Imagine you’re a distributor of household electrical appliances. You’ve been receiving reports from customers that a clothes dryer you sell has been sparking and even catching fire in some cases.
After investigating the issue, you discover your manufacturer recently started replacing critical components with inferior parts sourced from cheaper suppliers. How could you have known the factory substituted these parts without your approval?
Verifying the product’s construction data form (CDF) during pre-shipment inspection is one of the simplest and most effective ways to check critical components in your electronic products. And CDF verification can be a lower-cost alternative to testing every electronic component in your product at a professional lab.
Establishing a CDF also helps limit defects in the finished goods by setting clear quality requirements for critical components (related: How Experienced Importers Limit Product Defects in 3 Stages [eBook]). You can ensure your product is safe for consumer use and functions as intended by confirming it contains only approved parts and materials.
What is a construction data form (CDF)?
A construction data form is also sometimes referred to as a component data form or critical components list. It’s a document listing each of the critical components in a product and the approved manufacturers of each.
Buyers tend to develop construction data forms only for electrical products, as these products are more susceptible to function and safety problems if manufactured with substandard parts.
And given how often many overseas suppliers misunderstand requirements, electrical products often need more detailed documentation to set clear product standards (related: 4 Challenges of QC for Complicated Products).
What are critical components?
So how do you know what “critical components” should be included in your construction data form? According to the International Electrotechnical Commission (IEC), critical components include any:
- Components which can compromise the safety of the product if they fail
- Components which have specific requirements in the end-product standards
- Components which have requirements in any applicable national standards
- Materials which are critical to maintaining compliance with the standard
Critical components are also sometimes referred to as “safety critical components” as product safety is a primary concern in developing a critical components list, or CDF. Your CDF will vary based on your product type and its intended use. But some common critical components include motors, fuses, circuit breakers, switches, batteries and transformers.
Once you’ve identified the critical components in your product, the completed CDF should list relevant information for each component, including:
- Part number
- Manufacturer or trademark name
- Part type or model
- Technical specs
- Relevant testing standard
- Certification markings or symbols
For example, A CDF for an electrical appliance exported to Germany might include something like the below:
How a CDF is used in electronic component testing
Once you’ve determined your critical components, how do you use your CDF? As the importer, you or your manufacturer will typically send samples of critical components to a professional laboratory for testing before production.
The lab will then check these components against an existing CDF to ensure compliance with international safety standards and the product’s specifications. Or, if the manufacturer is submitting a new component or supplier for approval, the lab can approve the component and revise the CDF to include it.
The manufacturer will ideally send multiple samples from different suppliers for their initial part testing. This way, they’ll have a large pool of approved suppliers from which they can source parts. And the manufacturer can always resubmit new parts to a lab for a revised CDF, if needed.
Some harder-to-source components like a particular PCB may not have any alternative suppliers listed in the CDF. But other more easily sourced components like a plug or internal wire might have five or six different suppliers listed, depending on availability.
Why electronics importers need a CDF when manufacturing abroad
You might be thinking that creating a CDF and testing electronic component seems like a lot of extra work before production. Can’t you just rely on your supplier to manufacture these components?
The short answer is usually no, you can’t.
Most electronics suppliers don’t manufacture all the components that go into the product themselves. Rather, they rely on a network of sub-suppliers to manufacture and supply the parts, which they then assemble into the finished product at their facility.
And these end manufacturers you’ll typically work with sometimes lack robust incoming quality control procedures to evaluate the quality of their supplier’s goods. And they might frequently switch suppliers to cut their costs or meet production demand without informing their customers.
For these reasons, you must carefully assess the critical components in your product to ensure they meet quality standards.
Establishing a CDF and testing critical components before production helps:
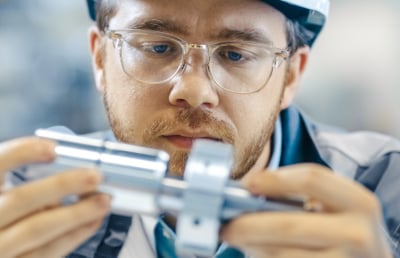
- Ensure only approved components are used in manufacturing your product
- Prevent quality defects from affecting the entire order
- Eliminate the need to test individual components when testing the finished product later
- Provide necessary documentation for international certifications and regulatory compliance
By compiling a CDF and conducting pre-production lab testing, many importers find they don’t need to conduct further lab testing on the final product after production.
