How important is it to clearly address on-site product tests during QC inspection?
After a string of deaths involving a chest of drawers made by IKEA, the Swedish retailer announced earlier this month it would pay a settlement of $50 million to victims’ families. At least three children were killed when the chest of the drawers fell on top of them, crushing them underneath.
Though tragic, this example serves as a lesson to importers about the importance of testing products during inspection. By load testing the chests of drawers, Ikea likely would have found the safety hazard and been able to address it properly before shipping their product.
Product testing is a vital part of almost any QC inspection. These tests simulate the conditions that the product may undergo at the hands of the end-consumer. On-site product tests can inform you about any potential safety hazards, functional issues, poor durability, substandard parts & materials and more.
But many importers and QC professionals simply don’t know how to clearly state their testing requirements so that inspectors understand the procedure and how to report results. So let’s look at all you need to know about properly addressing on-site testing in your most important quality control document—the QC checklist (related: 5 Essentials of a Quality Control Checklist [eBook]).
Equipment needed for product tests
Probably the most critical factor in performing on-site tests accurately and effectively is having the proper testing equipment available. Without it, on-site tests are hard to perform effectively—if at all—and the inspector can’t deliver accurate and reliable results to the importer. Any effective quality control checklist should include a section for on-site testing that addresses equipment and which party will provide it.
Who should provide the equipment needed for testing your product?
Most third-party inspection companies provide their inspectors with a set of tools. And it’s common for inspectors in the same company to carry different equipment, depending on each individual’s product area of expertise. Sometimes the responsibility to bring the required tools to the inspection site falls on the inspector. Other times the factory is expected to provide the necessary equipment for testing.
There are a few factors that generally determine who should provide certain equipment for testing:
- Applicability – depending on how relevant equipment is to a product, the factory is likely to have it available, since they’ll likely need it for their own internal testing. An inspector may also carry equipment that applies to various product types.
- Portability – inspectors are more likely to carry equipment that’s relatively small and easy to transport.
- Cost – an inspector isn’t likely to purchase expensive equipment for testing, especially if they won’t need it regularly. Factory managers are more likely to invest in costly testing equipment if they’ll use it for many production runs.
An inspector should always have a barcode scanner on hand, as it’s small in size, affordable and applicable to almost any type of product. But you shouldn’t expect an inspector to carry a heavy scale or metal detector to every inspection, even though they’re also used to check a variety of goods.
How can you ensure the right testing equipment is available?
Many importers mistakenly assume that either their inspector or their supplier has everything they need for product testing (related: 3 Mistakes Importers Make with Quality Control Checklists). Often the result is that neither party has what’s needed and inspection has to be rescheduled. This can cause shipping delays and can cost you additional inspection fees if hiring a third-party inspector.
Contact your supplier and QC team prior to inspection to confirm whether either will have the required equipment. If a piece of equipment isn’t provided by the factory and isn’t normally carried by the inspector, you may need to purchase the tool and lend it to the supplier during inspections.
Once you’ve confirmed the equipment and who will provide it, state this clearly in your QC checklist and provide it to both your supplier and inspector. This helps you avoid a situation where factory or inspection staff claim they didn’t know they needed to provide the testing equipment.
The sample size for product testing
After clarifying which equipment is necessary and who will provide it, the next point to include in your QC checklist is the testing sample size. The testing sample size is the number of units your inspector randomly pulls from mass production for testing. Importers and QC professionals generally rely on the industry standard known as acceptable quality limits (AQL) to determine the sample size for both testing and visual inspection.
Be sure to state the sample size for each test when you list any required on-site testing in your quality control checklist. This will help you avoid the consequences of inspection staff testing the wrong number of units.
Excessive sampling for product testing
On-site tests generally don’t require a large sample size because the variable being tested usually doesn’t differ significantly from unit to unit. For example, let’s say three out of 100 cast iron pots are tested for oven safety. If all three units pass, chances are the remaining pots in the same order are all made from the same material and will also pass oven safety testing.
It’s not only redundant when inspectors conduct on-site testing on more units than necessary, it can also be expensive. Product testing takes time, especially when limited equipment is available and units need to be tested one at a time. And testing often extends the length of inspection with each added unit tested. This can cost you more when you’ve hired an inspector that’s billing you for their time.
Inadequate sampling for product testing
Just as it’s important for QC staff not to pull too many units for product testing, you may have a major problem if they pull too few. There are some products, like consumer electronics, that warrant certain on-site tests for a larger sample of the order.
If inspectors only test the touch screens of 10 percent of the tablet PCs in an order, for example, you have relatively little assurance that the remaining 90 percent have working touch screens. This can lead to serious quality defects ending up in the shipment you receive.
Your product testing requirements
Importers often have their own tolerances for particular quality issues. Likewise, you may have your own definition of what should be considered “pass” and “fail” and related criteria for product testing (related: Is Your Supplier’s Quality Manual Missing Your Product Requirements?).
That’s why including your criteria and tolerances for the tests you need performed can make or break the accuracy of inspection results. Testing results aren’t nearly as valuable without clear guidelines of what constitutes passing or failing.
Some tests are easier to interpret than others. For example, say you’re importing Bluetooth headsets from China. You’ve included testing Bluetooth connectivity in your QC checklist as a requirement during inspection. It’s safe to say that a unit that can’t connect to a Bluetooth-enabled device should fail this test. But it’s still important to mention your criteria for this testing in your checklist so your expectation is clear.
Where clear testing requirements matter most
While some tests may be fairly straightforward, others are more open to interpretation. And you risk receiving inaccurate test results by not clarifying testing requirements in your checklist.
You might have to arrange for a re-inspection if you need assurance that your shelves can bear 20 kilograms. Or you might ship the order of shelves without realizing they were only tested to hold 15 kilograms. This could result in product returns from customers complaining that shelves are breaking under lighter loads than expected.
Had your inspector known to test the shelves with the proper weight, you’d have an accurate test result and could address any product issues with your supplier before shipping. This example highlights why the effectiveness of an on-site test depends on knowing the standard. Vague, poorly-communicated requirements—or missing requirements altogether—lead to uncertainty when testing and using your product.
Conclusion
On-site testing is one of the most effective parts of inspection to help importers understand the quality of their products. But to get reliable results, it’s crucial to ensure that required testing equipment, sample size and procedure are all clearly understood by the person conducting each test.
Your quality control checklist is the best place to make these requirements clear. And including these important points will transform your checklist into a powerful tool to prevent undetected product issues and protect your brand.
And don't forget to check out the manufacturing podcast episode that covers this topic!
Do you have other tips or advice for how to address on-site testing in a QC checklist? Share them in the comments below!
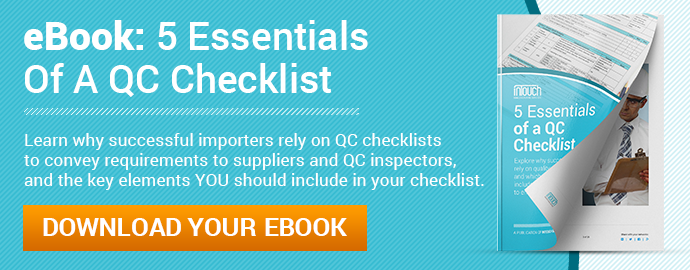