According to the Jesse Garant Metrology Center, the aerospace industry saves $1,000 for every $1 it spends catching and identifying a critical defect before production. That mean an aerospace company can save $80 million in rework costs just by investing $80,000 in finding defects before production begins.
Preventing product defects in an order comes at an upfront cost. But the cost of addressing defects later in production is almost always much greater (related: How Experienced Importers Limit Product Defects in 3 Stages [eBook]).
And the costs aren’t just monetary—addressing product defects often takes time and delays shipments. These can ultimately affect your bottom line as customer satisfaction plummets.
Incoming quality control (IQC) is the process of controlling the quality of materials and parts for manufacturing a product before production begins. With incoming inspection, you can control for quality even before conducting a first article inspection or a during production inspection.
Whether you manufacture industrial or consumer products, component and material quality is a key determinant of finished product quality. So let's explore how incoming quality control can help you verify quality before production.
Why is incoming quality control important?
Foreign suppliers typically only specialize in a few specific production processes, or even just product assembly. Most suppliers rely on a network of sub-suppliers to provide raw materials, components and packaging for their finished goods.
But one of the most common mistakes importers make is assuming the quality of raw materials from sub-suppliers will meet their quality standards.
You’re especially likely to face quality problems if you’ve negotiated the price of your order too low to cover the cost of high-quality materials or components (related: Preventing Product Defects Starts with Negotiating with Suppliers). Suppliers will typically try cutting their manufacturing costs to recoup their margin by:
- Using substandard materials (e.g. lower quality fabric than required for your garments)
- Substituting lower-cost alternatives for product components (e.g. cheaper electronic components in a mobile phone)
And it’s not just those importers working with new suppliers who are at risk of material quality issues. Even a supplier you have a long-established relationship with might take shortcuts with materials in hopes you won’t notice changes in product quality from one order to the next.
“Quality fade” is a common phenomenon whereby suppliers make small, gradual substitutions in materials and components over time. It’s easy to overlook this gradual decrease in product quality between orders if you’re not vigilant. And the consequence may be that your customers discover problems before you do.
Quality issues aren’t always a result of a conscious decision on your supplier’s part. Your quality standards might simply get lost in translation as your supplier relays them to their sub-suppliers.
Controlling for quality before production begins will help you prevent quality issues before they can affect production units.
How a clear incoming inspection procedure helps prevent product defects
Imagine you’re manufacturing smartphones. But your supplier hasn’t established an incoming inspection procedure to manage the quality of sourced electronic components. During pre-shipment inspection, you discover a major integrated circuit issue that affects product functionality.
One of two scenarios will likely follow:
- If the integrated circuit issue only affects one or two units of your order, your supplier might easily be able to disassemble and replace the affected units.
- If the issue affects all or most of the order, you’ll likely face shipping delays and high rework costs as your supplier replaces the component.
Suppliers usually purchase raw materials and components in high volumes to cover an entire order. This means quality issues with inferior parts or materials could affect all or most of your order quantity.
Correcting an issue like the use of inferior materials is rarely cheap and almost always time consuming when done after production has already started (related: 4 Ways to Address Product Defects Found During QC Inspection). Proper incoming inspection procedures can help you catch quality issues before it’s too late or too expensive to address them later.
How can you carry out incoming quality control?
You know the importance of quality materials in determining finished product quality. But how can you conduct incoming quality control to verify the quality of materials and parts used in production?
Effective IQC must precede mass production. Unlike pre-shipment inspection, IQC doesn’t include inspecting finished goods. Instead, IQC is a process that can take different forms depending on your product type and quality standards.
Component and material testing at a certified lab
How would you like to buy a 24-karat gold ring only to discover later that it’s actually only 10 karats? You’d be pretty upset about not getting what you thought you paid for.
Product materials testing is often essential for products like jewelry or rubber tires where composition can influence the value, performance or safety of the product.
Component and materials testing methods can include:
- Chemical testing and analysis, including composition analysis, trace contamination detection, metals testing and identification of unknown substances
- Physical properties testing and measurement, such as durability, stability, strength and flammability testing
- Mechanical properties testing, including testing resistance to deformation, fracture and fatigue
- Regulatory testing, for testing compliance with legal standards governing your product type and target market
Most importers don’t rely on the factory to conduct materials testing because tests often require specialized equipment and personnel the factory may lack.
Letting staff at the factory choose the samples for IQC inspection and testing also presents a conflict of interests. Factory staff are vulnerable to selection bias, “cherry picking” samples known to meet standards (related: Why Most Importers Don’t Rely on Factory QC Staff for Inspection).
Hiring a professional third-party inspector to randomly pull samples at the factory ensures test samples are representative of actual material quality throughout the order. These inspectors can then send the samples to the certified laboratory for testing.
Component and materials testing methods will vary based on your product type. But regardless of product type, relevant lab testing will help you verify whether raw materials and components meet your requirements for the product’s intended application.
