Best in Manufacturing – October 28, 2018
Each Sunday, we publish a list of top articles and other content related to manufacturing in areas like quality control, product development, supply chain management, sourcing, auditing, and law.
1. Is your supplier acting as a front for prison labor?
A note found in a purse bought at Walmart recently went viral after it was shared on social media.
The note—supposedly written by a prisoner—claims the purse was made through forced labor in a Chinese prison. A portion of the translated note reads:
Inmates in China’s Yingshan Prison work 14 hours a day and are not allowed to rest at noon. We have to work overtime until midnight. People are beaten for not finishing their work.
This isn’t the first time a customer has found a note like the one from Walmart. Saks, Zara, and Kmart customers have also found similar notes suggesting illicit company practices.
The notes will typically follow a similar form that suggests:
- The product was made with forced labor in poor working conditions.
- The writer is from a distant country, often China.
Customers are quick to blame the brand when notes surface, dealing a major blow to the company’s public image.
But like many companies, Walmart said it had no way of verifying the note or tracking down the worker in question.
Complex supply chains make an accurate tracing of forced labor difficult
Many manufacturers don’t knowingly participate in the illicit practices named in prisoner notes.
According to Li Qiang, founder of China Labor Watch, complex supplier networks allow for murky labor practices. It’s not uncommon for a factory to act as a front for products made in prisons.
In this scenario, an importer might place an order directly with a factory or trading company. But the factory then transfers the order to prison, without the company’s knowledge.
Once nearing completion, products are transferred back to the original factory where they are labeled and prepared for shipment.
A supplier audit can help reveal these murky backchannels. But many companies fail to thoroughly vet suppliers and factories.
Outrage highlights uncertainties of Chinese production
According to the author of this article, “Made in China” is a positive phrase in China. But it draws other implications in the U.S.
The phrase draws ire, conjuring images of goods mass-produced in factories with questionable conditions by workers who have supplanted their own country’s workforce.
Notes like the one found by a Walmart customer can reinforce an inaccurate depiction of foreign manufacturing.
While manufacturing in China may mean lower labor costs, it does not necessarily indicate poor labor conditions.
Customers shop at Walmart because of the low prices. In a study by AP News 67 percent of respondents said they’d buy a $50 pair of pants made in another country over an $85 pair made in the US.
It’s unlikely Walmart could maintain such low prices with entirely domestic production. But they should be able to maintain them without using forced labor.
Can notes like these move the needle towards widespread awareness of overseas working conditions?
If notes like these continue to surface, consumers will undoubtedly continue to point their fingers at brands named in the notes. Brands should consider how to follow up with better vetting and tracing of their entire supply chains.
You buy a purse at Walmart. There’s a note inside from a “Chinese prisoner.” Now what? – Rossalyn Warren, Vox
2. Second customer death at Pret a Manger reveals internal QC issues
In the last year, two customers have died after eating food with incorrect allergen labeling from Pret a Manger.
One customer died after buying a supposedly dairy-free flatbread last December. And just last month, a 15-year-old girl died from a sandwich unlabeled with sesame seeds.
The deaths highlight two major issues in the food industry—inaccurate labeling and a lack of supply chain transparency.
Parents of the young girl are pushing for urgent action. They want stronger food labeling laws and responsibility throughout the food chain.
But before legislation mandates greater customer safety, Pret a Manger will need to address its own quality control issues.
Sub-supplier to blame for contaminated yogurt
Pret a Manger traced the first allergen-related death back to its supplier CoYo. CoYo supplies Pret with a dairy-free yogurt used in its “super-veg rainbow flatbread”.
Pret said CoYo mis-sold a guaranteed dairy-free yogurt. Last February, CoYo recalled its yogurts after finding traces of dairy.
Working with the UK’s Food Standards Agency, Pret was able to identify trace amounts of dairy ingredients in materials used in CoYo’s products. According to CoYo:
This contamination was traced to a third-party supplier who we no longer work with.
After CoYo’s announcement, Pret immediately withdrew all affected products. The chain ended its contract with CoYo and is taking legal action.
Pret identified the issue in its supply chain. But the company relied on a supplier guarantee without ensuring the sub-suppliers met the same standard (related: 3 Complications of Sub-Suppliers and How to Avoid Them).
Thoroughly verifying CoYo and its sub-suppliers before using the products could have prevented a customer’s death.
Pret can’t guarantee allergy-free
The most recent death was not a supplier issue. Instead, Pret a Manger failed to label sesame seeds as an ingredient on the product packaging.
