Have you ever given lots of relevant product information to QC inspection staff and your supplier only to find problems later that should have been prevented?
Quality defects, dimensions out of tolerance, failure to conduct important product tests during inspection and inaccurate reporting are just some of the problems you might to encounter as an importer.
An effective quality control checklist can go a long way in helping you prevent these and other issues. QC checklists eliminate ambiguity by providing clear, black and white standards for your product. And by collaborating with your supplier and any inspection staff that will be checking the goods before shipping, you can ensure everyone fully understands your requirements. But importers often take unnecessary risks by making mistakes with their checklist.
What can go wrong when mistakes are made with your quality control checklist?
Let’s say you import mobile phones from a factory in China. You know that QC staff need to test battery capacity, but you assume they already know that. You also want inspectors to report any cases of loose screens as “major” defects, but you leave that out of your checklist. The result could be that the mobile phones you receive have more loose screens than acceptable and a low battery capacity—all because your supplier and any QC staff checking the goods weren’t aware of your requirements.
Common mistakes with QC checklists
Problems caused by ineffective QC checklists usually stem from assumptions made by either the importer, the supplier or staff inspecting the product. Let’s look at the most common mistakes importers make with quality control checklists and see how importers can avoid them.
1. Assuming QC staff and your supplier are aware of all “known quality issues”
Some importers assume that inspectors and factory staff always know about every issue with their products. But your standards may not align perfectly with your supplier's quality manual. And a defect you deem unacceptable might normally be tolerated by the factory and the staff inspecting the product.
Quality issues unique to the product
Professionals who routinely work with products in your industry are normally familiar with what to identify as a flaw. But sometimes there are defects which are specific to your product—particularly if production for that product is relatively less standardized.
For example, metal sinks manufactured from a mold are typically produced with very little variance between units. Whereas an acrylic sink probably involves more handling and manual workmanship, like sanding down rough surfaces, during production. The latter leaves more room for unique defects. And experience with similar products won’t necessarily help an inspector spot issues related to corner radii measurement, flatness and others aspects that are unique to the product.
Unpredictable quality issues
A supplier may be mass producing an item for the first time. Although a golden sample serves as a model for mass production, it’s often hard to know which defects you’re likely to find until the factory’s pre-production or first mass-production run. The golden sample of an item to be mass produced from a mold, for example, is often made by a very different process than the sample itself. So you’re likely to find quality issues later that you can’t initially predict.
How to avoid making assumptions about which issues are “known”
Clearly, it’s not always possible to list every single defect from the outset. That’s why it’s best to consider your QC checklist a “live document”—a document that’ll likely see multiple revisions as production and inspection occur. Rather than
assuming that QC staff or your supplier are familiar with all common defects you know can affect your product, include them directly in your checklist.
If you’ve hired your own QC staff to inspect, tell them to report, aside from known quality issues, anything they suspect could be a problem as a “PENDING” issue. Then you can discuss with your supplier and decide whether the finding is important enough to add on your QC checklist so that inspectors continue to look for it in the future.
By clearly stating and constantly updating known product issues in your checklist, you can avoid the consequences that follow making assumptions.
2. Omitting defect classification or tolerance
It’s usually much easier for importers to interpret an inspection report when QC staff classify defects clearly according to the importer’s standards. The way defects are classified is often a key determinant of whether an order of goods passes or fails inspection. Quality defects are typically categorized in one of three ways during QC inspection for a product:
- Critical
- Major
- Minor
These distinctions are essential. And importers often make the mistake of omitting their tolerance for specific defects and how to classify each from their QC checklist. The result is often that the importer, their supplier and their QC team each have a different understanding of which product defects are acceptable and in what quantities.
Let’s say you manufacture high-end, lounge seating in China. Your customers are 5-star hotels and have very high standards for the appearance of the product. You consider any poor stitching or wear in the leather upholstery found to be a “major” defect that will result in a product return.
