Best in Manufacturing – November 27, 2016
Each Sunday, we publish a list of top articles and other content related to manufacturing in areas like quality control, product development, supply chain management, sourcing, auditing and law.
1. 3 ways to handle a dispute with Chinese suppliers over product development rights
Intellectual property and manufacturing rights in general are at the forefront of foreigners’ frustrations with dealing with suppliers in China. When it comes to product development, especially for hardware, it’s not uncommon for Chinese factories to take product knowledge and manufacture a similar product without their customer’s consent. Many importers find it difficult to work out a fair agreement for maintaining ownership over their product concept and technology.
The author of a recent article published by China Law Blog lays out a few options left for dealing with a Chinese supplier that won’t yield IP ownership to their customer:
License the product technology from the Chinese side
You can negotiate a standard license for the technology and pay a license fee to the supplier. While this type of license agreement is common throughout much of the world, it’s rarely used in China. But it’s becoming more popular as Chinese manufacturer put more effort into monetizing their technology.
You can also negotiate an agreement with your Chinese manufacturer allowing you to manufacture the same product in a different factory if your current manufacturer cannot meet predetermined quantity, shipping date or price terms. This second option can be especially risky if the license only allows manufacturing in a different facility for quantities in excess of a predetermined minimum. The license leaves you at the mercy of the manufacturer if they aren’t capable of manufacturing that minimum quantity, as you’re then limited in the quantities you can produce.
Terminate your relationship with the Chinese manufacturer
While many importers refuse to walk away from a bad relationship with a supplier, it’s often best to cut ties and look for an alternative supplier that’s more agreeable and cooperative with basic manufacturing rights. The author notes that, especially in cases where a startup is seeking investment capital, it’s going to be very difficult to grow their business without having ownership of their product. And a refusal to walk away often mean forfeiting ownership of IP.
“Turn the tables” on your Chinese manufacturer
One other way you can deal with an unruly Chinese manufacturer that wants to seize control of your IP is to treat them as a “test bed” for product development. By experimenting with new technology with this particular manufacturer and avoiding dependence on this single product’s success, you become less dependent on the manufacturer. In this way, you can obtain control over the product because the product is only the foundation for an entirely new product.
The author stresses the difficulty of successfully taking control over their product technology and manufacturing rights, noting:
Many foreign product developers are confident that they can pull off this reversal of roles. They tell me that they will not walk away because they have this plan. In my experience, it is quite difficult to turn the tables on Chinese manufacturers. Chinese manufacturers have been using this strategy themselves for many years and they usually can see what is happening in time to take early action to protect themselves.
With so many importers weary of the risks and lack of legal protection when manufacturing in China, this is a great article for those wanting to steer clear of problems. Read the complete article by clicking the link below:
China Product Development and Manufacturing Rights – Steve Dickinson, China Law Blog
2. Integrated CAD/CAM are bridging the gap between design and manufacturing
Manufacturing has long been plagued by a fairly common problem. There’s a divide between engineers that design products and machinists that actually manufacture them. Machinists are often frustrated by receiving CAD designs that are unworkable or impractical. And engineers struggle to make designs simple enough to be manufactured on a large scale.
A new design tool from Autodesk promises to bridge the gap between design and manufacturing, relieving these problems. Called Fusion 360, the platform combines industrial design, CAD modeling and CAM processes into a single integrated software. The new software makes it easier for engineers to design products that are easy to manufacture, without needing to be familiar with G-code, the basic programming language of machine tools.
How will this new software change manufacturing?
Experts say this CAD/CAM integration will have a positive impact on manufacturing in a few ways, such as:
- Better communication between designers and workers on the shop floor
- Lower cost parts
- Faster time to market, and
- Better understanding of the challenges of mass production part-making
Chris Wilson, who participated in a class to learn the new software said:
[Software like this] is disrupting the status quo by giving designers, who normally don’t have access to CAM functionality, the ability to manufacture proof-of-concept designs in-house. It’s closing the gap between hobbyists and traditional production, allowing for better grassroots innovation.
To read the full story and learn more about how integrated design and manufacturing software is shaping the future of manufacturing, click the link to the article below:
How Integrated CAD/CAM Helps Engineers Design Better Parts for Manufacturing – John Hayes, Engineering.com
3. How importers should respond to changes in the price of raw materials
Anyone who’s manufactured in China or elsewhere knows that the price of raw materials can have a major impact on the overall cost of goods manufactured. But far fewer importers know how to monitor and respond to price changes so that they don’t end up being taken advantage of by their suppliers.
It’s not unusual for suppliers to inform their customers that the cost of their product will increase due to rising material costs. The problem is that it’s often hard to know if your supplier’s price increase is fair. The author of this article points out some important questions importers should be asking whenever they face such a situation, including:
- What is the market price for the particular material in question?
A simple search online can give you reliable data to determine if what effect price changes should have on the cost of your product.
- Is the price increase fair?
