Custom components are made to your exact specifications and special requirements. The manufacturing processes can vary, but the quality control of these components is vital.
Let’s explore the various manufacturing options for these custom components and the most effective ways to ensure quality.
Part 1: CNC Machining
CNC machining is a manufacturing process that uses pre-programmed software to cut or move material. It gives unmatched accuracy for manufacturing metal and plastic parts.
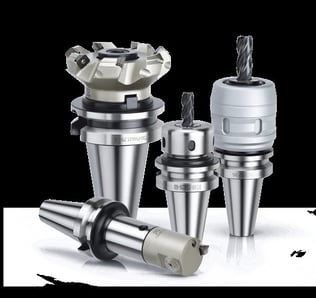
A general CNC machining process mainly includes 6 steps:
- Milling - rotating cutting tool contacts with a stationary workpiece
- Turning - rotating a workpiece to contact a cutting tool
- Drilling - rotating cutting tool contacts with the workpiece to create a hole
- Boring - removing material to make an inner cavity within a workpiece
- Broaching - removing material with a series of shallow cuts
- Sawing - cutting a narrow slit in a workpiece using a saw blade
However, using CNC machining have some limits. For instance, the majority of CNC machines have circular tooling, so the part's geometry is limited to curved corners due to the tooling. It would be difficult if you want your custom parts to have straight edges with CNC machines.
Also, CNC machines also have limitations on your material options, the design of the tools, and the minimum part thickness.
Part 2: Sheet Metal Fabrication
Sheet metal is a metal that is commonly used for manufacturing as it yields robust, end-use metal parts that can be made to your specifications. With sheet metal fabrication, you can turn flat sheets of steel or aluminum into the high-quality custom components that you want.
Sheet metal can be made into various sizes of components. These components can be found in industries ranging from furniture, construction, automotive, to aeronautics.
The main methods used in sheet metal fabrication are cutting and forming. Cutting is where the metal is separated through force being applied, which enables the material to be modified into the desired shape. The force is applied either by shearing, heat or abrasion.
Here are some examples of sheet metal fabrication:
|
|
|
|
|
|
|
|
|
Stamping is a process that places flat sheet metal in either blank or coil form into a stamping press where a tool and die surface forms the metal into a net shape. It is a cost-effective and fast way for large-scale manufacturing.
Metal stamping is commonly used in manufacturing components within the automotive, medical, and aerospace industries, amongst others. The demand for metal stamping is growing as the demand for complex parts to be manufactured at a fast pace in mass is evolving with the development of global markets.
By programming the machines or using computer controls, the stamping process can achieve high precision and repeatability. In addition, electrical discharge machining (EDM) and computer-aided design (CAD) programs are commonly used to guarantee accuracy.
Part 4 Injection Molding
Injection molding is the process of producing parts by injecting molten material into a mold. This process provides top performance and cost-efficiency for high-volume production parts.
Injection molding is a great choice when manufacturing at high volumes, for instance, mass-production where the same piece is being produced multiple times in sequence.
One of the main reasons people choose injection molding is the ease to scale production from low quantities to mass production. Although the initial cost can be quite high, the price per unit drops considerably and makes high volumes very cost-efficient.
Meanwhile, there also exist some limitations of injection molding, including:
- The high initial setup costs, related to design and tooling predominantly. If you are producing in bulk, you want to make sure the design is right, which requires testing at the beginning. This is often complex, and involves;
- The design followed by prototyping the part to ensure it meets the specification
- Original prototype development is usually finished on a 3D printer and typically in a material difference to the material of the final part (such as ABS plastic) - Designing the injection mold tool for the first manufacturing round
Creating an injection mold tool is usually needed for producing 300-1000 injection molded prototypes in the production material. - Adapting and making needed changes to the mold before mass production begins.
How to ensure the quality of your custom components?
Custom component manufacturing is often essential for certain products and its quality should be strictly controlled. As such, a clear incoming inspection should be performed to address quality issues before your components are assembled.
For example, in a Pre-Shipment Inspection, the inspector will check the points below and conduct some on-site testing to ensure you are getting what you ordered:
- Key material verification: checking if the components are made of the materials that you requested
- Visual check: visually checking if the components match the drawing provided
- Dimension check: checking the dimensions of each part of the components to see if it matches the requirements
- Weight check: checking if the weight of the components is correct
- Real unction check (if applies)
Additionally, if your custom components are critical, you can establish a construction data form (CDF) to check the parts. A CDF verification can be a lower-cost alternative to testing every electronic component in your product at a professional lab.
With a professional third-party quality control company like Asia Quality Focus, you can always request to check some specific areas/points based on your needs. The inspector will perform the inspection, generate a report, and ensure sure your component’s quality meets your requirements.
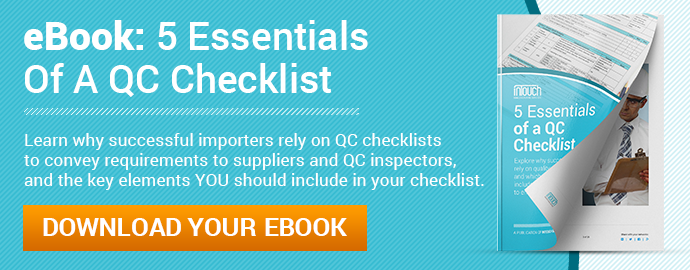