Why is it important to clearly define and classify quality defects for your products?
Imagine you’re manufacturing women’s blouses in Indonesia. A product inspection report from your QC partner shows about one-third of the blouses have untrimmed threads.
Would you classify this quality defect as “minor” or “major”? You might say untrimmed threads are a “minor” defect that don’t affect the salability of the product. Or you might consider them a “major” defect if you distribute your product to a high-end retailer with a lower tolerance for quality issues.
Here we’ll help you get started by explaining the most common ways to classify defects in different products.
What is defect classification?
Defect classification is a vital step for determining if goods should pass or fail inspection. And considering the quantity and severity of different types of defects found helps you make an informed shipping decision.
A professional inspection company often has established standards for classifying various types of defects for a particular product type. But it’s ultimately your responsibility as the buyer to decide your tolerance for different defects, often using a system like Acceptable Quality Limits (AQL) (related: The Importer's Guide to Managing Product Quality with AQL [eBook]).
3 TYPES OF DEFECTS FOR DEFECT CLASSIFICATION
Quality control professionals typically classify quality defects into three main categories. The nature and severity of a defect determine which categories it belongs in.
- Minor defects are usually cosmetic and not considered to be serious
- Major defects may inhibit the product’s ability to function as intended and are considered somewhat serious
- Critical defects may pose hazards and are considered to be very serious
Brands and retailers have the power to specify how many of each type of defect they’re willing to accept in their finished goods. This tolerance, in turn, impacts how many units per SKU an inspector would check during inspection—the sample size.
Importers commonly set these quality tolerances using a statistically valid acceptance sampling method known as acceptable quality limits, or acceptable quality levels (AQL) (related: 10 AQL Terms Importers Should Know to Succeed with AQL for Inspection).
An importer’s tolerance for minor defects tends to be greater than that for major or critical defects, given their relative severity. Let’s look at each of these defect types in detail.
Minor defects
Minor defects are usually small, insignificant issues that don’t affect the function or form of the item. In most cases, the customer wouldn’t even notice a minor defect on a product. And the customer wouldn’t likely return an item due to a minor defect alone.
Importers often set the highest tolerance—or AQL, if applying that standard—for minor defects in their inspected sample size. But an item can still fail inspection if the number of minor defects found exceeds the limit set by their tolerance (related: How AQL Sampling Affects Your Inspection Results).
Major defects
Major defects are more serious than minor defects. A product witha major defect departs significantly from the buyer’s product specifications. Major defects are those which could adversely affect the function, performance or appearance of a product.
These defects are readily noticeable by the customer. And these defects would likely cause a customer to return the product, lodge a complaint or request a refund in response.
Most importers set a lower limit for major defects than minor defects in their inspected sample size. They’ll often accept an order with relatively few major defects. But they’re likely to reject an order or ask their supplier to hold or rework it if the goods fail inspection due to an excessive number of major defects found.
Critical defects
Critical defects are the most serious of the three defect types. Critical defects render an item completely unusable and/or could cause harm to the user or someone in the vicinity of the product.
These defects put businesses at serious risk of product liability issues, lawsuits and product recalls.
Many importers have a “zero tolerance” policy for critical defects in their orders commensurate with this risk. An item will often fail product inspection if a single critical defect is found within the order.
EXAMPLES OF QUALITY DEFECTS IN DIFFERENT PRODUCTS
Different quality defects can appear in different products depending on materials, production processes and standards used. Below are some common examples of minor, major and critical defects in different product types.
Softlines
Softline products include raw fabric, home textiles, garments and other woven or knitted products and footwear. Garments, in particular, tend to be more vulnerable to quality defects because of the labor-intensive production processes involved in their manufacturing.
Human hands involved in sewing and stitching, for example, raise variability in production. Whereas more automated production processes, like the use of injection molding in hardline goods or robotics in electronic assembly, tend to lower variability. This typically results in more consistent product quality throughout a production run.
Some common softline defects include:
- Minor defect: Untrimmed thread – these are common quality issues in garment manufacturing. Factories can easily rework this defect by simply cutting the excess threads. You might also classify untrimmed threads as a major defect depending on your customers.
- Major defect: Missing stitches – these typically appear due to a fault with the sewing machine or an operator error. Missing stitches impact the visual appearance of the product and can even affect seam strength, making this a more serious quality issue.
- Critical defect: Needle found in item – needles can pose a hazard to the end user if they end up in the finished goods. This quality issue is almost always classified as a critical defect. The presence of one such defect typically results in the item failing inspection.
Hardlines
Hardline products include a broad range of goods typically made of metal, wood or plastic materials. This category includes most furniture, sporting equipment, cookware, building materials and tools.
Some common hardline defects include:
- Minor defect: Light abrasion on surface – an abrasion on the surface of a hardline item could be related to a
production process or simply rough handling. Abrasions and other damage to the surface of an item typically won’t hurt the product’s salability, making this a minor defect.
- Major defect: Deep scratch on item logo – damage to an item’s logo is often considered a major defect. Scratches on the logo can be difficult to repair. And they’re generally not tolerated in large numbers, as they can impact product salability and consumer perception of a brand.
- Critical defect: Sharp point or burr on item – sharp points can cause harm to the end user and are often cause for failing an inspection. These hazards often lead to product recalls, which is partly why importers commonly classify them as critical defects.
Electrical and electronic products
Electrical and electronic (E&E) products include consumer electronics, many household appliances, certain toys, power tools and other products that require electricity to function.
Some common defects in electronics include:
- Minor defect: Removable mark on item – marks on the surface of a product can include dirt or excess glue. These are often considered minor if they can easily be wiped away or are otherwise removable.
