Imagine you’ve been working with a supplier for several years without issue. Then one day, you start receiving complaints. Then you start noticing minor, but frequent, flaws in your products. At first it’s small things like broken seams or poor stitching, but then the material quality starts to degrade or the coloring is off and suddenly you have a problem.
This is referred to as quality fade and it is one the most common challenges that importers face when working with clothing manufacturers in China. But that doesn’t mean you have to just accept it. Quality fade can easily be overcome by putting a few safeguards in place.
What is quality fade?
Quality fade occurs when the quality of the garments starts to slowly degrade over time. Initially, your products will look and function the same. But over time, similar problems will become much more frequent and obvious.
Maybe the zippers are getting stuck or the buttons on your shirts are popping off. Customers most likely won’t notice small defects here and there, but when comparing items over a longer period of time, quality fade can become apparent.You may even lose your customers’ loyalty if the issue persists.
What causes quality fade?
Chinese manufacturers aren’t trying to hurt your brand. They are actually thrilled to have your business. That is why product quality was so high in the beginning. Your supplier was going above and beyond to win you over and it simply was not sustainable in the long run. And rather than raise their prices and risk losing your business, they might have decided to cut costs internally and hoped you wouldn’t notice.
The good news is that by staying vigilant and implementing a strict quality control process, it is possible to avoid quality fade with clothing manufacturers in China and still maintain a healthy relationship with your supplier.
What are the solutions to quality fade?
Setting quality standards can be hard enough, so how can you maintain those standards when your supplier is constantly trying to slip one past you? It’s not as difficult as you might think! Here are three easy ways to avoid quality fade with clothing manufacturers in China.
Prepare a quality control checklist and stick to it
An importer needs a practical quality control checklist to provide specific product requirements to their manufacturers or suppliers. Typically, the list gives the quality standards that the manufacturer should meet. It also provides a method of product inspection. This will reduce the chances of receiving an order that does not meet your clients' standards. Some of the essential elements of a quality control checklist include:
- Basic workmanship requirements
- Packaging requirements
- On-site check
- Defect classification
Inspect raw materials in advance
It is vital to do a proper material inspection before manufacturing begins. A pre-production inspection will help you to identify quality issues at the early stages of production and minimize potential defects. You can even have certified off-site material testing; all this is worth your money if you want to maintain your brand reputation.
Work with a third-party inspection company and conduct regular inspections
It is normal for an importer who does not have an external inspection team to doubt what they have paid for until they receive the final product. If the product does not meet their standards, they may be forced to request a refund or return the product, which is time-consuming and expensive.
Here comes the benefits of working with a third-party inspection company. Through this, the manufacturer can either address the root cause or rectify the underlying problem of the product.
A third-party inspection company can help with quality control whichever manufacturing stage you are. It can help to audit if a factory is the right supplier you are looking for, inspect the product during the manufacturing process, supervise your orders boarding the container, or even provide you with lab testing results to ensure the safety of your products.
Don’t Let Your Standards for Quality Fade
Customer expectations are high in the garment industry and even small discrepancies can result in a loss of interest. If you are importing from overseas, working with a trusted third-party can help you maintain strict quality standards and keep your customers happy for years to come.
AQF is a leading Quality Control service provider, serving global brands, importers, and retailers of Consumer Products in more than 135 countries since 2007. Our online platform allows you to access detailed reports and collaborate with your vendors on corrective actions.
Contact us today to learn more about how AQF can help to avoid quality fade and maintain your high quality level!
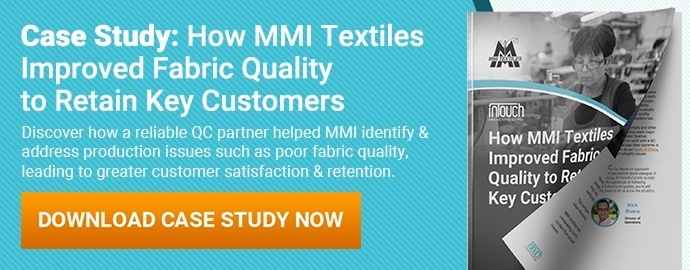