Incoming inspection of materials and components
By inspecting raw materials before production begins, you can direct your supplier to address quality issues before production begins.
For instance, incoming inspection procedures for an order of leather boots might include inspecting the raw leather for quality defects, such as wrinkling. Then, if IQC inspection reveals excessive wrinkling, you can ask you factory to either:
- Separate defective portions when cutting the leather for production if there’s enough unaffected leather to continue manufacturing; or
- Buy replacement leather if wrinkling affects all or nearly all of the material
Inspectors typically rely on an acceptance sampling plan like AQL to determine a sample size for inspection. From this inspection result, you can either accept or reject the lot of raw materials for production. It’s often helpful to re-inspect after any corrective action to verify expectations are now met and it’s OK to proceed to production.
Verifying the component data form (CDF) and other documentation
Products made up of many different components, like consumer electronics, often have an associated component data form, or constructional data form (CDF). A product’s CDF helps set clear standards with your supplier to ensure they don’t substitute inferior parts when manufacturing your product.
A CDF shows a list of a product’s components and their approved manufacturers, typically including data such as:
- Object/part number
- Approved manufacturer or trademark holder
- Type/model
- Technical data, including materials, voltages, securement methods and measurements
- Standard, such as UL, IEC, EN and CSA standards
- Mark(s) of conformity, such as UL, CE and CCC
Inspectors can visually verify component construction during IQC inspection and compare markings to ensure they match your CDF. In this way, you don’t need to test each individual component for function and performance until a pre-shipment inspection.
Verifying a CDF during IQC inspection can therefore reduce the time needed for inspecting and testing components. If you’re confident in the quality of components from your approved manufacturers, it’s reasonable to expect consistent quality of components from those sources.
Other valuable quality documentation for materials and components
You can also ask your supplier for a bill of materials (BOM). The BOM is a list of raw materials, sub-components and parts used in manufacturing a product. Seeing the BOM can help you verify whether the supplier is using the proper materials and components for your order and hasn’t misunderstood your requirements.
Outlining your quality requirements in a QC checklist might also help ensure your supplier doesn’t overlook your material and component requirements. Sending this QC checklist to your supplier before production gives them a chance to offer any feedback and confirm whether they can actually meet your requirements.
Should your supplier conduct incoming inspection?
Not all importers need to hire a professional third party or conduct incoming inspection themselves. Suppliers with a well-developed quality management system (QMS) should have their own incoming inspection procedures in place.
But you might still benefit from third-party incoming quality control if:
- You’ve experienced quality issues stemming from raw materials or components in previous orders
- The raw materials or components for your product are rare, expensive or otherwise difficult to replace or rework
- This is your first time working with a supplier and you want to verify their incoming inspection procedures
- You require lab testing for product materials and components
In these scenarios, hiring a third party for incoming inspection can provide added assurance that everything is on track before production begins.
Audit your supplier to verify incoming inspection processes
Conducting an audit of your supplier’s QMS, typically following ISO 9001 standards, can help you verify your supplier’s incoming inspection processes. This kind of audit often includes checkpoints related to incoming inspection processes, such as:
- Are there procedures that define acceptance activity (inspections, tests, verifications) and record keeping requirements for incoming products and materials? Is there evidence of compliance?
- Is there a documented and properly implemented process for collecting defects at the incoming inspection stage?
- Are defects well identified by type/category for sorting and analysis?
Assessing your supplier in this way helps you determine if your supplier has established robust incoming inspection processes to manage material and component quality.
If you choose to rely on your supplier to conduct incoming inspection, be sure to request photos of raw materials and any materials testing and delivery records. It’s usually difficult to authenticate these without a trusted agent verifying them firsthand. But requesting them from your supplier is better than taking no precautions at all to verify quality before production.
Conclusion
A product is only as good as the sum of its parts. Manufacturing a quality product starts with using quality materials and components. And quality issues in materials and components are generally reflected, and even amplified, in the finished product. That’s why it’s vital to catch any quality issues in parts and materials before production starts.
Incoming quality control can help you verify the quality of those materials and components of your product through:
- Lab testing
- Incoming inspection, and
- Verification of the CDF and product documentation
The next time you’re considering working with a supplier that claims to sell top-quality products, ask them to provide documentation of their incoming inspection process. If they can’t provide clear records, you may want to hire a third party to conduct IQC inspection and verify quality before it’s too late.
Download our eBook below to learn how quality control inspection can help you minimize product defects in your final goods!
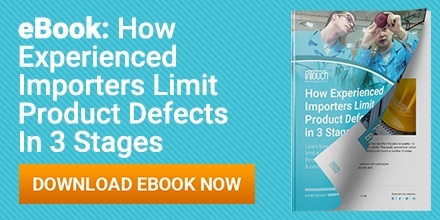