- Major defect: Non-function or malfunction – malfunction issues with an electronic product might include a failure to turn on, display issues or connectivity issues. Depending on the complexity of the product, rework of software or hardware may be needed to correct the issue.
- Critical defect: Damaged wiring – damaged wiring with copper exposed can endanger a product’s end user. Such a critical defect presents a risk of fire, electric shock, or in severe cases, electrocution (related: 5 Electronic Product Recalls That QC Inspection Could Have Prevented).
Industrial components
Industrial components is a broad term that can include fabricated steel, conduit piping, gas valves, wind turbines, maritime equipment and other machinery or materials designed for industrial use.
Some common defects in industrial products include:
- Minor defect: Surface imperfections – a surface imperfection like a welding protrusion on a steel pipe typically won’t affect the use or functionality of an industrial product. But consider both the type of imperfection and the product’s intended use before classifying such a defect as minor.
- Major defect: Non-critical dimensions out of tolerance – minor deviances in dimensions are undesirable in finished goods but often won’t impact the overall function of an industrial product. You might consider dimensional deviations more serious if they affect product function, performance or subsequent production processes.
- Critical defect: Rust – corrosion before shipping can be a sign of accelerated degradation and product failure. Rust should be a serious concern for you if you’re importing gas or water pipes, for example.
Classifying defects in quality control checklists
A QC professional can often suggest appropriate tolerances for known defects for your product. But it’s ultimately up to you as the buyer to specify your tolerance for each kind of quality defect.
Importers often list their defect classifications and tolerances in a document known as a quality control, or QC, checklist (related: 5 Essentials of a QC Checklist [eBook]). A QC checklist also typically includes other information like packaging requirements, on-site testing procedures and required inspection equipment.
This document should include an exhaustive list of common and known quality defects with your product type.
Accounting for every single quality defect may not be possible. But the more complete the list of potential defects you provide, the more likely your supplier will be to heed your tolerances. Your QC inspector is also far more likely to apply the same standard when checking your products against a complete QC checklist.
A defect classification list might look something like the below example for footwear:
This defect classification information can help:
- Improve your supplier’s ability to proactively self-identify and correct quality defects before outside inspection
- Ensure more accurate inspection results that match your quality tolerances and expectations
- Reduce any cases of “pending” results reported by the inspector due to unclear quality tolerances
This defect classification list might extend to include 20 or even 30 different types of defects depending on your product type. The more information you can provide, the better prepared your QC team and supplier will be.
How to address quality defects with your products
Identifying quality defects in your order before shipment is essential to ensuring your goods meet your customers’ expectations.
Third-party inspection companies can inspect your order and report to you the number and types of defects found in the inspected sample size. Their report will typically show you the total number of defects found in comparison to the number of defects allowed based on your tolerances.
The order will fail inspection if the number of defects found exceeds the allowed number. As you can see in the below excerpt, this order would fail inspection due to the number of minor defects exceeding the allowed number:
While this order would fail inspection based on AQL standards, it’s up to you as the importer to decide whether to ship the order (related: What Inspection Results Do and Don’t Mean for Your Shipment).
You might want to address any quality defects before approving a shipment. To address product defects found in your order during inspection, you might:
- Ask your supplier to correct quality issues through product rework or production of replacement goods
- Re-inspect to ensure product defects have been removed or corrected
- Chargeback your supplier for any re-inspections and quality issues, if you’ve previously set this condition as part of your agreement with them
- Destroy any unsellable goods to prevent defective goods from reaching customers through the grey market
And remember to continually update your defect classifications to add new quality defects or adjust your tolerances for new orders. Updating your QC checklist can help prevent the recurrence of known quality defects in your received shipments.
ADDITIONAL GUIDELINES FOR DEFECT CLASSIFICATION
These are rough guidelines QC professionals typically follow for defect classification (related: Why QC Professionals Use AQL Sampling for Product Inspection). But as the buyer, always consider the severity of different defect types and their effect on your customers and brand when setting tolerances.
Tell your inspector if they’ve classified a defect in a different category than you consider appropriate. This feedback allows them to adjust reporting for future inspections. Likewise, if an inspector finds “defects” you do not consider to be defects at all, inform the inspector to disregard those in future reporting.
These changes help ensure you receive the most accurate reporting possible so you can take appropriate action to address issues before they affect your customers.
If you'd prefer to listen to this topic instead, check out this manufacturing podcast!
STOP PRODUCT DEFECTS WITH AQF QUALITY INSPECTION
If you want to verify 100% of your oders and remove all defective products, the best thing to do is book a defect sorting service from AQF. Our qualified inspectors will examine the entire batch of finished goods in detail before shipment to identify and remove any defective products from the production batch. Defect-free products are shipped while finished goods with defects are discarded or reworked.
Contact us today or sign up for AQF Online to book your next quality inspection today.
Editor’s note: This post was originally published in November 2015 and has been updated for freshness, accuracy and comprehensiveness.
What other quality defects are especially problematic in the products you import? Share in the comments below!
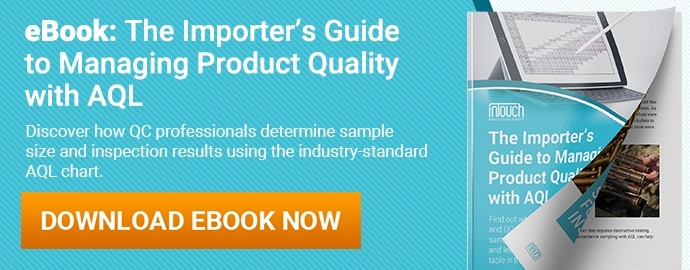