After this tragic error, the company promised to include full ingredient labelling on all products.
But both deaths were related to food containing allergens that shouldn’t have been there in the first place. A faulty supplier and mislabeled food are symptoms of a greater quality control problem.
Last week, the company posted notes in its London stores highlighting the nature of its production. Traffic cones sit among shelves of food adorned with little white warning notes.
Under a large title “Allergies?”, one note reads:
Our food is freshly prepared in small, busy kitchens (not a big factory with segregated production lines) so we really can’t guarantee any of our food is allergen-free.
Quality control can happen before the kitchen. If Pret wants to prevent future disastrous events, it’ll need to start thinking beyond the immediate symptoms.
Second Pret a Manger customer dies of allergic reaction after eating £3.75 vegan sandwich – James Wood, Daily Mail
3. Could robots become the preferred manufacturing employee?
Industry 4.0 encapsulates automation and data exchange in manufacturing technologies. It’s a trend towards computers and data coming together in an entirely new way.
Today, 90 percent of manufacturing tasks are still performed by humans. But with the rise of Industry 4.0, many are questioning how long this will last.
Employing robots on production lines is one aspect of Industry 4.0 gaining momentum in the manufacturing world.
Rapidly advancing AI and robotics can streamline tasks. And industry leaders are infatuated with their potential impact on production and profits.
Humans are still a necessity in many parts of production. But many are asking—can the human workforce survive manufacturing’s fourth industrial revolution?
Streamlining production can limit flexibility
One of the greatest potentials of robot automation is the ability to streamline tasks.
But robots on the production line are built to repetitively perform a single process.
Each process where the robot interacts with its surrounding environment requires a specific end effector. An end effector is a device on the end of a robotic arm, designed to interact with the environment.
But what if you want to try something new?
Changing just a single input port in your production line could require extensive end effector rework. This can limit production in two ways:
- It can be hard to find and retain capable talent. Engineers, programmers, and designers are in high demand.
- Rebuilding end effectors takes time. A team of professionals must create a new end effector. Humans, on the other hand, can learn to readjust their grip in real-time.
It’s possible this process could improve with time. But can robots ever match the flexibility of humans?
Manufacturing trends are on humanity’s side
Prasad Akella, founder, and CEO of data analytics company Drishti, said this lack of agility is a key reason company like Foxconn rely heavily on manual labor.
Robots can’t adjust to changing market demands nearly as fast as human workers.
Trends are constantly changing. And committing to an automated production line could hurt your flexibility.
Changing your production line to allow customization could yield significant financial returns. In a consumer survey conducted by Industry Week, 62 percent of respondents said they’d be willing to pay more to customize their devices. But customization would also require a certain level of flexibility.
Robots could be a regular feature in future production lines. But it’s unlikely robots will become the dominant factory workforce if customization continues to grow.
There are some areas where a human touch will always prevail.
Follow the link below for more information on Drishti and the downsides of a robotized manufacturing workforce.
A Human Touch in Smart Manufacturing – Ryan Day, Quality Digest
4. Will losing domestic incentives force Dixon to eliminate U.S. production?
In the 1990s, foreign-made pencils inundated the U.S. market. Today, most pencils are made outside of the U.S.
Dixon Ticonderoga has manufactured pencils in the U.S. for 223 years. But several global expansions and multiple factory closures later, just a few domestic plants remain.
The company still benefits from several trade policies because of its lingering U.S. presence. But these benefits may end soon.
Dixon’s legitimacy as a domestic company has come into question. And the company is fighting legal battles over the benefits it reaps from this classification.
This, along with rising trade tensions are likely to make Dixon rethink its manufacturing strategy. Will Dixon raise prices, shift operations or both?
Domestic manufacturing presence key to benefit entitlement
Dixon produces nearly 500 million pencils annually. But most of its production happens outside the U.S.
Dixon manufactures an undisclosed number of pencils at a distribution center in Macon, Georgia. This facility is where most of the company’s remaining domestic production occurs. And it’s a key factor allowing it to retain U.S. benefits.
U.S. law does not specify the number of domestically manufactured products required to receive government benefits.
The U.S. offers a range of incentives for companies considering domestic manufacturing. State and local governments are often the primary sources of assistance. But the federal government can offer:
- General workforce development
- Industry-specific incentives
- Energy efficiency grants
Dixon has come under fire for collecting benefits despite reducing its domestic presence.
