Imagine an importer of promotional baseball caps ordering a shipment from China. Pre-shipment inspection finds that factory workers used the wrong color thread when embroidering the logo on the product. Knowing their customer won’t accept this quality issue, the importer has little choice but to scrap the finished units and ask the supplier to begin production again from scratch.
What could this importer have done differently to prevent the thread color mismatch and other product defects?
They made a couple avoidable mistakes here. First, they failed to specify the appropriate thread color for the logo among their product requirements. And they didn’t request a product sample from the factory for review and approval before mass production. Both steps would have revealed the quality issue before it affected mass production (related: How Experienced Importers Limit Defects in Three Stages [eBook]). Let’s take a closer look at approved samples and their role in minimizing quality defects.
How approved product samples help you minimize product defects
Approved samples are so effective at reducing product defects because they serve as a standard by which mass-produced units are later evaluated. Factory design and engineering staff typically create product samples before mass production of an order starts. These samples typically closely represent the supplier’s understanding of what the buyer wants. The supplier then sends the samples to the buyer to verify a number of qualities, such as:
- Parts and materials used
- Adherence to product specifications
- Proper functionality, and
- Any complementary designs, branding and artwork for their product
Once the buyer is satisfied with a particular sample, that sample becomes the approved sample, or “golden” sample. The buyer sends this sample back to their supplier and authorizes mass production.
As the buyer, approving product samples gives you the chance to clarify every aspect of your product to prevent quality defects before production begins. If factory staff notice problems during production, they can then proactively take corrective action to address them. It’s also easier to hold your supplier accountable for unacceptable defects and other quality issues when factory staff have a golden sample to use as a model. Likewise, any QC staff conducting pre-shipment inspection can refer to your sample as a model for checking your product.
How to obtain a golden sample from your supplier
It’s very common for importers to ask their supplier to send them product samples before production. So don’t hesitate to ask your suppliers to provide a golden sample for you to review. Most suppliers are familiar with this process and willing to provide a sample, typically for a small fee. Your supplier may waive the product sample fee if you have a strong relationship or regularly purchase from them. Suppliers will often refund the sample fee to the buyer once the buyer has placed an order.
Because a factory creates the product sample before mass production, a detailed PO, QC checklist and any other product specifications should always supplement your golden sample. Each document works together throughout the manufacturing process to minimize your risk of finding unacceptable product defects in your finished goods. And if you fail to develop specific product requirements before requesting a sample, you might have revise the sample several times before achieving a suitable, golden sample.
Should you request a golden sample before or after selecting a supplier?
Some importers choose to request product samples from multiple suppliers as part of the vetting process before deciding on a particular supplier to work with. The quality of the samples can help you discern which supplier is able to meet your expectations. Product samples are also meant to give you an idea of the supplier’s quality capabilities, which can help you when proposing a target price during negotiation.
Other importers wait until after settling on a supplier before requesting a product sample to review and approve. You might not need a golden sample to decide on a supplier if you’re already comfortable with the proposed production capabilities and price. Regardless of when you request a product sample, make sure you’re setting quality standards early when negotiating with suppliers to minimize product defects.
Reviewing a golden sample for quality issues
After your factory has provided you with a sample, you’ll want to review it for any potential quality issues. For simple products, you may just need to review the sample’s dimensions, color and visual properties to verify it meets your specifications. Importers sometimes hire a local third-party inspector to review the sample on their behalf to save time on shipping. But for more complicated products, it may be necessary to send your golden sample to a certified laboratory for testing.
Factors to consider for testing a product sample in a lab
Professional third-party labs often perform testing to assess a product’s safety, performance, function and other properties. Some importers consider lab testing to be a vital part of reviewing a product sample before authorizing mass production. Others find testing to be a needless additional cost for them. Your decision to send a sample to a lab for testing will typically depend mostly on the following factors:
Your product’s intended use and attributes
Certain importers require lab testing to verify their product will work safely as intended. A common example is food items or products that make contact with food when used. Safety and function testing in a lab is often an essential step in quality control of medical devices as well. And many cosmetics importers send their product samples to a lab to ensure they’re safe for contact with human skin, eyes and mouth.
For a handful of products, material composition and purity are important in determining a product’s value. Jewelry manufacturers, for instance, often insist on lab testing to ensure the quality of precious stones and metals used in their products. And for textile manufacturers, material composition testing of fabric can help reveal quality issues that might otherwise have gone unnoticed.
