An inspection report is the most valuable tool a buyer can attain when manufacturing abroad. However, many buyers don’t really take advantage of this opportunity simply because they don’t know how to. We are here to change that and teach you what to look out for in order to get the most value out of your inspection reports.
There are many aspects that affect the quality of your goods in China. While performing ongoing inspections on your product will keep the factory on it's toes, it will not necessarily prevent defects from popping up throughout the manufacturing process.
Below are 4 steps that outline simple things you can do with inspection reports in order to help you get the most out of your investment using 3rd-party inspection.
1. Give feedback on quality issues found during product inspection
Suppliers not understanding your quality expectations is one of the leading causes of recurring quality issues in China.
Upon receiving your inspection report, carefully go through all of the “pending” issues and defects listed. Make sure to advise the factory exactly how you would fix them, if needed, and request any necessary re-work on the order.
Point out any unacceptable defects and do not be afraid to emphasize how this will affect your future relationship with the factory if they continue to arise. Holding your supplier accountable for not meeting expectations will greatly increase the chances of the factory working out a solution to those issues in future orders. (To learn more about improving quality, check out Combat Poor Product Quality Between Orders.)
2. Update your product specifications
Use the issues highlighted in the reports to update your own documentation. This will help you recognize what is realistic and what is unrealistic for the factory to accomplish and make any necessary changes to your product.
A common cause for nonconformities found during inspection is outdated specifications used by a factory for production. This can be related to the product itself or packaging and accessories. An example of this is when a garment manufacturer updates what kind of top stitching should be used on a pair of pants. A factory that fails to update the specifications could mistakenly continue to manufacture the pants with the old top stitching.
Ensuring that the file name has a clear version number that relates to the PO and is distinguishable from previous orders is a good way to ensure that the factory is working off the most current data.
3. Get to the root cause
Asking the factory to investigate the root cause is a good way to prevent the same issue from occurring time and time again.
Having the factory actually look into how that defect occurs will give them extra insight into their own manufacturing processes. Specific causes for defects found are often lost between the sales representative you speak with and the production floor. Is the warping in your furniture due to storing the finished product in a place with high humidity? Is the chipped coating on your metal display due to rough handling during production? These are examples of issues which production managers or a factory’s own internal QC staff should be able to identify and address.
Documenting common QC issues and their causes will ensure that staff on the production floor are aware that the issue is not acceptable and aware of the likely cause of the issue, better enabling them to prevent future defects.
4. Provide encouragement on positive points
Suppliers, like anyone, appreciate positive feedback. If there are no issues of concern highlighted in your inspection report and the result is "PASS", highlight the points where the factory has done a good job.
Quality can fade over time. If the factory is aware of the points it has done well, it will be more likely to maintain quality in those areas going forward. Keep the factory doing what it’s done well by letting them know.
Remember, communication is key. And part of effectively communicating with your supplier means letting them know when they've done something right.
Conclusion
As we know, Chinese manufacturers are capable of making some of the best quality products in the world (see Do Chinese Factories Care About Quality?). The main point is, quite often, there is a gap in suppliers’ understanding of your quality requirements. By following the above steps, you can greatly improve and maintain your product’s quality over time.
Product inspection reports can be a powerful and very useful tool. They are your eyes and ears in the factory where your products are being made. Just remember to:
- Give detailed feedback to your supplier
- Keep your specifications up-to-date
- Investigate how and why the defects occur; and
- Encourage your supplier when they do something right
Follow these four steps to get the most out of your product inspections every time.
What tips do you have for using product inspection reports effectively? Share in the comments below!
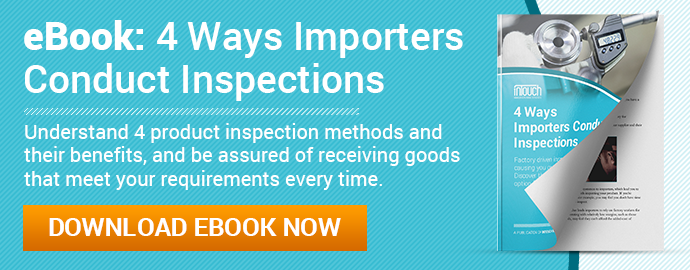