Best In Manufacturing – June 03, 2018
Each Sunday, we publish a list of top articles and other content related to manufacturing in areas like quality control, product development, supply chain management, sourcing, auditing and law.
1. Is your supplier overly dependent on quality inspections?
A crucial and valuable aspect of quality inspection is to have continuous open dialogue with your supplier. If at first they are confused about particular expectations, you may send an inspector to help them along. If they later encounter issues during production, you might even send your own engineer to straighten things out.
These may seem like the appropriate steps needed to ensure the quality of your product, but it’s important to proceed with caution. There’s a fine line between helping a manufacturer follow your guidelines and taking so much control that they’re unable to operate without you. You want to make sure they’re manufacturing to meet your quality standard, not do it for them.
How can you balance product inspections with supplier accountability?
The trick is to maintain a balance. Timely inspections will help you verify whether your supplier is giving you what you want. While creating financial accountability will help push a supplier to get the job done.
The first stage in finding this balance requires getting the first batch right. Depending on the type of product, and the quantity you are producing, this requirement might look a little different.
Stage two targets consistency. Can the supplier repeat this quality and catch any mistakes along the way? It’s hard to achieve this without regular inspections. But once they have the hang of it, consider requiring the supplier to do self-inspections and send you reports. Combining this with a system of financial accountability when unacceptable issues occur will allow you to take a step back and let them do their job.
The final stage is learning to trust your supplier when they prove their ability. If five batches in a row meet your standards, consider shifting to a “light” final inspection. Work together to reach a place where you both feel confident in each other’s expectations. After all, the end game is to have a supplier who knows what you want and how to provide it.
For a more in-depth understanding of these three stages and how they might adapt to your own company, visit the link below:
Helping a Chinese Factory While Still Holding Them Accountable – Renaud Anjoran, Quality Inspection
2. Smart manufacturers who optimize the IoT are simply understanding their data
The Internet of Things (IoT) has widely been accepted as the obvious business tactic of the future. But the less obvious aspect is how to use the data it brings in. Sure, the ability to monitor humidity-levels and get live-streamed updates on production numbers may seem futuristic. But how is it helpful if you don’t know what to do with the data?
Smart manufacturers have adopted various data management strategies to make the most of the IoT and give themselves a competitive advantage. Some have learned to improve production through automation, cutting costs and reducing waste.
Lido Stone Works has even increased productivity by 30 percent through equipment with built-in diagnostics and communication which minimizes strain on maintenance technicians. Others, like Kasser Kompressoren, have learned to use the IoT to strengthen their customer experience. They offer compressed air-as-a-service which saves customers the expense of purchasing industrial scale air compressors and machinery.
One of the more significant benefits of the IoT is the improvement it provides to safety and security. Factories are now using cameras that can automatically focus on a specific area during an alarm and wearable devices that can detect the presence of dangerous chemicals.
Which of these IoT tactics should your company be adopting?
The key to being a smart manufacturer is to single out the IoT strategy that best fits your company. Using them all may seem ideal but is simply unrealistic. As you encounter problems and analyze efficiency, be sure to research existing technology available. The IoT is both flexible and highly adaptable to any business as long as you know exactly what you need it for.
Consider things like durability, flexibility and design, as well as costs and payoffs when choosing what technology is right for you. The IoT is an investment but not one that you should make blindly. Do your research, understand the data and raise to the level of your smart competitors. Find more strategies and tactics for making the most of the IoT at the link below:
What Manufacturers Should do With IoT Data – Kayla Matthews, Manufacturing.net
3. Vietnam threatening China’s manufacturing dominance thanks to Nike, Adidas
China has developed in the last 30 years from a low-cost, low-quality manufacturing country to one that increasingly values quality control, technology and labor standards (related: China's Move Up the Value Chain). But with these improvements come inevitable cost increases, causing some companies to look elsewhere in Asia for their manufacturing needs.
Vietnam has in fact become the primary manufacturer of footwear for companies like Adidas and Nike. In the past seven years alone, Adidas has shifted nearly half of its sneaker production from China to Vietnam, with Nike trailing not far behind at around 40 percent.
Though the rise of Vietnamese manufacturing is most dramatic in the footwear industry, U.S. and Japanese fashion companies have also been opting for the cheaper labor in Vietnam. Uniqlo increased its major suppliers in Vietnam by 40 percent last year alone. And in 2017 the U.S. Fashion Industry Association issued a fashion benchmarking study reporting a new sourcing model of “China Plus Vietnam Plus Many”.
What does this mean for Chinese manufacturers?
Though the trend toward Vietnam is on the rise, China remains confident that Vietnam poses no threat to its manufacturing industry. China still dominates in more valuable and less labor-intensive items, like electronics. And Manufacturing Global cites China’s 2017 growth rate to be 6.7 percent, only slightly behind Vietnam’s 6.8 percent.
