Imagine that your supplier has just sent you a set of samples for raw fabric that you’re ordering. You’ve approved the samples for mass-production. And now you want to make sure the factory has these on-hand as “golden samples” for reference.
So what’s the problem? You were careful to request fabric samples to approve before placing your order – an important step often missed by first-time buyers (related: How Experienced Importers Limit Product Defects in 3 Stages [eBook]). And it stands to reason that you’d want the factory and your own product inspectors to have these samples available for production and then later during pre-shipment inspection.
You’re doing a lot of things right. But to send your approved samples back to the supplier the way you received them is a mistake that can lead to confusion, quality issues and other problems further down the pike.
In a previous article, we talked about how you should never manufacture without a golden sample. Here you’ll learn three best practices for sending the samples you’ve approved for production back to the supplier to prevent issues.
1. Always sign and date the approved golden samples before sending
Your signature written directly on the golden sample is one of the only ways to ensure that your supplier and any inspectors know which sample is approved. This step becomes more crucial when receiving multiple samples for the same item.
Sample mix-up
For example, some of the raw fabric samples you’ve ordered are coated with resin. A resin coating on raw fabric typically affects the hand feel. But the resin effect can be less than obvious. And depending on the fabric, you may not be able to tell which items have resin and which do not by hand feel alone.
You can help ensure the factory knows which golden samples should represent mass production by signing them before sending. If the supplier has not labeled the samples, and you’re unable to tell them apart or indicate which should be the golden samples, you may want to ask the supplier to send new samples that are clearly labeled.
"You can help the factory know which golden samples should represent production by signing them before sending."2. Send one set of approved samples to your supplier and another to your inspector
A lot of buyers fall short when it comes making sure their inspectors are using the correct samples during product inspection. Sure, you can approve a set of product samples and send them to your supplier. You can ask your supplier to make sure the factory keeps them on-site and makes them available to your inspectors.
But sending samples to your supplier alone can lead to a couple issues:
Lost Samples
Approved samples CAN and DO get lost in the factory among tens or hundreds of other samples for other buyers. Your samples might not even arrive at the factory manufacturing your goods if sent to a supplier working with more than one factory. The supplier could mistakenly send your samples to the wrong factory or not send them at all.
Incorrect samples used during inspection
When it comes to product inspection, you want your inspectors to have the correct golden samples available to them at the factory. But if your samples are sent only to the supplier, you place the burden of responsibility on the supplier to make these samples available. And that’s a BIG problem.
You’re supplier – mistakenly or deliberately – might provide inspectors with the wrong samples. Remember that red item of fabric that’s seen a few revision since the sample you first approved last year? That outdated sample could be the one the supplier provides to the inspectors as the basis for comparison.
Along with signing and dating, it’s best to send two identical sets of approved samples – one to your supplier and one to your inspectors. This ensures product inspection is carried out using the samples you approved. It also places the responsibility of using up-to-date inspection criteria on the inspector, which is generally less biased than the supplier.
"It’s best to send two identical sets of approved samples – one to your supplier and one to your inspectors."3. Properly seal golden samples before sending them to your supplier
Let’s say you’ve approved your fabric samples and signed & dated them. Then you’ve mailed one set to your supplier and one set to your independent inspector’s main office. Looking good so far.
But there’s still one glaring problem. Your inspector’s office is located in Hanoi, Vietnam and the inspection site is in Ho Chi Mihn City, more than 1,000km from the place where you’ve just shipped the golden samples needed for inspection. Staff at the office have mailed the samples to the factory so the inspector will have them for inspection.
Tampering with samples
What’s to stop the factory from tampering with the samples? Factory staff could open the package, switch your approved samples with other samples and re-seal the package.
Tampering may seem like an unlikely scenario for you to have to confront. But tampering with samples can be a real problem, especially if your supplier doesn’t welcome inspection from an independent third-party.
You can help prevent any tampering with your samples by making sure the packages sent to your supplier are properly sealed (learn how to seal product samples).
Your product inspector should have their own procedure in place for sealing samples to ensure their tamper-proof. This makes it easy for inspectors to know whether or not staff at the factory have opened the samples when they need them for inspection.
Conclusion
Requesting golden samples is a wise measure before placing an order with a supplier for mass production. Few things can compete in providing more accurate criteria than a product sample that perfectly meets your expectations.
"Requesting golden samples is a wise measure before placing an order with a supplier for mass production."But approving and sending samples to your supplier is often not enough to ensure that they will use the correct ones for production and inspection.
If you’re serious about your requirements and product specifications, take these added precautions to heart. And ask your inspectors about what procedures they have in place to prevent sample confusion, loss or tampering.
Don’t miss the manufacturing podcast episode that covers this article!
Aside from establishing golden samples, there are many other methods for limiting quality defects in your products. Learn more in our eBook below!
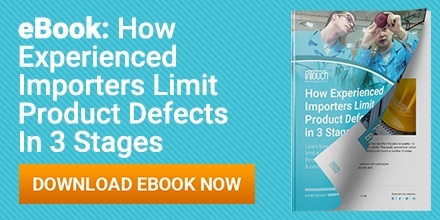