Just because your product contains steel, for example, and the price of steel has risen 20 percent doesn’t mean the cost of your product should increase by the same amount. It’s helpful to look at what portion of your product is made of that material, often by referring to the bill of materials. This can help you determine what effect the change in the cost of that material should have on your product (related: 3 Tips for Getting the Best Price from Suppliers). You may also want to request a quote from similar suppliers for comparison.
- Should your product cost always increase?
Sometimes the cost of raw materials can change in your favor—if materials used in your product become cheaper, the cost to manufacture your product should come down as well. But suppliers typically won’t proactively pass the savings on to their customers. By staying on top of changes in material, you may be able to negotiate lower pricing.
- How will changes in the RMB to USD exchange rate affect your costs?
The author advocates taking advantage of China’s currency depreciation, which has occurred over the last few years: “You will virtually always benefit from indexing your prices on the RMB instead of the USD. RMB payments are more profitable in the long term.”
You may have less sensitivity to the price of raw materials than other importers. But price fluctuations for materials can greatly influence many products nonetheless.
You can read the full article for more information by clicking the link below:
Bad News from China, Raw Material Prices Just Increased! – Fabien Gaussorgues, QualityInspection.org
4. Opportunities for machine learning in manufacturing
We often talk about the growing role of IIoT in manufacturing and capturing and analyzing machine data can improve manufacturing efficiency. But we rarely mention the impact that machine learning, a type of artificial intelligence, may have on the industry. Its applications are far-reaching and have already shown positive results for manufacturers.
Put simply, machine learning is the process of machines gathering data, analyzing that data and changing their behavior based on that information. For example, injection molding tooling with machine learning ability might be able to detect poor flow rate, find the cause (e.g. inadequate temperature) and adjust its own settings to improve results. This process of changing based on a predictable outcome is called predictive analysis.
What known results have manufacturers seen with machine learning?
In the case of predictive analysis, machine learning has proven to raise manufacturing efficiency. A report by General Electric found:
- As much as 20 percent of production capacity is recovered when engineers altered equipment using machine learning to improve reliability
- Material consumption is reduced by 4 percent with optimized utility infrastructure
- Finished goods buffers, extra inventory produced during manufacturing, can be reduced by 30 percent or more due to more predictable production capacity
- Product rework can be reduced by 20 percent when more complete quality data is transferred with the product during shipping
There are also a number of other potential benefits manufacturers can reach with machine learning, such as improved preventative maintenance, more optimized supply chains and improved product and service quality.
Read the full article in the link below for a more in-depth overview of machine learning and its potential in manufacturing:
Machine learning drives the future of industry – The Manufacturer
5. Advanced barcode scanning could help your supply chain more than you might think
To many supply chain professionals, barcodes may not be the most glamorous part of their job. And it shouldn’t come as a surprise, as barcodes have been around for several decades. The first scanning of the now mainstream Universal Product Code (UPC) dates back to 1974.
But since coming into mainstream use, barcodes have been a very important part of the way suppliers track products and gather vital metrics data from their supply chains. Now new advancements in barcode technology are improving the efficiency of supply chains around the world. And with consumers demanding more customization and faster results than ever, these advancements can’t come soon enough.
What are these benefits of barcode technology for supply chain managers?
This article, written by a software product director at Accusoft, delves into three ways that new barcode technology is making supply chains more efficient, including:
- Greater accuracy – algorithms used in today’s barcode scanning software help to limit problems with misprinting 1D and 2D barcodes, which has traditionally been a major challenge with scan-ability.
- More transparency – regulations, such as the FDA Food Safety Modernization Act, hold suppliers accountable for product traceability from production throughout distribution. In response, barcodes are becoming more sophisticated to simplify the process of tracking product lots, allowing for greater visibility.
- Improved tracking and inventory control – by scanning barcodes at each stage of manufacturing and distribution, supply chain managers can more easily trace the flow of goods and manage product inventory.
The author proposes that opportunities for further barcode advancements could come from wearable technology and augmented reality. It’s hard to say exactly what the future holds, but with all the recent emphasis placed on “big data” and the need for total transparency, implementing cutting edge barcode technology will definitely be a factor for supply chain competitiveness.
Check out the full article in the link below:
3 Ways High Tech Barcode Scanning Can Transform Supply Chain Efficiency – Tom Setzer, Manufacturing Net
We’re constantly scanning the web for top manufacturing stories and news. But if you’d like to submit an article for consideration for our weekly Best in Manufacturing, send us a message and let us know.
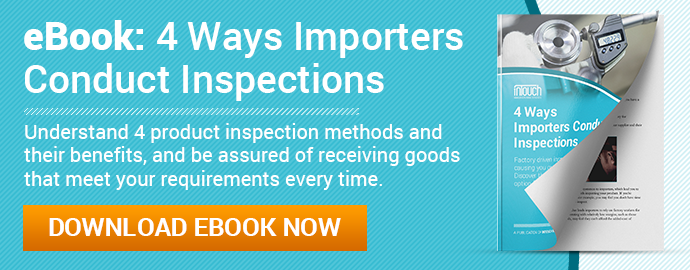