The only looming threat lies in the slowing growth rate of China’s workforce, with around 25 percent of the population expected to be above 60 years old by 2030. The effects of this population crises are not entirely predictable. But China’s cabinet has begun proposing possible solutions to combat the issue. These include lifting the nation’s birth limit policy that’s been in effect for over 40 years.
Whether Chinese manufacturers feel threatened or not, Vietnam is clearly making progress. For more data on these changes in manufacturing trends, visit the link below:
Nike and Adidas help to redraw Asia’s manufacturing map – Marc Bain, Quartz Media
4. A stagnant U.S. manufacturing industry: where it came from and where its headed
The U.S. manufacturing industry’s stagnation is no secret. Disappearing jobs and overall production levels lower than those of a decade ago are clear indications of its downturn. The 2000s brought a Chinese superpower with an abundance of labor and low-cost manufacturing that was simply unmatched.
But with the rise of automation, manufacturing is slowly shifting away from being an industry built on the backbone of low-skilled, middle-class workers. This shift might eliminate some of China’s natural advantages and slightly level the playing field. In fact, the U.S. share of manufacturing output among developed countries has actually risen since 1997.
Investing in automated manufacturing may not seem like an obvious solution to a struggling job market, but some economists say it is. High-technology export jobs produce income that fuels domestic spending, thus creating more local American jobs. But reviving the U.S. manufacturing industry won’t happen overnight.
What are the next steps to revising American manufacturing?
It’s impossible to predict what will truly turn the industry around. But a shift to producing more robots and promoting higher skilled labor may be the way to go.
The U.S. currently lags behind other countries in industrial robot supply. And even worse, most of its supply is produced abroad. A possible long-term plan might be to become the main global producer of manufacturing machinery. Or at least enter the ranks of competition.
The second approach is to focus more on creating high-skilled workers. Producing high-tech equipment is one thing, but having people who know how to operate it is another thing entirely. Improvements to the education system with greater emphasis on science, technology, engineering and math (STEM) fields are an obvious starting place. But promoting the immigration of skilled labor might be a more short-term solution.
To read more about possible solutions to U.S. manufacturing stagnation, check out the link below:
The U.S. Can Still Catch Up in Manufacturing – Noah Smith, Bloomberg
5. China’s unexpected PMI increase in May and what it means
China’s manufacturing Purchasing Manager’s Index (PMI) increases from 51.4 in April to 51.9 in May, despite Reuters economist’s prediction of decline. While a PMI increase isn’t always breaking news, this particular growth comes amidst rocky trade relations with the U.S.
To understand why this number is an important indicator, it helps to know exactly what a PMI is. As defined by Investopedia, the PMI is an indicator of the economic health of the manufacturing sector. It provides valuable information about current business conditions to both company decision makers and analysts. The number is calculated based on five major indicators: new orders, inventory levels, production, supplier deliveries and the employment environment.
That’s great, what does manufacturing PMI growth mean for China?
May’s PMI growth is the fastest the country has seen in six months, following a nearly 20-year low of investment in April. Economists assumed April’s numbers were a result of U.S. tariff threats. But this month’s data suggests that those two may not be entirely related.
Referring to China’s PMI exceeding expectations, Jian Chang, Barclay’s chief China economist, claims: “the stronger-than-expected PMI were [sic] somewhat consistent now with the government’s already preemptive measures to boost domestic demand and infrastructure investment.” The government is taking matters into its own hands and trying to keep its manufacturing industry thriving.
Though this is good news for May, it’s still unclear what China’s overall economic growth will look like at the end of this year. More tariffs could be introduced in the next few months. And economists predict 2018 growth to slow by 0.4 percent from the previous year. For more detailed information on China’s May PMI, see the Reuters article below.
China May official factory growth well above forecasts – Reuters Staff, Reuters
We’re constantly scanning the web for top manufacturing stories and news. If you’d like to submit an article for consideration for our weekly Best in Manufacturing, send us a message and let us know.
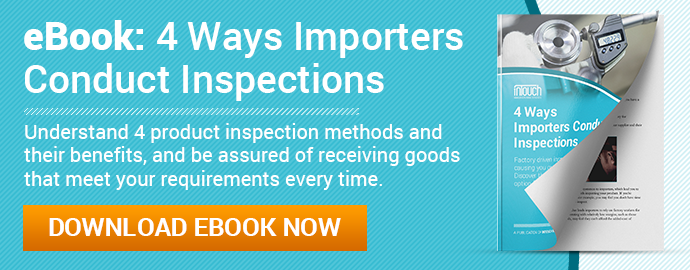