Claims made in marketing your product
Have you made any claims about your product’s performance and quality in marketing your product? You’ll likely want to test certain aspects of your product’s performance to ensure it lives up to these standards. Is your set of porcelain dinnerware supposed to be dishwasher safe? What’s the rated temperature of your oven mitts? These are the sort of claims you’ll probably want to test before confidently promising them to your end-customers.
Another consideration is how your product stacks up against similar products. If you’ve claimed your product performs better than your competitors’, you might want to conduct comparison testing, or benchmarking. One common example is power tools. Manufacturers of electric drills often compare their product’s reliability and power with competing drills. Lab testing can compare how your product’s performance, materials, features, quality and durability stand up to your competitors’ products.
Regulations governing the product type in your market of sale
For some products, lab testing can help you verify whether your product complies with government regulations in your target market. For example, if you’re manufacturing cookware for customers in the United States, the coating of cookware that comes in contact with food products must meet certain standards.
And generally, if your product has the potential to cause serious harm to the end-consumer, there are safety regulations governing that product. This includes children’s toys and products with lithium-ion batteries, among others. Depending on the product’s intended market, there might also be different relevant tests based on the regulations of that country or region.
Aside from these factors, you’ll also want to consider your budget when determining whether to send product samples to a lab for testing. Depending on the testing, it may not be worth the added time and expense. Still, if you want to verify particular safety, performance or function aspects of your product that only a qualified lab can test, it may be worth the investment.
How to handle golden samples properly to reduce your risk of quality defects
After you’ve obtained and reviewed your golden sample for mass production, there are some steps you should take to ensure factory staff and any QC inspectors handle your golden sample appropriately (related: 3 Must-Do Procedures for Handling Golden Samples for Manufacturing).
Factories might have multiple product samples lying around the production floor that you may or may not have approved. Workers or QC staff could easily mistake one of these for your golden sample, if the sample isn’t properly handled. And factory workers might tamper with your approved sample to try to mislead any outside inspectors about your product specifications. This is a common risk with suppliers that have outsourced your sample or order to a sub-supplier or otherwise haven’t met your quality standards.
There are a few steps you can take to minimize mishandling of your approved sample:
- Establish two identical approved samples: One sample is for the factory to use as a guide during the production process and for the factory's internal QC inspections. The other sample is for any outside QC team’s reference during inspection, in case the factory’s sample is missing or altered.
- Sign and date your samples: This verifies the authenticity of the sample and allows the factory and QC staff to keep track of your latest specifications in the case of multiple revisions over time.
- Seal each sample in its own carton for shipping: Sealing samples helps prevent tampering by making it easy to tell if anyone has opened the sample before your own QC staff have.
Send the approved sample back to the factory, allowing enough time before mass production to address any potential misunderstandings with your expectations. If you’ll be sending outside inspectors to the factory to check your product, ensure they receive it at least 1-2 working days before the expected inspection date. More time is recommended for more complicated products.
Advise your factory and QC team when sending the sample, noting a description of the number of samples, the courier name and tracking number. When sending samples by post, it’s also helpful to label the package with “PRODUCT SAMPLE – NO COMMERICAL VALUE”. This helps prevent the risk of customs agents stopping the samples at the port of destination. If your sample is delayed at customs, you’ll need this information to retrieve what you shipped.
Conclusion
Establishing a golden sample is an efficient way to prevent quality defects before mass production begins. As an importer, you can personally hold and examine the product a factory is capable of producing by obtaining a golden sample. With the sample available, the factory staff will have a clear standard to follow to ensure production complies with your specifications. And QC inspectors will be able to catch any defects and nonconformances compared to your approved samples during product inspection.
Remember that a golden sample isn’t always indicative of final, mass-produced quality, but rather ideal quality. With a multitude of factories around Asia, each factory naturally has different standards for production. Don’t cause yourself unnecessary headaches by assuming up front that the factory understands your product requirements and that it will always produce your golden sample.
Setting clear standards with a golden sample before mass production will help you avoid delays and the costs of trying to address product defects during or after production. And while providing a golden sample can’t always guarantee perfect products, it can help prevent careless errors and set you down the path of satisfactory quality.
When have approved samples saved your product from defects and other quality issues? Share your experience in the comments section below!
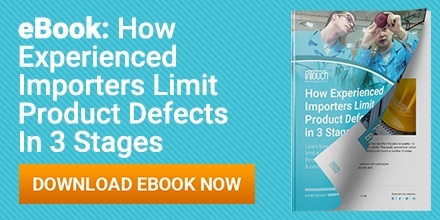