The company recently lost its designation as a domestic manufacturer from the U.S. International Trade Commission. And continued legal proceedings may eliminate future benefits.
President Trump’s tariffs might incentivize companies to move production
President Trump’s tariffs on Chinese goods are an attempt to reduce the lure of global manufacturing. Making import costs greater than domestic production costs could, in theory, draw production back to the U.S.
Pencils haven’t been hit by President Trump’s trade war yet. And for Dixon, moving production outside the U.S. has been a sound investment.
But losing U.S. benefits could force the company to completely move production elsewhere.
The current trade climate is forcing many companies to reassess production lines. Some are considering moving to the U.S., while others explore diversifying sourcing from China.
Trade rules and incentives will likely change again in the coming years. And your production needs are unlikely to remain stagnant.
With the right attention to detail, you can maintain the quality and integrity of your product throughout these transitions.
Follow the link below for more information on Dixon’s journey through American pencil manufacturing.
America’s favourite pencil maker Dixon Ticonderoga blurs line of where it manufactures: in the US, Mexico or China? – Damian Paletta, South China Morning Post
5. Why so many companies fail to reap benefits of lean production
In the 1940s, Toyota began streamlining processes to eliminate waste and improve productivity with the Toyota Production System. Forty years later, John Krafcik coined the term lean production.
Approaches to the two methods differ but unite under a common goal—improve efficiency in the production process.
Manufacturing models of efficiency often promise to cut costs and drive production. But lean production aims to achieve more than this.
Lean principles focus on increasing value and engagement. Some even describe the business model as a way of life.
Implementing lean can streamline processes, remove waste and build commitment. But like any new business model, lean practices are not easy to implement.
Lean production eliminates waste and cuts lead times
The Toyota Production System Support Center is a nonprofit that helps small and midsize businesses streamline operations with lean production methodologies.
In 2014, Ace Metal Crafts Company was accepted into the Toyota program. With the help of an expert, Ace Metal focused lean efforts on welding, a long-time bottleneck of the business.
In the end, Ace Metal cut lead times on new orders by 50 percent. And business grew by 30 percent.
Ace credits the Toyota program as a significant driver for this growth. Streamlining production, eliminating waste and improving employee engagement helped the company improve operations.
Cutting lead times is a commonly cited benefit of lean manufacturing. According to MK North America, other benefits include:
- Increased product quality – Improved efficiency frees up resources.
- Sustainability – Less waste sets the stage for future growth.
- Employee satisfaction – Elimination of unnecessary work leads to happier workers.
These benefits could entice any business owner. Who doesn’t want to cut waste and improve overall performance?
Benefiting from lean production requires long-term approach
But lean production isn’t without its drawbacks.
Ace experienced significant growth with the help of a lean expert. Most companies don’t have an expert walking them through the lean process. Companies might attempt to adopt the general principles but fail to tailor them to their individual needs.
Sometimes companies see limited success because there’s too much starting and stopping of implementation.
Rachna Shah is a professor at the Carlson School of Management at the University of Minnesota. Shah said it’s important to continuously streamline processes.
According to Shah, without a long-term, continuous and disciplined commitment to lean:
You cannot have the same levels of improvement in productivity.
Another common criticism of lean is the failure to fully integrate the methodology. Companies may implement one principle but fail to integrate the strategy into overall process flows.
Lean is an opportunity to minimize non-value work activity from the manufacturing process. But it can be hard to fully commit to the methodology.
But you aren’t stuck with using just one methodology. Take the time to explore options and decide what works best for your company.
Follow the link below for more examples of companies adopting lean production processes.
Here’s the Skinny: For Lean Production Processes to Work, a Company Needs to Be All In – Ellen Rosen, New York Times
We’re constantly scanning the web for top manufacturing stories and news. If you’d like to submit an article for consideration for our weekly Best in Manufacturing, send us a message and let us know.
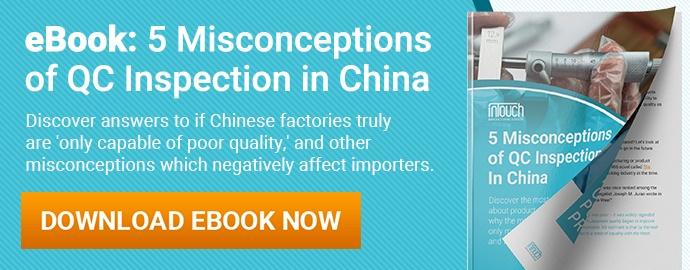