Imagine ordering wooden furniture from a factory overseas, waiting three months for production to finish and then discovering that 25 percent of the goods you receive are misshapen due to warping.
Needless to say, that would create a whole slew of problems and frustrations. But before you take corrective action, you need to know two things:
- Where did the problem happen?
- And how can warped wood be prevented?
Warped wood can be a serious problem for some products, resulting in customer complaints and returns (related: How Experienced Importers Limit Product Defects in 3 Stages [eBook]). Where some products are concerned, such as building materials, cracked or warped wood that affects a structure can be dangerous.
Here you’ll learn about common types of wood warping, potential causes and ways you can prevent warped wood in your own products.
What is wood warping?
Wood warping is deformity in wood occurring when the moisture content of different parts of a piece of wood changes unevenly. When one part of a wooden board dries faster than another, for example, the drier part shrinks faster and causes stress that changes the shape of the wood. So a board that was meant to lie flat now has a bend in it somewhere.
Warping is a product defect that can affect retailers of a wide variety of products, from wooden furniture and wood molding to musical instruments like guitars.
What causes wood warping?
Before exploring the different types of wood warping, it’s important to understand what causes wood to change shape.
If you’re a manufacturer or retailer of wooden products, you may have heard that moisture and humidity levels can impact the shape and integrity of wood. This is because wood is a hygroscopic material, which means it absorbs and releases moisture from its environment. When the moisture content of wood changes unevenly, it causes the wood fibers to expand or contract in different directions, leading to warping.
Understanding equilibrium moisture content
When wood has a relatively high moisture content, it shrinks as it dries until it reaches equilibrium with relative humidity, sometimes called equilibrium moisture content (EMC). Conversely, wood with a relatively low moisture content will swell as it absorbs water from the surrounding air until reaching EMC. This direct relationship helps predict how wood will behave as it adjusts to particular conditions.
Factors that influence the rate of change in moisture content
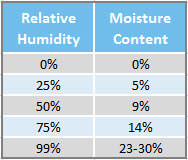
Although all wood will generally reach EMC, the process of adjustment can take hours, days, weeks or months. Factors that affect the time needed for wood to reach EMC include:
- Size of the piece of wood (thicker pieces take longer to lose or absorb moisture)
- Coating (coated wood takes longer)
- Grain orientation (end grain wood takes less time)
- Ambient air temperature (warmer air speeds the process of wood reaching EMC)
Ambient air temperature influences the rate of change in wood moisture content but doesn’t significantly affect EMC.
5 Types of wood warping
Wood can warp in a number of different ways, depending on the cause. Understanding these common ways wood warps will help you diagnose potential problems occurring in production or storage:
1. Bow
When one face of a wooden piece gains or loses moisture unevenly compared to the opposite face, the wood expands or contracts asymmetrically. This causes the board to bend along its length, resulting in a bow.
For example, if one face of a wooden board is exposed to a humid environment while the other face remains relatively dry, the moist side absorbs more moisture and expands, while the dry side retains its original dimensions. As a result, the board bows with the moist side facing outward.
2. Kink
A kink can appear as a sudden deviation or irregularity in the straightness of the wood. It often appears as a sharp angle or twist, causing a localized area to be bent or twisted out of its original plane.
Kinks in wood are usually caused by factors such as uneven drying, moisture imbalances, or internal stresses within the wood. When the wood fibers experience non-uniform changes in moisture content, they expand or contract unevenly, leading to kinks or twists in the wood.
3. Twist/Wind
A twist or wind is a form of warping characterized by a rotational or twisting movement of the wood fibers. When wood twists, the board no longer lies flat. Instead, it acquires a spiral shape.
Twists or winds in wood are typically caused by uneven drying or changes in moisture content along the board's length. When one side of the wood gains or loses moisture at a different rate than the other side, the fibers respond by expanding or contracting unevenly to form a twist.
4. Cup
When wood cups, it means that the edges of the board are higher or lower than the center, resulting in a curved shape resembling the shape of a cup.
This type of wood warp is primarily caused by changes in moisture content across the width of the board. When one face of the wood gains or loses moisture more rapidly or to a greater extent than the opposite face, the wood fibers respond by expanding or contracting unevenly to form a convex or concave shape.
5. Crook
A crook refers to a type of warping where a single edge of a wooden board or plank develops a curvature along its length. It is a form of warping characterized by a bend or curve in the shape of an arc.
A crook can be subtle, with a slight curve, or more pronounced, with a significant bend.
Note that different types of wood warping are not mutually exclusive. Different warping shown in the same piece of wood could be a sign of multiple problems related to moisture content.
Wood Species and Warping
Some species of wood are more stable and less likely to warp or crack than others. The following species are known to be relatively resistant to warping:
- Redwood not only has a comparably straight grain pattern but also a natural chemical inside that protects against moisture infiltration.
- Cedar is among the densest wood species, which helps prevent cracking due to changes in moisture.
- Fir is very stable once its moisture content reaches equilibrium with the relative moisture of the surrounding air. At equilibrium, or when the wood is “seasoned”, fir will undergo very little shrinking or warping.
Ways to Prevent Wood Warping
Several factors affect wood warping, some of which are easier to control than others. Different types of warping also tend to be caused by different factors. So being able to link warp types found to particular causes helps in preventing future warping.