Without stating in your checklist that these defects should be treated as major, factory workers and QC staff may consider them minor. This influences the reporting, as QC staff are too lenient when identifying and documenting the defects (related: How Product Inspectors Use Quality Control Checklists). And since the supplier thinks issues are minor, they’re more likely to ship the product with an unacceptable number of units that have poor stitching or worn leather.
How classifying defects helps you avoid problems
You can help ensure that factory staff and QC professionals know how to treat and report defects by classifying their severity in your QC checklist. This informs the factory’s QC team and any outside inspection staff so they can catch and report any defects properly before they affect the finished goods. In turn, you can be more confident in the results of product inspection.
It’s also important that you and your supplier agree on the standards for defects included in your checklist. Quality is built into a product. And you’ll typically receive better products with fewer delays and repairs needed if your supplier knows your tolerance for quality defects before beginning production.
3. Failing to include any on-site product tests you require
Some importers are familiar enough with the QC side of their product to know which tests should be conducted on-site during inspection. Others may not even know that testing is a standard practice during inspection. An experienced QC professional can often help you decide which tests should be conducted based on your product type. But whatever tests you determine to be relevant, it’s important to include the following information in your checklist:
- What on-site product tests are required during QC inspection
- What equipment, if any, is needed for testing; and
- Who’s responsible for providing the necessary testing equipment
As with most parts of a quality control checklist, if you don’t specify on-site testing, QC staff aren’t likely to address it, and your supplier isn’t likely to expect it. For example, real-world function testing is fairly common during QC inspection for household appliances, like electric juicers. But if you don’t inform your QC team that you want them to conduct this test, there’s no guarantee they will.
If you want inspectors to report fabric density precisely, they’ll need special equipment to cut and weigh fabric and measure GSM (grams per inch). Without seeing this requirement in your checklist, inspectors may make a less accurate estimation of fabric density. And sometimes the factory provides the necessary testing equipment, while other times the inspector is responsible for bringing it to the inspection site. Omitting this detail from your checklist can lead to an inability to perform the test.
How to address on-site testing in your checklist
The best time to specify which tests are required is when you’re creating your QC checklist. Professional checklists tend to have a section dedicated to on-site testing. Start by communicating with your QC team about which tests are necessary. Then find out whether factory workers or the QC team already have the equipment needed for testing. You may need to purchase any equipment necessary and provide it to the inspection team.
Once you’ve settled all requirements related to testing, include detailed information in your checklist and get feedback from your supplier and QC team. This last step ensures all parties understand what’s expected.
Sometimes importers want to see certain tests performed during inspection, such as a carton drop test. But when inspectors arrive at the factory, management there refuses to allow the test. You can avoid unwanted surprises like these by clearly outlining testing in your checklist beforehand.
Conclusion
Having a QC checklist at all is a step in the right direction toward better order quality. But the mistakes mentioned above can hamper the effectiveness of your checklist and leave you wondering why it didn’t serve you better in preventing problems.
By avoiding these common mistakes that importers make when creating a QC checklist, you can sleep more soundly knowing that you’ve provided your supplier and inspectors a clear, undisputed and truly useful document. And the more clarity you bring to your checklist, the better your odds will be of avoiding the problems keeping your customers happy.
And don't forget to check out the manufacturing podcast episode that covers this topic!
What other mistakes have you seen importers make when creating a QC checklist? Share your experiences in the comments below!
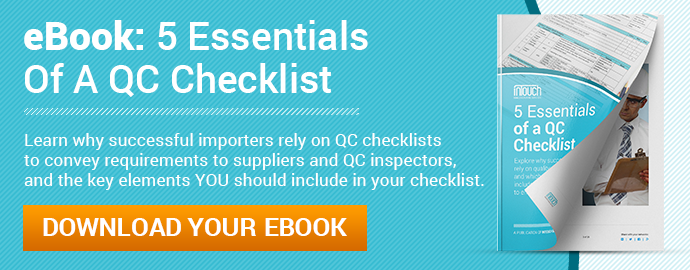