Each Sunday, we publish a list of top articles and other content related to manufacturing in areas like quality control, product development, supply chain management, sourcing, auditing and law.
1. Industrial innovation in the U.S. compared to China
The United States is a global research leader. In 2015 alone, around $500 billion was spent on industrial research, which is approximately a third more than China, three times more than Japan, and four-and-a-half-times more than Germany.
Although the U.S. has this strong lead in overall research spending, that doesn’t mean the money is allocated the same way in those other countries.
The distinction between what that money is funding comes down to three types of research:
- Basic research: this category is concerned with expanding knowledge in general. There isn’t a specific focus on products or processes.
- Applied research: this category is concerned with solving practical problems and improving the human condition.
- Development research: this category is concerned with developing “useful materials, devices, systems or methods”
The U.S. leads in conducting basic and applied research. But China, bolstered by Made in China 2025, is now spending more on development research. In the next five years, China’s expenditures on this type of research are projected at twice as much as the U.S., which could provide significantly more competition in the global industrial innovation arena.
Implications for manufacturers and importers
The differences in how research money is allocated and eventually turned into value for manufacturing could have broad ramifications for importers. Choosing to source from one country over another might boil down to how the success of research manifests over the next few years.
Even with how the U.S. currently allocates industrial research money, according to the 2016 global manufacturing competitiveness index by Deloitte, by 2020 the U.S. is projected to become the number one manufacturing economy. Yet as China moves up the industrial value chain, it’s hard to determine just how solid that projection is.
Whether an importer’s future is intertwined with America, China, Germany, Japan or some other country with significant research expenditures, hopefully, the end result for consumers everywhere is better products at lower prices.
To read more about research and manufacturing, especially within the context of America, check out the full article in the link below:
An Innovation-Led Boost for US Manufacturing – Hal Sirkin, Justin Rose and Rahul Choraria, BCG.com
2. 3D printed modifications and your product liability
Your lawyers and product designers have worked on them for days. They’re finally available: the warnings that will accompany your product.
The team at your company has done what is reasonable to prevent foreseeable misuse of your product and avoid any product liability litigation. But there’s one element your team didn’t consider that can stifle your all your efforts, and it goes by the name of 3D printing.
Transforming and augmenting products has become remarkably easier with the abilities that 3D printing offers. Customizable modifications open up a world of possibilities for end users to get creative with what you’ve sold them. This article mentions “car engine parts to climbing wall holds to firearm silencers” as a few examples of what consumers have made to use with their products.
What’s important to acknowledge is that, since the product has changed from the modifications and/or accessories, that casts the usefulness of your product warnings into doubt. As the author reports:
Critically, the range of uses that are foreseeable can change over time: uses that may not have been foreseeable when a product was initially designed can become foreseeable as a result of changes in consumer behavior. Manufacturers of consumer products will need to monitor how their products are being modified by consumers and then consider whether popular 3-D-printed modifications and accessories require design changes or revised product warnings to keep consumers safe.
3D printing changing the functionality of products means then that product warnings can’t remain static. It’s now necessary to stay vigilant of the ways consumers are combining 3D printing and your product, which might entail constantly updating warnings to anticipate and prevent any potential issues that could result in legal trouble or injury to end users.
While it may seem far-fetched to have to worry about the endless possibilities of 3D-printed items that consumers could use in conjunction with your product, it won’t seem so unbelievable if you’re in court one day discussing product liability as the defendant.
To read more about the relationship between 3D printing and product liability, check out the detailed article in the link below:
What You Need to Know About 3-D Printing and Product Liability – Andy Crowder and Alex Fenner, Industry Week
3. A milestone for 3D shoe printing
If you’re wearing shoes, chances are that at least a part of them was made using injection molding. In case you’re not familiar with injection molding, it’s a very popular manufacturing method that involves injecting materials into a mold for a certain part – say, for the sole of a shoe.
While injection molding is great for mass production, it’s not always economical for smaller production runs. The reason for this drawback is that you need a mold to begin production. And sometimes molds are expensive or require too much time to make for just a small batch of product.
