanatory in that a minimum legal working age is set by the local government, and individuals under this age may not be recruited for employment under any circumstances (in China, this age is 16 years old). There are some subtleties to child labor laws, such as in China where there are provisions for the employment of “juveniles,” (individuals aged 16-18) that stipulate their rights to receive compulsory education, restricted working hours, and exclusion from hazardous tasks.
When discussing forced or “compulsory” labor, people often immediately think of prison inmates being used as slave laborers. In reality, forced labor can take less obvious forms. An employer that requires laborers to surrender important documents such as identification or residence/working permits could be in violation of forced labor laws. Without these documents, laborers may have little choice but to continue working for their current employer or face deportation or other consequences. Similarly forced labor could apply in a case where an employer makes large (and often illegal) deductions from employee wages. Employees that are continuously indebted to their employers will face serious obstacles to leaving their current position.
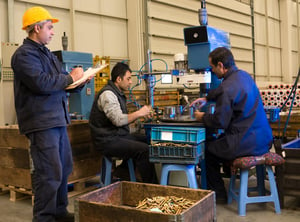
4. Environmental Issues
Some brands and retailers have adopted separate frameworks for controlling the environmental impact of their merchandise. However, in many cases environmental concerns still appear within social compliance standards and regulations, and they remain a part of most standard social compliance audits.
Common environmental infractions involve factories not disposing of their waste materials properly. Any time a factory is venting hazardous fumes directly into the atmosphere or dumping untreated liquid/solid waste into sewage systems or natural bodies of water, it is considered a major environmental issue. Whether required by local law or specific brand/retailer standards, factories must monitor and record their waste materials as well as employ a qualified contractor to dispose of the waste legally. Depending on the nature of the supplier’s operations, as well as the standards they are expected to uphold, noise pollution may also be considered a violation of environmental standards.
[sidebar name="case studies"]
3. Hazardous Working Conditions
Chinese factories run the gamut in terms of safety. Some facilities are generally clean and well maintained, and may exhibit a few minor safety issues that are easily corrected. Others can impose hazardous conditions on their employees, and may not be able to comply with safety regulations without a serious overhaul.
Some very common safety violations that are found during social compliance audits include a lack of personal protective equipment (PPE) provided to employees, lack of or misplacement of fire extinguishers, locked or obstructed exits, lack of emergency lighting, failure to conduct annual evacuation drills, and machinery lacking guards/shields on moving parts.
Protective equipment such as gloves, eyewear, and masks must be provided to all employees that are involved in hazardous tasks such as welding or handling chemicals. Fire safety violations are probably the most common but are also among the easiest problems for a factory to address after a social compliance audit: fire extinguishers are bought and mounted at a reasonable height in an accessible area, emergency lighting is installed or repaired, and evacuation drills are conducted regularly.
2. Wage-Related Violations
In China, the legal required minimum wage varies from province to province (a breakdown of 2012 minimum wage rates can be found here). During social compliance audits, it is up to the auditor to determine whether or not the factory is paying its employees in accordance with the minimum wage laws in their province. To do so, auditors will not only thoroughly review payroll records supplied by the factory, but also conduct employee interviews. Any discrepancies found during this process are reported as possible wage-law violations.
Other common violations related to wages include deductions or unjustified delays in paying wages to laborers, as well as non-compliance with overtime wage adjustment laws. Chinese laborers are legally entitled to 150% of normal wages when working normal overtime hours, 200% when they work on designated rest days, and 300% when working on national public holidays. If pay roll records or employee interviews are inconsistent, or if either discloses information suggesting that wages are illegally garnished, not paid on time, or not adjusted according to special circumstances, wage violations are reported.
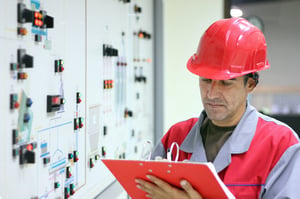
1. Exceeding Legal Overtime Limits
Separate from the issue of whether or not laborers are being paid for the hours they work is the question of how many hours they are legally allowed to work. Chapter 4, Article 36 of the Labor Law of the People’s Republic of China states that “ labourers shall work for no more than eight hours a day and no more than 44 hours a week on the average.” It goes on to state in Article 41 that “work time to be prolonged shall not exceed, however, 36 hours a month.”
Social compliance auditors once again rely on both a critical evaluation of attendance and production records as well as employee interviews in order to identify any overtime related violations. Very often, employee attendance records are found to be at odds with production records: on the same day, attendance records may indicate that an employee who had already worked the maximum number of monthly overtime hours was on leave, when production records show that the same employee had produced 150 components.
In some cases this disregard for overtime limits is consensual – factory management needs to boost output and employees volunteer for more hours so they can earn more money. However, it is equally possible that employees are unaware that they are legally protected against excessive overtime, and so these issues must be investigated during every social compliance audit.