Wood grain and sawing techniques
Grain patterns can influence the way wood behaves as it adjusts moisture content. Wood that’s cut from the heart of the tree is generally more stable against shrinking and warping. Very straight grain with only 1/32 in (about 0.79 mm) between grain lines is less likely to warp, regardless of wood species.
Sawing techniques used in processing the lumber can also influence warping. An understanding of these can help you limit your risk of manufacturing warped wood products. For example, in a quarter-sawn board where growth rings are symmetrical, shrinkage will occur evenly and cup-type warping is far less likely. Then again, a flat-sawn board is less likely to experience crooking because both edges are equidistant from the tree’s core.
Poor saw maintenance and variation in saw speed can result in boards that are thinner on the ends than in the middle, which can cause bow-type warping. It’s also recommended not to saw lumber at an angle to the grain. Sawing so the grain is parallel to the edge of the board can help prevent crooking.
Proper storage techniques to prevent warped wood
The way you stack and store lumber is a major factor for how it will change as it adjusts to EMC. Some best practices for stacking and storage of wood include:
- All boards and the stickers placed between them in a stack should be of uniform thickness, especially when placed in the same layer.
- Stickers should lie flat and be vertically aligned.
- Lumber piles should rest on a flat foundation.
Placing heavy weights on a stacked lumber pile can also be helpful in preventing cupping . The wood also needs proper ventilation, which is best accomplished by spacing the material so all surfaces are exposed to the air.
Store your lumber in a clean, cool, shaded and dry location. If you're storing wood in an area with high relative humidity—80 percent or more—be sure it's wrapped in material that is impermeable to vapor. This prevents the wood from absorbing significant amounts of moisture from the surrounding air. High humidity should be a real consideration for those manufacturing furniture and other wood products in South China and Southeast Asia.
Properly drying or curing wood to prevent warping
Although the process for curing wood doesn’t usually affect crooking, it’s important in limiting other types of wood warping.
Kiln-drying is often used in manufacturing, as it gives the manufacturer more control over drying speed and degree. But all kiln-dried wood will acclimate to relative humidity of its environment. The main advantages of kiln drying over more passive natural drying are that kiln drying stops insect activity and sets the sap in resinous softwoods, which is especially important for wood used as building material.
Experts recommend certain practices for drying wood to prevent warping, such as:
- Don’t allow partially dry lumber to quickly regain moisture
- Don’t dry lumber too slowly (doing so could worsen any bowing and other warping)
- Don’t over dry lumber, which can lead to cracking, splits and end grain checking
Sealing the ends of wood can also help prevent warping caused by uneven drying. Moisture leaves wood ten to fifteen times faster from its ends than through its other surfaces. And without sealing the ends of boards of wood, the ends tend to shrink faster than the rest, leading to undue stress that can cause warping.
MONITORING MOISTURE CONTENT AND CHECKING FOR WARPING DURING INSPECTION
Manufacturers working with wood need to closely monitor both relative humidity of their storage and production areas and moisture content of the wood material. Retailers often rely on locally-based, third-party inspectors to visit these facilities on their behalf. But depending on your situation and relationship with your supplier, you may choose to rely on factory staff or hire your own full-time staff to inspect instead (related: 4 Ways Importers Conduct Product Inspection [eBook]).
Factories that produce wooden products should have accurate hygrometers installed to measure relative humidity in storage and production areas. Inspectors should note the humidity in each relevant area. Keeping a record of these readings helps diagnose the causes of any wood warping found in the product.
Factory workstations should also be equipped with calibrated prong-type moisture meters to measure the moisture content of the wood at various production stages. Prong-type, rather than surface-type, moisture meters should be used because moisture content can vary one to two percent between the wood's interior and outer surface.
How to check for wood warping
Checking for warped wood is a simple procedure:
- Place a board or piece of wood on a flat surface.
- Check along the edge of the wood to confirm its level along the full length.
- If one part or end of the board is raised above the rest, the board is likely warped.
Each face of a board should be checked this way to make sure it has a uniform shape.
Don’t Let Wood Warping Hold You Back
Wood warping can be a common problem for those working with this natural but complex and versatile material. And many manufacturers find it vital to limit warping, especially when structural integrity or design aesthetics are important in the finished product.
There are many factors that affect the behavior of wood as it acclimates to different humidity levels and environments. But by knowing these common causes and ways to prevent warping, you’re better prepared to implement the right quality control measures. And whether you manufacture wood siding, wood molding or wood furniture you can be confident how your wood products will take shape.
About AQF
Material quality is one of the most important aspects of quality control. By inspecting your raw materials and the environment they are being stored in before they enter the manufacturing process, it is easier to detect and prevent defects such as wood warping.
AQF offers quality control services at every stage of the supply chain: starting with raw material selection and factory audits. Our technical engineers work alongside your team to understand key risks and ensure the AQF product-specific checklist is fully customized to your needs.
Contact us today to learn more or sign up for AQF Online to book your next service.
Editor’s note: This post was originally published in July 2016 and has been updated for freshness, accuracy, and comprehensiveness.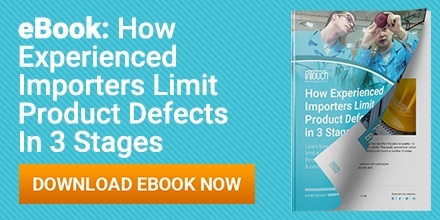