Recently, however, Adidas launched a shoe with a sole that was 3D printed. Adidas partnered with a startup out of Silicon Valley named Carbon to open the doorway to mass production using 3D printing, which could potentially offer these benefits:
- Greater shoe customization
- Potentially faster time to market
- Less reliance on expensive molds, which might reduce costs for consumers
- Better quality shoes and shoe components, assuming that 3D printing doesn’t experience something similar to injection molding defects
Using past 3D printing methods, creating a shoe sole took an hour and a half. With Carbon’s technology, that time could shrink to only 20 minutes per sole. And excitingly, this method is slated for the mass production of 100,000 units of Adidas shoes next year.
For manufacturers and importers, this technology represents a significant milestone. By adopting effective 3D printing capabilities, companies might gain the ability to sell to more consumer segments and with less risk compared to injection molding. Although Adidas is a large company and can afford technology like Carbon, it might only be a matter of time before more shoe makers (and manufacturers in general) turn to 3D printing for mass production.
To learn more about 3D-printed shoes, check out the full article in the link below:
Adidas Will Mass-Produce 3D-Printed Sneakers with This Silicon Valley Startup – Retuers via Fortune
4. Bangladesh connecting to the Silk Road
The One Belt, One Road initiative, or OBOR for short (一带一路 in Chinese), is a massive project spearheaded by the Chinese government. Essentially, the aim of the initiative is to connect the East and West via land and sea routes to foster trade and geopolitical ties, much like the ancient Silk Road did in centuries past.
For some countries though, like Bangladesh, OBOR also offers something else: reliable electricity and poverty relief. Around half of Bangladesh’s population doesn’t have reliable access to electricity. Understandably, this problem challenges reliable manufacturing and industry in the country. But OBOR can help change that.
According to the article,
According to HSBC estimates, China will invest about US$23 billion in at least 28 projects in key areas from power plants and roads to bridges and railways in the next five years.
Bangladesh’s low wages are an attractive reason to conduct business there. And with OBOR projects, more importers can potentially use this competitive advantage for their businesses while also providing more commercial opportunities to the people of Bangladesh. OBOR could ultimately mean more electricity, less poverty and more business, so long as the projects go according to plan.
To learn more about OBOR and its effect in Bangladesh, check out the full article in the link below:
Bangladesh Plugged into China's Belt and Road Scheme, HSBC Banker Says – Sidney Leng, South China Morning Post
5. The pros and cons of Vietnamese labor
Monthly pay for workers in Vietnam ranges from around 200 to 250 USD. Although this range can certainly wade into higher figures, it’s even cheaper than China. The author points to the example of lesser developed areas in western China where monthly labor costs per worker start at approximately 300 to 350 USD.
Part of this variance in price is due to how young, and unskilled, the workforce is in Vietnam. The article reports,
- Vietnam’s labor force is 54.5 million people
- 74 percent of the labor force is less than 50 years old
- 80 percent of the workers don’t hold any formal qualifications
- Approximately 9 percent have graduated from a university
- Around 21 percent have “received any kind of professional training of three months duration or more”
All the figures mentioned above pose benefits and obstacles for importers trying to source in Vietnam. On the one hand, for relatively simple products that require little more than manual labor, the country’s lower wages might allow for wider margins and a greater number of orders. Yet conversely, if relatively sophisticated engineering or technical skills are needed to fix quality issues, importers might find themselves worrying if Vietnamese factories can consistently meet their standards.
How do you feel about the strengths and weaknesses posed by Vietnam’s labor force? Let us know in the comments below.
To read more about some of the benefits and challenges related to the Vietnamese labor force, check out the full article in the link below:
Vietnam’s Youthful Labor Force in Need of Production Services – Wing Chu, HKTDC Research
We’re constantly scanning the web for top manufacturing stories and news. If you’d like to submit an article for consideration for our weekly Best in Manufacturing, send us a message and let us know.
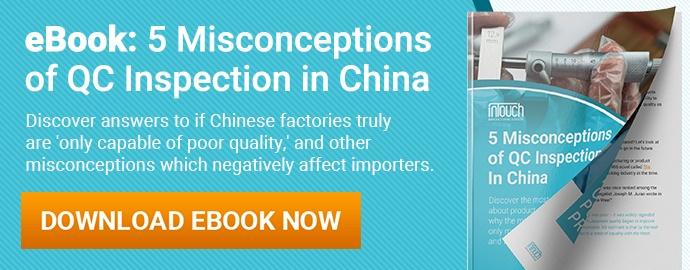