Mistakes in manufacturing can lead to problems ranging from minor quality defects and customer returns, to serious product malfunctions, consumer hazards, expensive recalls and even lawsuits. And if you’re an experienced importer, you’re likely aware of these potential problems and how clarifying your requirements with suppliers helps you prevent them.
But did you know that an effective quality control checklist is one of your best tools to help avoid errors in the manufacturing process?
A QC checklist is basically a written guide outlining requirements for a product, its packaging, inspection method and more (related: 5 Essentials of a QC Checklist [eBook]). The factory workers handling your product and any QC staff inspecting it use this guide as a reference to understand your expectations. An effective checklist is:
- Comprehensive enough to convey all your product standards,
- Practical enough for inspectors to use in a factory setting and
- Clear enough that you, your suppliers and any product inspectors all have the same understanding
In short, checklists help eliminate potential unanswered questions looming about your product. Factory staff use them to produce your goods to your specifications. And inspectors use them to check that your standards are met.
Let’s look more closely at what a difference a quality control checklist can make in your manufacturing experience.
What can go wrong without a quality control checklist?
Many importers mistakenly assume that, simply by explaining their requirements once over the phone or by email, their suppliers or inspectors will fully understand their requirements. But without the clarity that of a detailed QC checklist, problems can arise that limit your suppliers’ ability to manufacture your product and any inspectors’ ability to check the product (related: 3 Mistakes Importers Make with Quality Control Checklists).
Products that don’t meet customer requirements
Let’s say you supply garments to several major retailers, including Walmart. Walmart expects you to meet specific packaging requirements for their stores. Similarly, you must also meet the unique requirements of other retailers when distributing in their stores. And then there are particular legal requirements for clothing labeling, which can vary depending on the market of sale.
Without a detailed checklist that shows these requirements, you could end up with customers rejecting entire shipments of goods that don’t adhere to requirements. You may also be subject to government fines or chargebacks from customers when products don’t meet certain standards.
Unreliable inspection results
In another example, consider manufacturing furniture in China. You have concerns about your dining room chairs toppling or breaking during normal use. You might want inspection staff to conduct load testing, among other product tests, to address this concern.
But without including this in your checklist, there’s a strong chance that either inspectors won’t conduct load testing or will use the wrong testing standard. The result is that you may need to repeat inspection or else risk receiving faulty furniture.
Production or shipping delays
Both examples above show cases where production or shipping delays are likely to occur. Even small issues with your order may require product rework. And this, along with any follow up inspection to verify rework, can lead to delays, a fairly common problem among both new and experienced importers. Delays often happen because of the need to correct mistakes that could have been prevented by having a clear QC checklist.
How you benefit from using a QC checklist
You stand to benefit a lot from taking the time to develop a clear quality control checklist. Details are sometimes lost in translation or forgotten altogether. But a checklist combining your requirements with any feedback from your supplier and QC team will help protect you against costly errors and misunderstandings during the production and inspection process.
Getting the product right the first time
Some product issues are easy to mend, like removing flash from an injected-molded part. Other issues may require the factory to start production again from scratch. For example, your supplier might produce ceramic cups that don’t meet requirements for size and artwork. These aren’t problems that the workers can easily correct. And the factory would likely need to produce an entirely new order of cups to fill your order.
You can prevent this kind of scenario and the delays likely to follow by providing your supplier with a QC checklist upfront. When your supplier has all the information they need before beginning mass production errors due to misunderstandings are prevented before they occur.
Holding suppliers and inspection staff accountable for meeting requirements
With clearer expectations comes greater accountability. And when your supplier and inspection staff understand your expectations, it’s easier to hold them accountable for any mistakes. Many importers see this shown in their requirements for workmanship and the quality of parts & materials used in their product. When you’ve outlined these requirements for your supplier in a way that’s black and white, it’s harder for them to defer responsibility by claiming they weren’t aware.
