If you’re like most importers, you’re had the experience of feeling inundated with pressing questions, such as: Which supplier should you work with? How much should you spend on parts & materials for your product? And how soon will your customers receive the finished goods?
All of these are potentially difficult questions that each importer must answer for themselves. But one question you should never have to face is how best to detect product defects early so you can address them before they harm your bottom line. The answer is simple: quality control inspection.
Only by inspecting your shipment of goods before it leaves your supplier’s factory can you identify and address any quality issues before it’s too late. Managing product quality with QC inspection lowers your risk of product returns, unhappy customers and many other costly and avoidable problems (related: How Experienced Importers Limit Product Defects in 3 Stages [eBook]).
Let’s discover what value inspection offers at various times to determine when it’s best for you.
Where quality control inspections offer value at different production stages
Every inspection type aims to detect any product defects or other issues before the factory ships the finished goods. But QC inspection provides different insight into your product when performed at different points in production. The greatest value in finding problems early is being able to address them with your supplier before it becomes difficult or expensive to do so, such as after you or your customers have received the shipment.
Importers commonly perform product inspection at various stages of production or shipping, including:
- Checking raw materials or components prior to production
- Inspecting semi-finished products and finished products during production
- Inspecting finished products (with or without packaging) after production
- Monitoring the loading of shipping containers
You might find inspection is only necessary for your specific concerns at one or two key production stages. Or you may feel you need inspection throughout production to adequately oversee quality (related: 3 Reasons to Conduct Production Monitoring). You’ll need to strike a balance between the cost and time needed for inspection and your appetite for quality risk.
By understanding the benefits of inspecting at each stage, you can determine which is best for your situation and ensure you’re not missing opportunities to catch product defects in your order early.
Incoming quality control (IQC)
Inspecting parts and materials chosen for a product, a process called incoming quality control (IQC), is an important first step in identifying any quality problems. Importers typically leave IQC to their supplier’s own staff to perform, rather than visiting the factory themselves or hiring a third-party QC inspector for this purpose. If you’ve bargained your order price too low when negotiating with suppliers, don’t be surprised if factories attempt to recoup lost margin on your order by using cheaper, substandard materials or parts.
It’s difficult for a factory to manufacture a product that meets your quality standards using materials that don’t. And suppliers normally buy materials in bulk for use throughout manufacturing your product and any others like it. So any quality issues related to raw materials will usually affect most or all of an order. IQC helps ensure raw materials and components conform to your specifications before the factory begins mass production.
IQC processes may also include ensuring the proper storage of raw materials in the factory’s warehouse. Inspecting storage conditions can be particularly important for importers of wood products, for example, where closely monitoring relative humidity of both storage and production areas can help prevent wood warping.
Should you insist on outside IQC for your products?
Any decent supplier will normally perform incoming quality control on their own. But your choice to rely on your suppliers’ staff for these checks should depend a great deal on the strength of your relationship and any prior experience working with them. Arranging IQC on your own can be especially helpful if:
- You’re working with a supplier for the first time and don’t know what quality to expect
- You need to verify rare or expensive materials or components for your order, or
- You’ve had issues with the raw materials in prior shipments you’ve received from this supplier
As an importer, only you know what’s best for your product. So if you suspect your supplier’s IQC is insufficient, you might benefit from proactively arranging IQC by your own QC staff or a professional third party to detect any quality issues before production.
First article inspection (FAI)
For some importers, the next prudent step in identifying product defects after IQC is checking some of the first mass-produced units. During first article inspection (FAI), an inspector will check one or a few of the first units of an order off the production line, or a unit from the first production lot.
Reviewing a golden sample is similar to FAI in that it aims to establish a quality standard for production. But the insight gained from FAI will typically vary greatly from that obtained by reviewing a pre-production sample.
Golden samples are usually custom made by an R&D team, often using different processes than those of mass production. For instance, your factory might manufacture a working prototype or sample for a plastic-molded component using 3D printing or a temporary mold. Since these methods likely differ from those the factory will use on the production line, there’s no guarantee the sample accurately represents the quality of mass production.
FAI offers you a more reliable look at the quality of goods you’ll ultimately receive because it looks at those initial units from mass production. FAI also helps you spot any issues apparent from the start of mass production so you can resolve them with your supplier early.
Would you benefit from using first article inspection to detect product defects?
First article inspection is somewhat more common among military subcontractors, but it also has a place among civilian sectors. For example, FAI is a common practice among manufacturers of automotive parts, medical devices and aerospace equipment. You might want to consider FAI if:
- Your product contains expensive components that are difficult to repair or rework in the event of quality problems, or
- Your product has very strict tolerances (e.g. dimensions) that depend on precise calibration of tools and equipment used in production
First article inspection probably isn’t necessary if you’re manufacturing low-cost consumer goods. So long as you’ve clearly outlined your product requirements, you can still address any product defects later in production.
