Best in Manufacturing – November 6, 2016
Each Sunday, we publish a list of top articles and other content related to manufacturing in areas like quality control, product development, supply chain management, sourcing, auditing and law.
1. Using big area additive manufacturing for enhanced magnets
Magnets are already pretty incredible. They’re used in all sorts of different applications, like for storing data, producing sound, propelling maglev trains and diagnosing illnesses with MRI machines. And due to the brilliant minds at Oak Ridge National Laboratory (ORNL) in the United States, the process to make magnets is becoming increasingly efficient.
Scientists at ORNL recently demonstrated that permanent magnets made using big area additive manufacturing can perform better than those produced by injection molding. This improved process is great for a few reasons:
- It captures and reuses waste, unlike in standard sintered magnet manufacturing;
- It will help conserve rare earth metals; and
- It allows engineers to create new magnet designs more quickly
Since materials are reused, that could mean cost savings for importers that need magnets in a variety of electronics, from electric vehicles all the way down to head phones. And conserving the scarce materials that go into magnets is a step toward a more sustainable future.
You can view this cool new process in action in the video that ORNL released on YouTube (below):
If you’d like to learn more about the details of this manufacturing process for magnets, check out the full article in the link below:
Researchers Use Big Area Additive Manufacturing to Develop Enhanced Permanent Magnets – Writing staff, AZO Materials
2. There’s more to know about the IIoT than you suspect
Most in the manufacturing industry know that the Internet of Things (IoT) is not to be underestimated. It’s a significant development that, if overlooked, could significantly define how competitive a company is in the future.
Some IIoT articles focus mostly on its benefits. Some go into detail about how the technology works. Some focus on its challenges. But in this article from Machine Design, the author brings a few different aspects together to consider when it comes to the IIoT.
Two aspects he mentions are:
- Acquiring smarter talent and maintenance - Just adding a bunch of smart machines to factories doesn’t mean productivity will improve and costs will immediately drop; you need people that know how to use them, too. Additionally, maintenance of these machines will shift from reactionary to predictive, which will help manufacturers avoid unexpected downtime.
- Understanding the importance of big data - “IoT is a Big Data problem,” says the author, and as such it needs big tools to solve it. The tools need to be adequate enough to handle the volumes, velocity and variety of the data. If your systems can only process two of these dimensions, then you might be missing something big or draw incomplete conclusions.
New technology is seldom fully understood as it’s just being released. Real familiarity of it takes time and firsthand experience. And in the case of the IIoT, staying well informed about it through articles like this will help you adopt it faster and more effectively than your competitors.
To learn about the other two things you must know about the IIoT, check out the full article in the link below:
4 Things You Must Know about the IIoT – Matteo Dariol, Machine Design
3. Success stories of shifting to cloud ERP
Cloud ERP (enterprise resource planning) is a great way to achieve some of the things that all manufacturers dream about, like lower operating costs, a better understanding of your supply chain, automated production and more.
Yet it’s those that have already adopted cloud ERP and the information transformation in manufacturing that will vault ahead of their competitors. The sooner you start collecting data and using a system that can analyze it, the sooner you’ll be able to make real, informed decisions.
The author mentions a few companies that already have this advantage. Specifically, some of them are able to:
- Lower the total cost of ownership
- Increase operational efficiency - Sanko Gosei technologies increased its efficiency by 30 percent after automating many manual processes, leading to lower costs and increased customer satisfaction.
- Improve product cost
- Reduce scrap and inventory on hand - The company Ralco Industries eliminated its inventory inaccuracy and inefficient planning problems after embracing cloud ERP. One improvement? Reducing scrap by more than 60 percent.
- Shift IT resources to value-added activities
- Become lean while improving quality - Wolverine Advanced Materials utilized cloud ERP and saw a 60 percent decrease in overtime and an increase in first-pass quality of 15 to 20 percent.
And these summaries are just a taste of what turning to an advanced digital solution has done for some companies.
If you’d like to read the rest of these success stories and how cloud ERP helped solve common manufacturing challenges, check out the full article in the link below:
6 Manufacturers Use Cloud ERP to Cut Costs – and Position Their Companies for Growth – Plex, IndustryWeek
4. Measuring 3D printed goods isn’t optional
If I told you I was the President of the United States would you believe me? Or would you believe that I can make any product perfectly blindfolded, with my hands tied behind my back, just as your CAD drawing specifies?
If you just doubted my far-fetched claims, you’ve got good judgment. But when it comes to 3D printing, there seems to be a lack of healthy skepticism about parts being made correctly.
In many cases, purchasers of 3D-printed goods believe their parts don’t need to be checked. After all – a 3D printer is supposed to build items bit by bit, so there shouldn’t be any problems, right? But according to the author:
It is a misconception commonly held by the users of 3D printers and encouraged by the vendors that the parts made by 3D printers are made perfectly and within the stated accuracy of the machine and so don’t need to be checked. This is, from the perspective of a quality controller, completely ludicrous but it is a widely held view.
Completely forgoing quality control just because a 3D printer made the item at hand is a terrible habit. It’s imperative to still ensure that items adhere to the same dimensional integrity standards and overall quality found elsewhere in your respective industry. Because, ultimately, if you assume product quality is at a certain level without verification, you and your customers might pay for it later.
To learn about the importance of checking 3D printed goods and ways to do so, check out the full article in the link below:
Measurement Matters – Giles Gaskell, Quality Magazine
5. Big value at the atomic-scale
In the past, mankind wasn’t able to see atoms; they were unperceivable to the naked eye. Gradually, microscopes and other advances allowed us to better manipulate and experiment with them. Nowadays, thanks to scientists pushing the limits of what is possible, developments like diamond nanothreads and super advanced manufacturing materials are closer to becoming a market reality.
Adding to these already remarkable achievements, Robert Wolkow and his team have developed a way to create atomic switches for electricity.
Although the development affects the atomic level, the implications are huge:
We're using this technology to make ultra-green, energy-conserving general purpose computers but also to further the development of quantum computers. We are building the most energy conserving electronics ever, consuming about a thousand times less power than today's electronics.
Although the technology has still not fully matured, Wolkow said he and his team have been working with Lockheed Martin to enter the market. Once Wolkow’s work proliferates throughout the world, we might see green electronics on an unprecedented scale. His work might also lead to a reduction in the number of conventional transistors that electronics need, which could cut costs.
Greener tech for less money – it sounds almost too good to be true, right?
If you’d like to read more about the exciting discoveries happening at the atomic scale, check out the full article in the link below:
When It Comes to Atomic-Scale Manufacturing, Less Really Is More – University of Alberta, Science Daily
We’re constantly scanning the web for top manufacturing stories and news. But if you’d like to submit an article for consideration for our weekly Best in Manufacturing, send us a message and let us know.
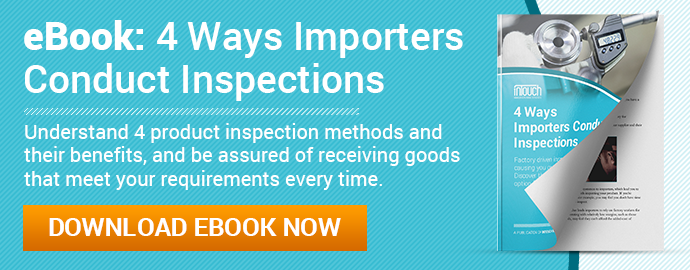