The same is true for any QC staff you’ve hired to inspect the product before it ships. Whether you have full-time inspectors or third-party inspectors, you’ll want to be confident they’re checking the product as thoroughly as or better than you would if you were conducting inspection yourself. Clearly defined inspection criteria shown in your checklists help ensure nothing is missed.
Improving your understanding of your product
Let’s face it. Not every importer is an expert in the all the production and quality control aspects of their product. You
may be experienced in selling your customers the speaker systems they love but less familiar with specific quality issues to look for during pre-shipment inspection. That’s why importers often find that using a QC checklist helps them gain a fuller understanding of their own product.
Many third-party quality control companies have their own QC checklists to help with inspection. But many importers find it extremely helpful to develop one not only for others to reference, but for personal use as well.
The process of writing and continually updating the checklist forces importers to consider every aspect of their product that’s important to their customers.
Improving the relationship between you and your suppliers
It may seem that suppliers don’t like their customers to dictate a long list of requirements to them. But having an effective QC checklist in place actually tends to improve the relationship between the supplier and the importer.
The key to making this work well is collaborating on developing the checklist—consulting your supplier on what’s reasonable and agreeing on product requirements before production. This shows the supplier that you value their input and want to reach an agreement so that you avoid misunderstandings later (related: 4 People to Consult When Creating a Quality Manual for Your Product).
How to develop a quality control checklist
So how do you create a QC checklist? Depending on your own expertise and the complexity of your product, creating a QC checklist can be more or less of a challenge.
While many third-party inspection companies have their own checklists for various types of products, your checklist should be customized to fit your product. Two different mobile phones may have some of the same requirements for battery capacity, for example. But other product components, packaging and branding are likely very different between the two.
The importance of feedback from those involved
The best checklists come from thoughtful collaboration between the importer, supplier and QC staff. By directly involving factory management and staff in developing standards, they’re more likely to feel invested in your orders and take a greater interest in meeting your requirements. Consulting factory management also helps you get a more complete understanding of the production processes involved, which can help you prevent delays and quality problems.
It’s also important to consider the perspective of the people that actually inspect your goods when creating your checklist. When inspectors visit your supplier’s factory, they need to know precisely how to check your product, what product tests you require and more.
An experienced inspector may have already checked many products very similar to yours. But they may not know your unique methods, criteria or tolerance for specific defects.
Most effective QC checklists contain the following information:
- Product requirements;
- Packaging requirements;
- On-site product tests & checks;
- Defect classification; and
- Feedback from key people involved in production and QC
It may also be helpful to create a version of the checklist that’s written in your supplier and inspector’s native language.
Conclusion
A detailed quality control checklist is important because it conveys requirements and standards to suppliers and quality control providers. Checklists help importers ensure their expectations are understood and that QC staff are holding their product to the right standard. Without them, inspectors and factories are often left guessing what is and isn’t acceptable.
It may seem like just a reference material, but when done correctly, a QC checklist can mean the difference between success and failure for an importer. Creating a checklist can be a challenge and often requires continual updating. But it continues to play a vital role in managing product quality across the manufacturing industry.
And don't forget to check out the manufacturing podcast episode that covers this topic!
How has a QC checklist improved your manufacturing experience? Share in the comments below!
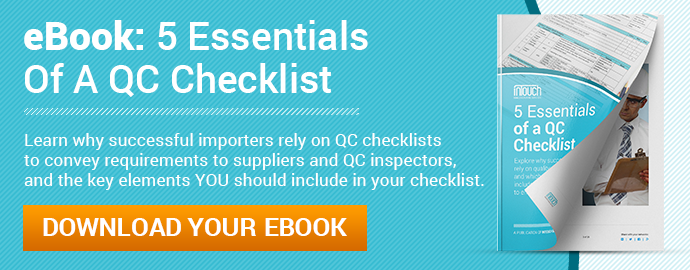