The terms quality control and quality assurance are often used interchangeably and this can be confusing. Although there are some similarities and both are important to an effective quality management system, it is important to understand the specifics of quality control vs. quality assurance if you want to build a reliable system.
This article will discuss some of the key differences between quality control and quality assurance and explain how AQF can help you get the necessary tools for effective quality management.
Quality Control vs. Quality Assurance: What’s the Difference?
Quality control and quality assurance are both designed to ensure that a product is safe and meets relevant quality standards. The main difference is that quality assurance is focused on being proactive and preventing defects while quality control is more reactive and focused on identifying defects.
In other words, quality assurance establishes a system of standard operating procedures that result in a quality product and quality control establishes a set of tests that uncover defects and identify whether or not the quality assurance system is working.
What is Quality Assurance?
According to the ISO 9000 Family of standards clause 3.2.11, Quality Assurance is defined as "A part of quality management focused on providing confidence that quality requirements will be fulfilled." It involves planning, documenting, and agreeing on a set of standards to assure quality.
Think of quality assurance as building a system of safeguards that maintain product quality and prevent defects.
What is Quality Control?
According to the ISO 9000 family of standards clause 3.2.10, quality control is defined as "A part of quality management focused on fulfilling quality requirements." It involves monitoring aspects of producing and testing the output to ensure identify and classify any defects that have occurred.
Even with effective quality assurance, you are likely to see the quality of products gradually fade if you aren’t practicing quality control. This fade happens because businesses wouldn't have the ability to monitor and verify that your preventative measures are having the desired effect.
When to Use Quality Control
If you are involved in a business that focuses on producing or selling, and buying goods and services, you should consider implementing quality control as a form of quality management.
Quality control will help you verify that all your products are uniform and of the required quality.
In the long run, you will be able to:
- Establish good customer relations
- Build your brand
- Build a good and reliable customer base
Aren't these the critical ingredients to a successful business? Enjoy all these benefits by adopting Quality Control in your industry.
Building an End-to-End Quality Management System
Preventative measures alone won’t prevent defects from occurring. Most quality assurance measures are generic and not specific to the requirements of the product being developed.
Quality control is necessary because it provides feedback and informs your quality assurance team on what is and is not working. Quality control measures are also concerned with the exact requirements of an individual product.
To learn more about improving product quality, contact us today or sign up for AQF online to book your next inspection.
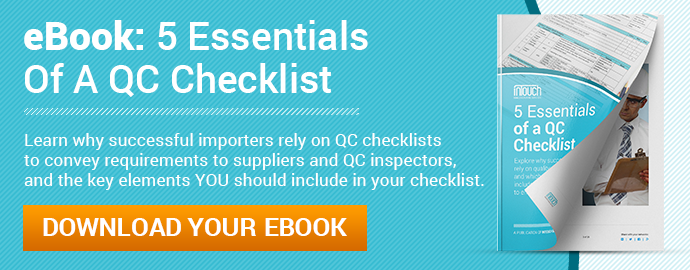