Shipping mistakes can lead to serious product defects, costing businesses money and damaging customer trust. When packages arrive broken, leaking, or unusable, companies face expensive returns, lost sales, and negative reviews. Many of these issues stem from common shipping mistakes like weak packaging, mishandling, and poor environmental protection. Businesses that fail to address these risks may struggle with high damage rates and dissatisfied customers. Here, we'll cover the most frequent shipping errors and how to prevent them. Businesses can reduce product defects and ensure safer deliveries by improving packaging, handling, and carrier selection.
Using Low-Quality Packaging Materials
Weak packaging puts products at risk during transit, leading to cracks, leaks, and breakage. Many businesses try to cut costs with thin cardboard boxes, cheap plastic wraps, or inadequate cushioning, but these materials fail to protect against impact and rough handling.
Poor packaging impacts your business and supply chain efficiency by increasing return rates, delaying shipments, and causing unnecessary expenses. On the other hand, choosing durable materials, reinforced boxes, and high-quality padding reduces the risk of damage. So, investing in proper packaging ensures products reach customers in perfect condition, improving satisfaction and reducing costly replacements.
Ignoring Proper Labeling and Handling Instructions
Shipping labels provide crucial information for safe handling, yet many businesses overlook their importance. Without clear instructions, fragile items may be stacked incorrectly, liquids can spill, and electronics might be exposed to harmful conditions.
Proper labeling helps avoid different types of defects by guiding carriers on how to handle each package. Using "fragile," "this side up," and temperature-sensitive labels ensure safer transport. Including clear barcodes and tracking details also prevents misplacement. Businesses that prioritize proper labeling reduce damage rates, streamline logistics, and improve customer satisfaction by ensuring products arrive in perfect condition.
Avoid common shipping mistakes such as overloading the boxes
Overloading Boxes Beyond Their Weight Limit
Overpacking boxes may seem efficient, but it increases the risk of product damage. When a box exceeds its weight capacity, the packaging weakens, making it more likely to tear or collapse during transit. Common shipping mistakes, like overloading, lead to crushed fragile items, strained box seams, and unstable stacking in trucks or warehouses.
Distributing the weight evenly and using reinforced boxes for heavy shipments can prevent these issues. Businesses should follow weight guidelines and use multiple packages when necessary. Proper weight management reduces breakage, lowers return rates, and ensures products reach customers in excellent condition.
Poor Internal Cushioning and Spacing
Items that shift inside a package are more likely to break, yet many businesses fail to use proper cushioning. Gaps between products allow movement during transit, increasing the risk of cracks, dents, and other damage. Materials like bubble wrap, foam inserts, and air pillows help keep items secure. Fragile products need extra padding and should never touch the box walls.
Overstuffing can also cause pressure damage. Proper spacing and cushioning protect shipments from impact, ensuring they arrive in perfect condition. Businesses prioritizing internal protection reduce product defects, customer complaints, and costly replacements.
Inspect products before shipping
Choosing the Wrong Shipping Partner
Not all shipping companies handle products with the same level of care. Some carriers have higher damage rates due to rough handling, delays, or poor tracking systems. A shipping partner without a strong reputation for reliability can lead to frequent product defects, lost packages, and dissatisfied customers.
So, businesses should research carriers, check reviews, and compare damage claim policies before choosing a provider. Partnering with a trusted shipping company ensures better handling, safer transit, and fewer damaged goods. Investing in a reliable shipping partner helps businesses maintain product quality, reduce losses, and improve customer satisfaction.
Failing to Protect Against Environmental Conditions
Extreme temperatures, humidity, and moisture exposure can severely damage products during shipping. Electronics may overheat, wooden furniture can warp, and food products might spoil if not properly protected. Insulated packaging, moisture-absorbing materials, and climate-controlled shipping options can prevent these issues.
When temporary storage is needed, consider choosing companies such as SkyEx Moving and Storage that offer secure storage solutions to help businesses protect sensitive shipments. Choosing a provider with climate-controlled facilities ensures goods remain in top condition. Businesses that consider environmental factors in their shipping process reduce the risk of defects, ensuring safer deliveries and better customer satisfaction.
Skipping Pre-Shipment Quality Checks
Rushing to ship products without proper checks increases the risk of defects. Many issues, such as cracks, missing parts, or leaking containers, go unnoticed until customers receive damaged goods. Implementing pre-shipment inspections helps identify these problems before they become costly returns.
Checking for packaging integrity, verifying product condition, and ensuring correct labels can prevent avoidable damage. A simple inspection process saves businesses time and money while improving customer satisfaction. Companies that prioritize quality control before shipping reduce defects, strengthen their brand reputation, and ensure that products arrive in perfect condition.
Track and monitor your shipments
Neglecting Real-Time Tracking and Monitoring
Without tracking, businesses cannot control shipments once they leave the warehouse. Packages can be delayed, mishandled, or even lost without immediate action. Common shipping mistakes, like failing to monitor deliveries, increase the risk of damage, customer complaints, and unexpected costs.
Real-time tracking allows businesses to spot issues early and take corrective action before products are compromised. GPS tracking, impact sensors, and automated alerts provide better visibility and security. Companies that invest in shipment monitoring reduce damage risks, improve delivery reliability, and ensure customers receive their orders in perfect condition.
Rushing the Packing Process
Speeding through packing leads to mistakes that can cause product damage. Skipping protective layers, using the wrong materials, or failing to secure items properly increases the risk of defects. When employees are pressured to pack quickly, they may overlook important steps like sealing boxes correctly or adding enough cushioning.
Taking the time to pack carefully ensures products stay protected during shipping. Businesses should balance efficiency with accuracy by training staff on proper packing techniques and using quality materials. A well-packed shipment reduces breakage, minimizes returns, and keeps customers satisfied with products that arrive in perfect condition.
Avoid These Costly Shipping Mistakes for Safer Deliveries!
Common shipping mistakes lead to product defects, costly returns, and unhappy customers. Businesses can prevent damage using quality packaging, proper labeling, and reliable carriers. Careful packing, monitoring, and storage solutions further protect shipments. Avoiding these mistakes ensures products arrive safely, reducing losses and improving customer satisfaction. Investing in better shipping practices benefits both businesses and buyers.
If you don’t have time to check each of the above checkpoints individually, consider working with a professional quality control partner like AQF to simplify your process. At AQF, we have extensive experience in product quality control and are dedicated to identifying defects that could harm your brand's reputation. By partnering with AQF, you can order a pre-shipment inspection for your products that includes various checks, such as packaging materials, labeling, inner and outer boxing, product condition, and more. This way you can minimize shipping errors and improves your product quality. Contact AQF to learn more.
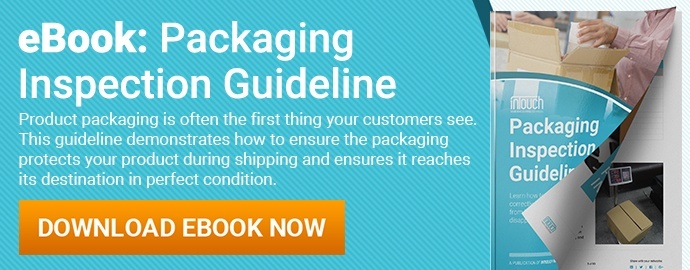