CDFs are required for IEC certification
Another reason electronics importers might need a construction data form is for an IEC certification.
IEC standards are some of the most commonly used international safety standards for electrical and electronic components, equipment and products. And a critical components list is one of the document requirements for an IEC test report.
The IEC System for Conformity Assessment Schemes for Electrotechnical Equipment and Components (IECEE) CB Scheme is a multilateral agreement among participating countries that promotes harmonization of national standards with IEC standards.
IECEE test reports and certifications are mutually accepted in all 53 member countries in the Scheme, including major export markets, such as the U.S., UK, EU and Australia.
IECEE covers 23 different electrical product categories. Some common IEC certifications that require a CDF include:
- IEC 60335: Household and similar electrical appliances
- IEC 60601: Medical electrical equipment
- IEC 60598: Luminaires
After establishing a critical components list, testing can help you validate critical components for IEC certification.
How to verify critical components during pre-shipment inspection
Now that we’ve established how a CDF is created, how is the CDF used during pre-shipment inspection of your finished goods?
CDF verification offers importers an alternative to on-site testing.
Many electronics importers believe on-site function and stress testing are vital for ensuring their product’s safety. But a couple constraints limit importers’ ability to conduct comprehensive function testing during inspection:
- Time needed to test: Time-consuming testing can raise QC costs when hiring a third-party inspector that bills based on time spent on site (such as in “man days”) and can delay urgent shipments.
- Equipment and expertise needed for testing: Factory staff and inspectors might lack the equipment or expertise needed to perform complex safety or function checks.
Instead of conducting on-site testing, inspectors can visually check all critical components to verify they match the approved components listed in the CDF.
If an inspected production unit is found to be constructed with all the same components as the earlier tested sample, you can reasonably assume it meets the same standards.
CDF verification procedures during inspection
When verifying a CDF, the inspector disassembles one or two units and checks the conformity marks on the unit’s critical components with those listed in the CDF. Any inconsistencies with the CDF may indicate the factory has replaced critical components with untested ones.
The inspection report should note the markings found on each of the critical components with a photo of the component. If the CDF is not available during inspection for whatever reason, the inspector should still take photos of all components found on site. Component markings can be checked against the CDF later once it’s available.
The inspector can also ask for relevant certifications for the components if they have reason to doubt the components match the CDF. A supplier should always have these records available on request. Just be sure to inform your supplier before inspection to have the CDF and relevant certifications available for review to avoid any delays during inspection.
The inspector typically performs an internal check along with the CDF verification, since both require disassembling the product. During this internal check, the inspector checks the quality of construction and ensures components have been assembled correctly.
You might also include this CDF verification and internal check in your QC checklist to set clear expectations for inspection:
Consider any pre-production testing invalid if the pre-shipment inspection reveals inconsistent components. In such cases, it’s best to test the product and components again to ensure they meet your standards.
Conclusion
All electronics importers should want to sell a safe product that functions as intended (related: 5 Electronic Product Recalls QC Inspection Could Have Prevented). Verifying the product’s critical components match those in a construction data form is a cost-effective way to accomplish this.
Checking the CDF offers assurance of product quality and safety without taking much extra time on site. And while creating and validating a CDF through testing before production takes time, the CDF will save you more time in the long run by providing a reliable reference of your requirements for production.
An electronic product is only as good as the sum of its parts. And ensuring the quality of critical components will go a long way in helping you deliver a high-quality product to your customers.
How do you ensure the compliance of your electronic components? Share your tips in the comment section below!
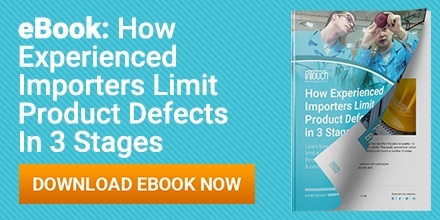