In-process quality control (IPQC) and during production inspection (DUPRO)
The next logical stage to consider quality control inspection after FAI is when production is well underway. The two types of inspections commonly performed here are in-process quality control (IPQC) and during production inspection (DUPRO). The difference between these is that inspectors generally perform IPQC on semi-finished goods, while they conduct DUPRO on finished goods. DUPRO typically occurs when the factory has manufactured 15-80 percent of the total order quantity.
IPQC and DUPRO inspections are highly underrated tools for improving product quality. Both similarly help importers identify product defects and other issues that have arisen during production before they potentially affect their entire order.
Should you include DUPRO inspection in your QC budget?
Between DUPRO and IPQC, DUPRO is the more common option among importers and is second in popularity only to final inspection. Investing in DUPRO inspection may be worthwhile for you if:
- You’re struggling to manage product quality and meet shipping deadlines with final inspection alone
- You’ve seen quality defects or other issues in final inspection that were clearly introduced during earlier production processes, or
- You’re manufacturing a relatively complicated product that requires many different components and production processes
Final inspection helps you catch any problems before your shipment leaves the factory. But by the time final inspection occurs, it may be too late to catch and mitigate any issues introduced earlier. If you’re able to identify quality defects during IPQC or DUPRO, the factory can stop production and address these before they affect the whole lot. This also has the added benefit of preventing production or shipping delays.
Final inspection
The most common time importers choose to perform quality control inspection is when most of the goods are finished—typically 80 percent or more. Usually called final inspection, this represents your last opportunity to see the quality and condition of your shipment while it’s still in the factory. Many experienced importers and QC professionals consider final inspection to be the bare minimum required level of product oversight.
Like DUPRO and some other earlier inspections, QC staff typically use AQL sampling or an alternative sampling method for final inspection. But final inspection typically offers a look at a more representative sample than inspections conducted earlier because more of the units will be finished.
And unlike other QC inspection types, final inspection provides the opportunity to verify packaging materials and methods. Inspectors can check requirements such as artwork, barcodes, carton markings, packing assortment and others. When it comes to outside inspection, factories often prefer to pack just a few cartons of the order ahead of inspection, while leaving the remaining units unpacked for easier inspection. This gives you a chance to verify packaging requirements without factory workers having to repack every carton that inspectors have opened.
Is final inspection a vital step for you in identifying product defects?
Do you care whether your product conforms to your customers’ specifications and quality standards? If you’re like most importers, your answer is a resounding “YES”. By extension, final inspection is a vital step in helping you manage the quality of your products by identifying any product defects before it’s too late to address them efficiently.
You may be importing wicker patio furniture, high-end women’s footwear or promotional keychains. But regardless of your product type, checking your product before it ships is essential to avoiding quality issues that can lead to product returns, dissatisfied customers and other costly, but preventable, problems.
Monitoring container loading
Some importers require inspection while workers load their goods into a container for shipping. During the process of monitoring container loading, inspectors check the packed cartons and loading method and verify workers have properly sealed the shipping container before transit.
Inspectors might open one or two cartons to check a small sample of product and verify packing method. But most factory managers want to load the containers and get them out of the way as quickly as possible. So it’s not practical to inspect a larger sample as you might with DUPRO or final inspection. The main points of monitoring container loading usually include:
- Checking the internal condition of the container for moisture and other issues
- Monitoring loading by the factory workers and recording quantities of cartons loaded, and
- Verifying the sealing of containers and recording details of the seal placed on the containers
One downside to monitoring container loading is that it’s often difficult to know how long the loading process will take. This will depend on factors such as how many workers will be loading the container and whether the container arrives at the loading site on time. If you’re sending your own or a third-party inspector to monitor the container loading process, they may not be present for the duration if loading is delayed or takes more time than expected.
Is monitoring container loading necessary for you?
Monitoring container loading is an unnecessary additional precaution for most importers. But you may want to budget for the added oversight if:
- You have a strict loading plan or procedure you require the factory to follow
- You require a record of the container and seal as a condition related to a letter of credit, or
- You’re worried that your supplier will ship unacceptable or otherwise defective units with the rest of your order
You may have repeatedly experienced serious quality problems with a particular supplier in the past that you feel warrant monitoring container loading. But most often this would indicate that you should find a better supplier.
Conclusion
When should you inspect your order? Only you can determine the best time for your business based on your unique past experience, product type, deadlines and budget. But now that you have a better understanding of the value of quality control inspection at different stages, you’re in a better position to make an informed decision about which time is best for you.
When implemented successfully, product inspection is an invaluable tool for identifying product defects in your order and improving product quality over time. To schedule QC inspection at any point of the production process, be sure to openly communicate with their supplier and inspection team. With clear communication, you can come to an agreement about the standards and criteria of QC inspection to ensure you’ll get accurate results.
When have you found QC inspection valuable for your managing your product quality? Share your experience in the comments section below!
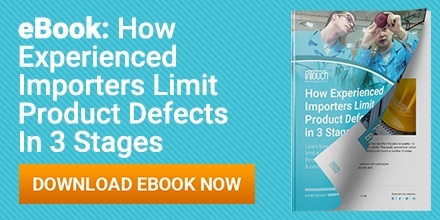